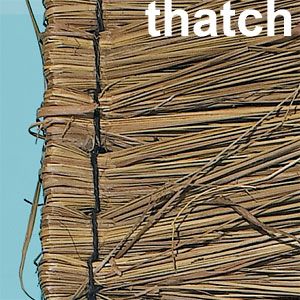
For most of us the roof is an afterthought—at least until it starts to leak. Then we realize how critical that surface of our house’s exterior really is. Yet, as well as keeping the house dry, the roof contributes greatly to the look of the house, so when building a new house, adding on, or re-roofing, it may pay to consider the options. Right now there are more options in the marketplace than ever, so choosing the best roof type is tough. I know because I am in the midst of selecting a roof for my cabin in Maine, and every time I know what I want I look at one of the other options and begin to change my mind! The choices range from asphalt shingles to wood shakes and clay tiles, from steel panels to rubber lookalike slate. The most important trend to note, however, is that as with home-construction materials in general, there is an increasing move towards engineered roofing materials. This change is being driven by a few different factors. One is simply the high cost of wood. The second is that in many cases, codes now mandate the use of fireproof construction materials. And third, people understandably want to build with materials that not only look good but also are very long-lived.
Asphalt Shingles
The roofing material we all see the most of these days—the one that covers the roofs of a great majority of houses across America—is the standard three-tab asphalt shingle. One of the least-expensive roofing options, asphalt shingles are available in a dozen or so different colors both solid and blended. The shingle products being made today are usually guaranteed for 20, or in some cases 30 years, making them an excellent value. Value is the principal advantage of this roofing material, which explains it’s commonality. The disadvantage, however, if there could be said to be one, is the fact that it is so common. The next upgrade from a standard three-tab is a thicker variation called an architectural shingle. These shingles are built up to be about twice as thick as a normal shingle with the layers staggered to give them a heavier, more substantial or “architectural” look. In some colors they resemble slate, and in other colors wood shakes. We used architectural shingles on the Lexington ranch house. With only a modest upgrade in cost and up to a 30-year guarantee, architectural shingles also represent an excellent value with an added touch of style.
Shingles, Shakes…
For looks, it is hard to beat a wood shingle roof. Over time it weathers out to a gray or soft silver that seems to root the house to the landscape. Several species are used: Western Red Cedar, Alaskan Yellow Cedar and Eastern White Cedar. Shingles are relatively smooth and cut to a uniform thickness, although they vary in width. Wood shakes are thicker and rougher, being split rather than sawn from the logs. Wood roofs are meant to breathe and should be laid over a substrate that allows air to circulate behind them: skip sheathing—wood strips or battens nailed directly to the roof rafters—is the traditional method of installing a wood shingle roof. About 10 years ago we began using a plastic matrix product that is something like a scrubby pad, which allows air to circulate behind the shingles. This product can be laid on top of a building-paper-coated plywood roof deck, making it ideal for a retrofit. Another method of getting air circulation behind the shingles is to lay them on pressure-treated lattice. For all their great looks, shingles and shakes are expensive to install and do require some periodic maintenance, typically in the form of washing to remove any mildew or moss, and then re-oiling with a clear wood finishing product. On our current Shingle-style project here in Manchester, Massachusetts, we’re using a wood shingle that is new to us: pressure-treated Southern Yellow Pine, which grays out in a few years to resemble cedar and is said to require no maintenance at all. A properly installed and maintained wood roof should last at least 30 to 50 years. In fact, we have seen roofs on which the shingles were still good after 25 years or so, but the galvanized nails were finally rusting, so be sure to use a high-quality stainless-steel nail!
…And Fakes
Originally, our Craftsman-style bungalow in Santa Barbara, California, would have been clad in a combination of wood shingles and shakes, because the building needed that shaggy rough-hewn appearance to look authentic. However, because of fire danger, local codes now require all roofing materials to be fireproof. Accordingly, we used a heavy architectural asphalt shingle on the roof, and a cementitious shingle manufactured to look like a wood shake for the side walls — although they are suitable for use on the roof as well. Use of these “fake” shakes is rapidly increasing, both because they satisfy the strict fire codes in the West and because they are long lived and require no maintenance.
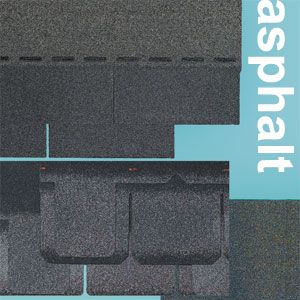
Slate and Fake Slate
In the Northeast slate was a traditional roofing material for high-end houses and municipal buildings. It is beautiful, lasts for generations, sheds ice and snow, and is very expensive. Because of its cost and weight, which requires a beefier roof structure to support, slate is not often used these days. Yet on our Billerica project, rebuilding Dick Silva’s burnt-out family home, we wanted the slate look. Again we turned to an “engineered” product, this time a slate lookalike fabricated from recycled rubber and plastic. At only about one-third the weight and cost of slate, these shingles can be installed using standard tools and techniques. From the street, the discerning eye might be able to tell the difference between engineered and the real McCoy, but most of us would be very house-proud with one of these roofs on our homes. Plus, these shingles are guaranteed to last for as long as 50 years.
Metal
Metal roofs, in the form of corrugated, galvanized sheets, have been a standard feature of barns, sheds and other agricultural and utility buildings for years. Metal roofs can be cheap, rugged, long-lasting and easy to install—perfect for a utility application. On the other end of the spectrum is a copper roof, elegant enough to grace the country’s finest mansions and public buildings. Graceful bay and bow windows are often roofed with sheet copper soldered at the seams. We used such roofs on both the Billerica and the Lexington houses. Larger expanses of roof are covered using the “standing-seam” method, in which one sheet joins with its parallel mate via an interlocking, water-tight seam. Metal is a great choice for a house in a snow country, as well as in an agricultural country. Fortunately, in terms of products available, there is much to choose from between the galvanized low-end and the copper high-end. On our Milton project, we used a formed-in-place, standing-seam steel roof on the workshop addition to the barn. While not as dear as copper, this roof was expensive — and beautiful. There are a variety of powder-coated steel roof “systems” on the market, some very cost-effective variations on the galvanized sheet-steel theme. Others are factory-built standing-seam roofs, custom-made to your house or barn and installed by a roofing contractor. The advantage of these systems is that they require no special fabricating equipment and can be installed by any qualified contractor. (I am even considering using one on the shed I have to build in Maine.) In addition to standing-seam roofs, several types of metal shingles are also available. One, an interlocking tin shingle we used on the roof at our Key West project I have never seen anywhere other than the Keys. Another variation commercially available nationwide is an interlocking copper shingle. Regardless of the style you choose, in general, a properly installed metal roof should last you at least 50 years.
Ceramic
Ceramic tile roofs are found throughout the Mediterranean and Levant—and, of course, in the Mediterranean-Revival-influenced architecture of Florida and California. Barrel tiles, the most common type of ceramic tile, resemble half cylinders about 16 inches long. In the old days they were individually made by hand, their tapered shape achieved by forming the clay over the top of the thigh. We actually used some of these handmade tiles on our renovation of a hurricane-damaged Mediterranean-Revival house in Miami. And more recently, we used high-quality reproduction barrel tiles on our West Palm Beach project. Tile roofs are quite heavy, so the roof framing must be stout enough to support the load. Waterproofing is achieved via a waterproof membrane laid directly on the roof sheathing. Then the clay tiles are laid one by one in a pad of mortar. Tiles turned upside down form a trough, which is then covered by tiles laid right side up. The whole process is quite labor intensive, which makes an authentic tile roof quite expensive — about $1,000 per 10×10-foot square, or about three times the cost of a standard three-tab shingle job. In addition to barrel tiles there are a number of variations of clay roof tiles. Some are shaped like thick shingles, some like slates. A high-quality tile will be hard-fired and will not absorb moisture that could fracture the tile when frozen. Thus such tiles are suitable for northern climates. All high-quality tile roofs are expensive, both in terms of the material and the installation, and so clay tile roofs are fairly rare. Yet in the long run the most expensive might be the most cost-effective, since you can expect to get 60 to 80 years or even more out of a well installed tile roof. I know of a hard-fired clay shingle roof on a seaside mansion not far from our current project in Manchester.
Steve Thomas is the host of This Old House.