
Bruce Torrey held up a chunk of fiberglass insulation that he’d just ripped from a crawl space off the third floor of Madeline Krauss and Paul Friedberg’s soon-to-be-renovated Shingle-style home. Turning it over, he showed Maddy the dirty black streaks that coated its edge. “Wow, what is that?” she asked with concern. “Was there a fire?”
Thankfully, the house—the site of This Old House TV’s 2007 project house—hadn’t been damaged by flames. But the ugly smudges were a warning that the three-story house could still burn its new owners—with outsized heating and cooling bills. The marks were soot streaks, caused by drafts whipping against the fiberglass insulation, which collected the dirt particles from the air. Finding such drafts is part of Torrey’s job as senior building investigator for Building Diagnostics, the Cape Cod–based company the couple hired to conduct an energy audit on their house before construction began so they could learn where they needed to tighten up.
Leaks and drafts that let heat escape in the winter and trickle in during the summer aren’t easily detected, because they’re usually the result of problems behind walls or in other hard-to-reach places. “Heat loss and drafts are by their nature invisible,” says Torrey, who worked with TOH general contractor Tom Silva to identify problems in the 1897 house. Together, they ran a diagnostic energy audit, which relies on a combination of sophisticated equipment and good old-fashioned detective work. For a cost of about $400, such an audit provides homeowners with a written report detailing a home’s problem areas and laying out cost-effective solutions.
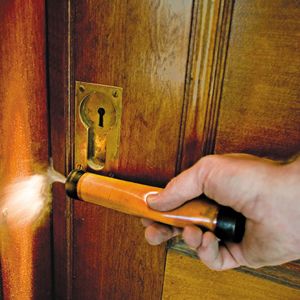
Here’s a look at how the audit at Paul and Maddy’s home took inventory of potential trouble spots.
Exterior Walls
Even when a house has been insulated, the materials’ thermal effectiveness can be diminished by settling, wetness, or spotty installation. So the first place Torrey looks during an energy audit is inside the walls, to see where insulation is missing or has become compromised over time. To do this, he sets up a “blower door” test, creating an artificial windy day. He closes all the windows and doors, inside and out, then covers one exterior door opening with a thick plastic sheet that has a large fan embedded in it. By blowing air out the door, the fan lowers the air pressure inside the house. Gaps reveal themselves as fresh air begins to seep in to fill the vacuum. A pressure gauge measures how much air moves inside. (Similarly, Torrey uses a “duct blaster” on forced-air systems to check for ductwork leaks.)
With the blower door running, Torrey can scan the entire house with a camcorder-size infrared camera, which produces an image that registers temperature differences inside walls, attics, ceilings—anywhere leaks occur. Though an energy audit will work in any weather, the best time to do one is during hot or cold extremes so that there is a distinct temperature difference between inside and outside. In the winter, anywhere cold air is coming in appears black on the infrared image. In the summer, hot air moving through walls looks white. By keeping an eye on these spots, he can pinpoint where insulation has failed or is missing.
One way to make up for missing insulation is to blow loose cellulose into small holes drilled in the walls and behind the siding. However, walking through this house on a hot summer day, Torrey confirmed what Tom suspected: A previous owner had already retrofitted blown-in fiberglass, but there were gaps in the protection at the top and bottom of the spaces between the studs. Together the pair identified trouble spots, then Tom marked the walls so he could come back and replace the fiberglass with slow-expanding urethane foam, which seals crevices and joints so breezes can’t slip through. The product (Icynene and Demilec are two brands) costs more than fiberglass, but “you’ll get a tighter job,” says Tom. “You could cut your energy loss by half.”
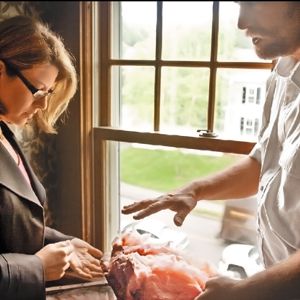
Attics, Knee Walls, Eaves
Leaks at key places where framing comes together—attics, knee walls, cantilevers, and eaves—can account for a home’s biggest heat losses. These hard-to-reach spots may not have enough insulation, or what’s there might be installed incorrectly. Not surprisingly, Torrey’s infrared camera showed missing or underperforming insulation in all these places.
Again, Tom will come back and remove the dirt-coated fiberglass Torrey found so he can insulate the eaves and the knee walls with expanding foam. Since Maddy and Paul will place their new, efficient HVAC equipment in the attic, Tom will also coat the underside of the roof sheathing. Torrey notes that for attics that don’t double as mechanicals rooms, it’s better to seal the flat attic floor; blown-in cellulose provides great results for this application, he says. For homeowners who can’t afford all-new insulation, Torrey recommends a hybrid approach for gaps in these framing details. “Sometimes it’s a long crack, sometimes large chaseways,” he says. A combination of expanding foam, rigid boards, and blown-in cellulose can assure that an air barrier and insulation work as one.
Windows
Windows tend to leak, but not necessarily through thin glass. “Typically, air moves through headers and below sills,” Tom says. So, not surprisingly, the infrared camera showed no insulation in the cavities above and below the windows at this house. Torrey then took out a candle-size smoke stick, which emits a wispy column of nontoxic white powder when it’s squeezed, to help locate small drafts. When he held it up to the window casing the trail of smoke quickly bent toward the trim and disappeared behind it, telling him that there were uninsulated voids. The renovation plan calls for replacement windows that fit inside the existing frames. But first, Tom will drill a series of ½-inch holes all the way around the inside of the jamb—top, bottom, and sides—so he can inject expanding foam into the cavities.

Wiring, Plumbing
The smoke stick comes in handy when examining where wiring or plumbing chases cut through walls, floors, or ceilings—locations notorious for leaking conditioned air into the attic and letting outside air seep inside. Torrey used it to check the areas around light fixtures and radiator pipes and found a few trouble spots. Some will be taken care of where rooms will be gutted, but Tom will have to come back and either seal around the areas from above with canned foam insulation or caulk around them from below.
The Payoff
Energy-saving investments can show results quickly. “Air-sealing improvements can pay for themselves in one or two heating seasons,” Torrey says. Larger-scale insulation upgrades can pay off in 4 to 7 years; new windows, in 7 to 15 years. With upgraded insulation and windows, plus other energy-saving measures, Maddy and Paul’s house will certainly be more comfortable—and they could cut their energy costs by as much as 50 percent, compared with previous owners’ utility bills. “Our move from a smaller home to this house is like switching from driving a VW to an SUV,” says Maddy. “We want to reduce our energy use not only for the environment but for our budget, too.”
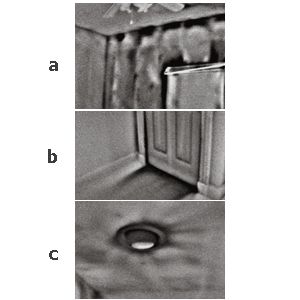
How to Find an Energy Audit Pro In Your Area
To find reliable energy pros near you, start with resources such as the Residential Energy Services Network (RESNET) at natresnet.org. This national standards-making body for buildings’ energy-efficiency rating systems offers an online Certified Rater Directory. Search by state for local listings.
In addition to asking for references—Tom Silva recommends asking former clients if they’ve had any problems with mold, mildew, or drafts after following the recommendations—be sure to find out about the diagnostic tools they use and what the assessment will show.