If you’ve ever warmed yourself in front of an open fire, you’ve experienced radiant heat. Unlike rising hot air, radiant heat travels in all directions, warming cooler objects around it. Delivered via warm water in plastic tubing installed in a floor, radiant floor heating moves out from there, making the room feel warm and comfortable.
Though installing a radiant floor heating system can run up to 50 percent more than, for example, conventional forced-air heat, it saves 30 percent in energy costs, eventually paying for itself. Putting it into new construction is easy: Special wood plates screwed to the joists double as subflooring. But retrofitting the tubing under an existing floor presents challenges. If a room is gutted down to the joists, it’s easy enough to lay down the wood plates. But that’s not possible when flooring stays put.
3 Places to Retrofit Radiant Floor Heat in Existing Homes
Here’s a look at the three most popular places for retrofitting radiant and what the pros do in each case to bring cozy warmth to older houses.
1. Radiant Heat in First-Floor Living Spaces
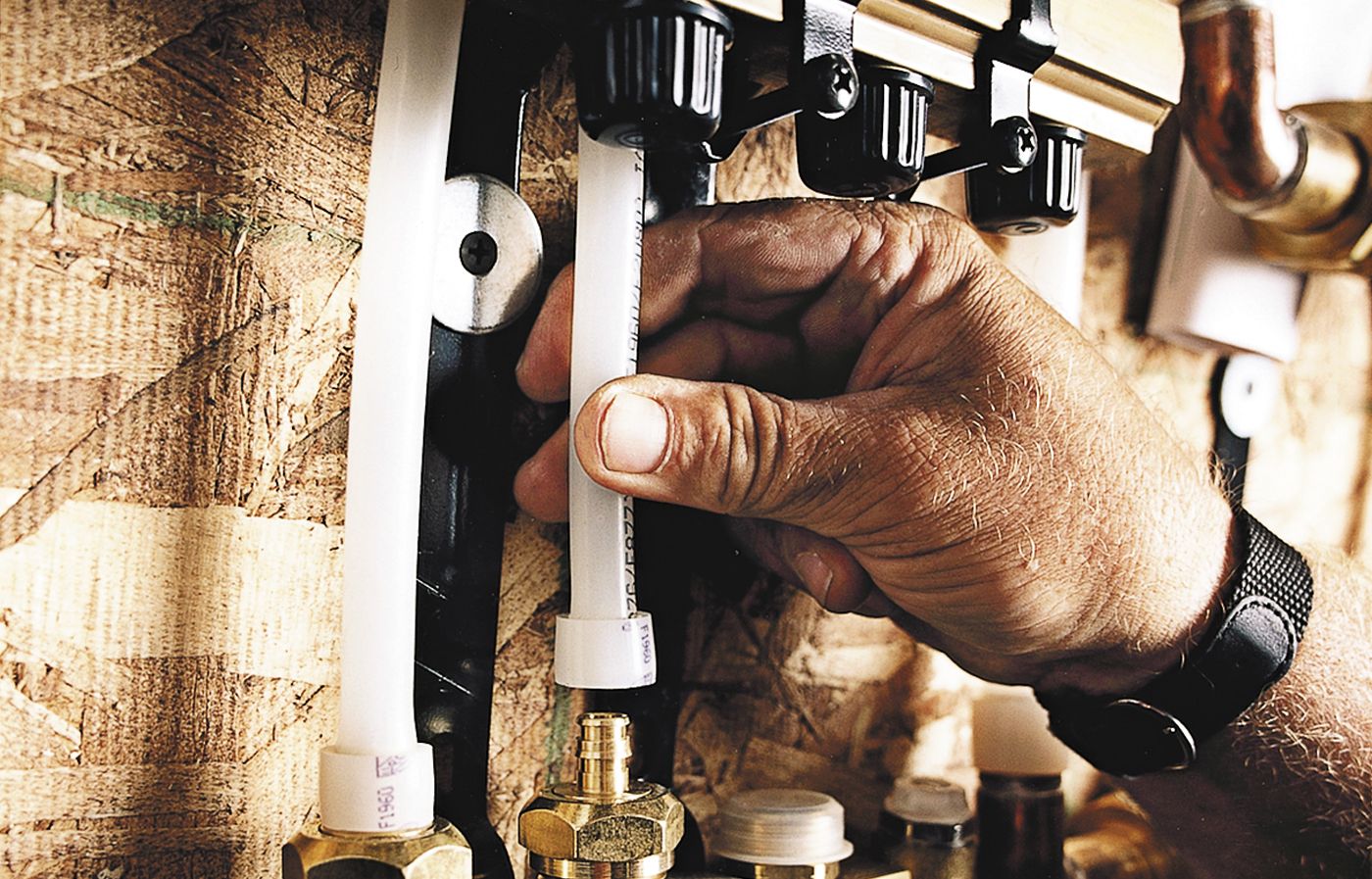
The best way to retrofit radiant floor heating without disturbing an existing floor is to do it from below, against the underside of the subfloor. In most houses, the only place to do this is on a first floor where joist bays are open to the space below. It can go under most existing flooring, including wood, tile, vinyl, and even carpet.
Installing radiant floor heating in existing homes begins with aluminum tracks being screwed between the joists, which hold PEX (cross-linked polyethylene) tubing carrying hot water. “Plastic like PEX is not a good transfer medium,” says Richard. “So the aluminum sucks the heat out and conducts it to the subfloor.” The tracks keep the tubing evenly spaced at 6 to 8 inches to avoid cold spots. The tubing snakes uninterrupted from bay to bay through holes drilled at least 2 inches from the edges of each joist. In a kitchen or family room, though, Richard takes care not to run it under cabinets or other built-ins. “You don’t want to trap the heat under a sealed box,” he explains.
Insulation beneath the tubing is critical to keeping the heat moving up into the floor, rather than dispersing every which way. At the project house, the crew will spray foam insulation over the tubing between the joists, forming a tight seal.
A radiant floor heating system needs a hot-water supply, a connection between the tubing and the plumbing, and a pump to move the water from one to the other. In a first-floor retrofit, all these either already exist or are easy to locate nearby.
The TOH project house has a manifold in the basement where all the tubing originates and returns. It connects to a circulator pump. Each room’s tubing feeds into the manifold’s supply, loops around under the floor, and reconnects at the return. Every room or zone has a separate thermostat; turning it up sends warm water to the room, raising the room temperature. Turning it down shuts the water off.
The manifold gets its hot water from the boiler, which has a special mixing valve that’s set to deliver water at no higher than 140 degrees F. This limit, explains Richard, ensures that the floor’s surface doesn’t rise above 85 degrees, which can break down tile mastics and warp wood. At the project house, the temperature in the tubing will rise and fall with the weather—running between 85 and 90 degrees on winter’s mild days and as high as 130 or 140 on the coldest days.
2. Warming Up Second-Floor Bathrooms and Bedrooms
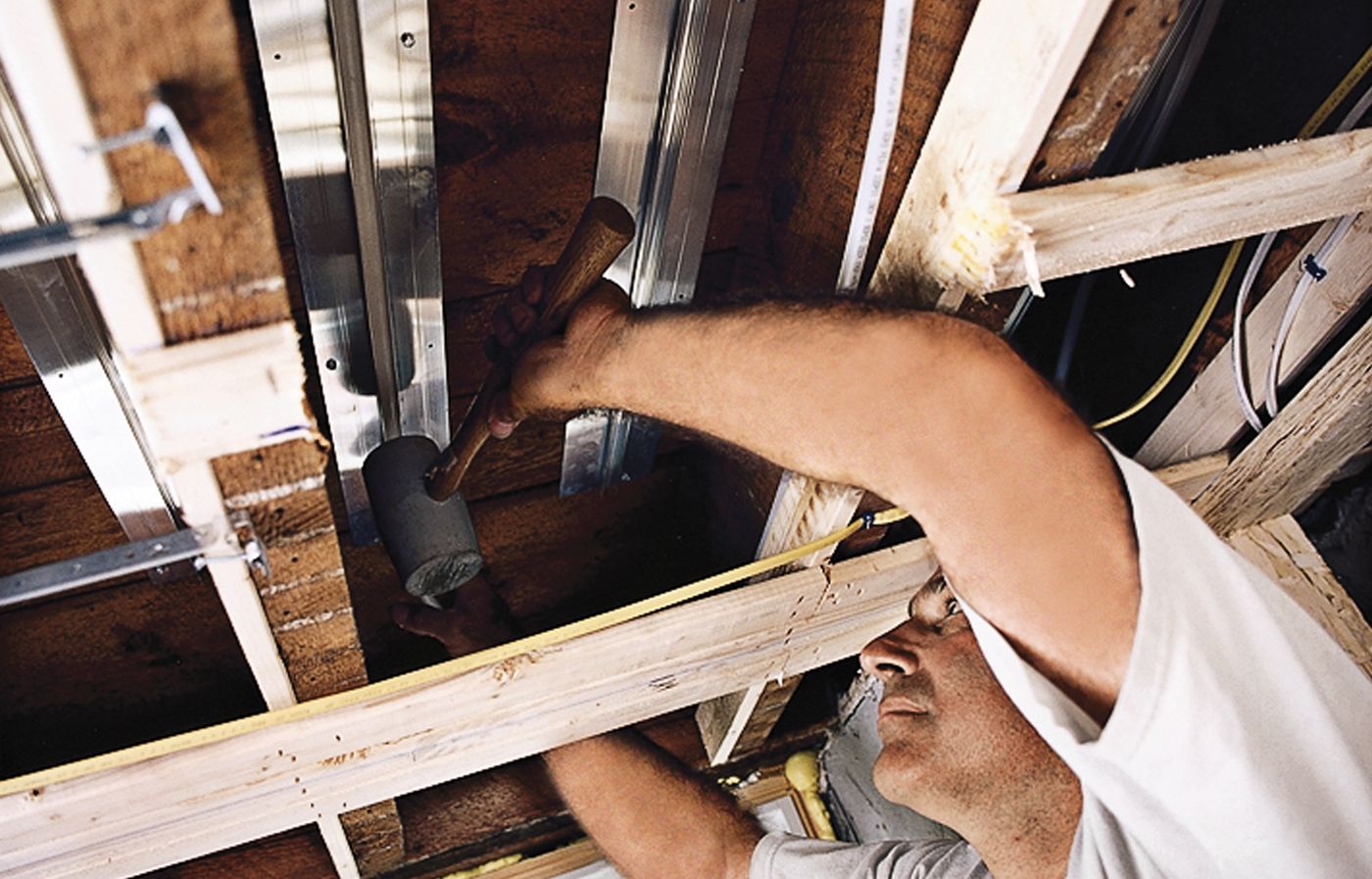
Retrofitting radiant on a second floor, where the comfort of warm bathroom tiles or wood flooring under bare feet is a treat, can be trickier. Rarely is there access to second-floor joists from below, so the tubing must go in from above. This could add from ½ inch to 1¼ inches to the floor grade, says Richard, requiring adjustments, such as raising or cutting down doors. (These limitations also apply to a first floor with no basement. So in a kitchen, for example, you must be sure that raising the floor doesn’t pin a dishwasher into place.)
Fortunately there are products—Uponor’s Quik Trak, Viega’s Climate Panel, and Rehau’s Raupanel are some—that keep the added height below ¾ inch. According to Rehau project manager John Kimball, these panels can go over most any subfloor—planks, plywood, OSB, or even concrete—as long as it’s level and in sound condition.
Once the panels are nailed or screwed down, you can cover them with a variety of finish floors. Because tiles give up their heat readily, they’re ideal for radiant heat—so a bathroom is a great place for a retrofit. However, a tile floor includes backer board, thinset, and the tile itself, so it will add more height to the room than, say, linoleum, which goes down over ¼-inch plywood, or wood, which can be laid right over the panels (as long as installers don’t nail through the tubing).
That said, just about any conventional floor covering will accommodate radiant. For wood floors, Richard recommends hardwoods like oak, ash, or maple. “The narrower the plank, the better,” he says. “It keeps expansion and contraction to a minimum.” Carpeting will also work, as long as the combined insulating value for the carpet and pad—information carpet dealers or radiant contractors should have—doesn’t exceed R-2.5. “If the floor is too well insulated,” says Richard, “it’s like putting a sweater over a radiator.”
Connecting a second-floor radiant system to the heat source is just a matter of finding a way to get the water from the boiler. Basically, wherever PEX tubes can be installed, radiant heat can travel. Richard recommends installing a manifold “in a closet, or tucked into a stud cavity—close to the area being heated.” This avoids snaking multiple lengths of tubing down to and back from a distant manifold. Then a single line can supply the water from the boiler to the manifold.
3. Creating a Heated Basement Floor
“Any basement that will have a family room, playroom, or workshop should have radiant,” says Richard. If the basement will get a concrete slab, the PEX can go down before the pour, attached to a wire mesh or clipped onto rigid foam insulation. The flooring then goes right on top of this slab.
If there’s already a slab in place, the tubing goes over it, using the same low-profile panels used for a second-floor retrofit. Then you can finish the flooring in the same way you would on a second floor, or you can pour lightweight concrete over the panel. “Covering the tubing with lightweight concrete or gypsum concrete allows its heat to be absorbed by the concrete’s thermal mass. It also protects the tubing, but it raises the finished floor height,” says Richard. “So you’ll need to adjust every door opening.”
In the end, the Newton homeowners decided to put the radiant under the entire first floor and under a second-floor bathroom, but left it out of the basement. The installation will add to the cost of upgrading their heating system, but in the cold Northeast climate they’ll see the savings in the first energy bill of the winter. However, says Richard, monetary payback is not really what radiant’s all about. “There’s no question that it’s the most efficient way to heat and has the lowest operating costs,” he says. “But the main reason you do it is for everyday comfort.”
Electric Radiant Heating Alternative
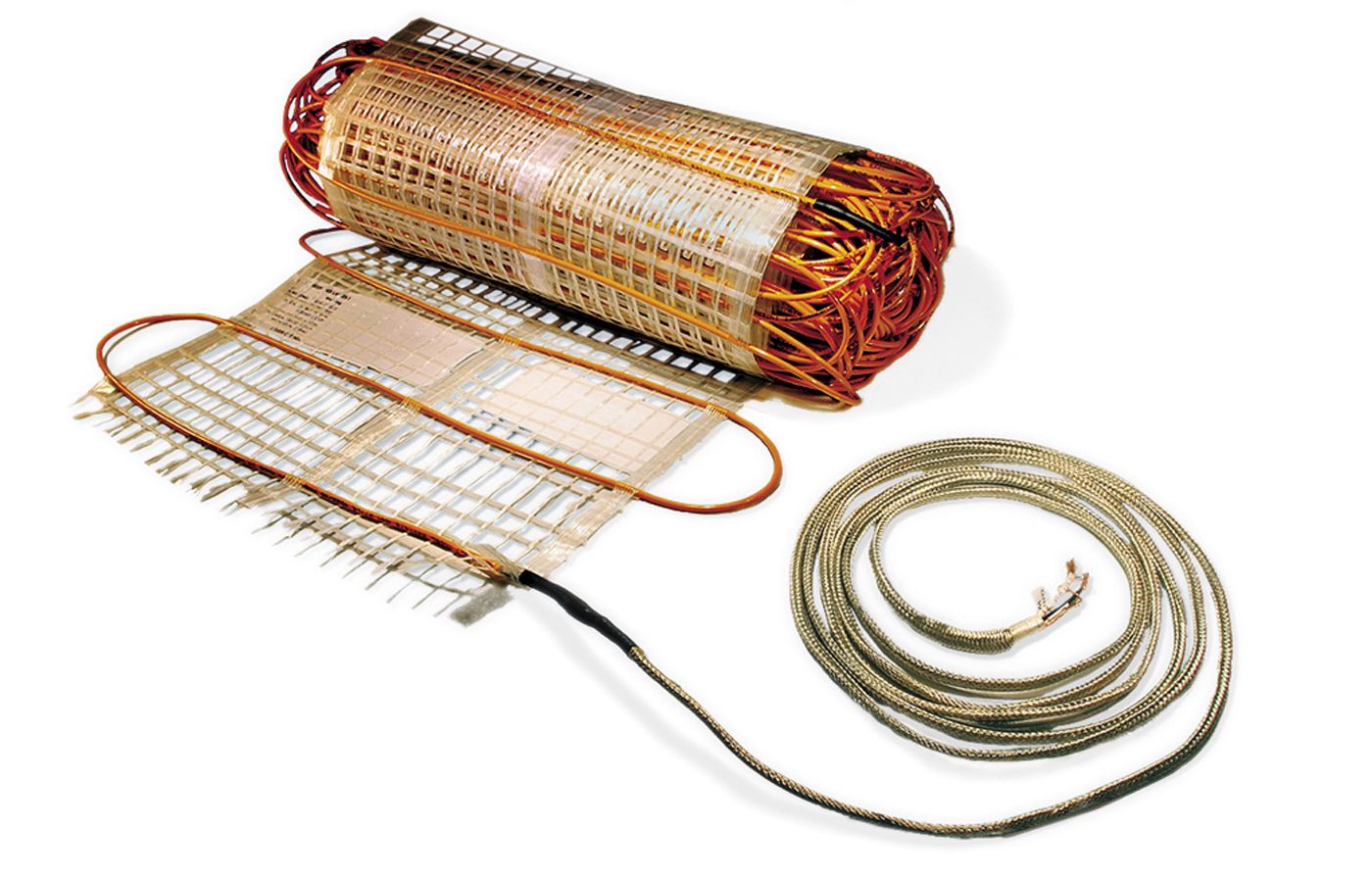
Generally, electric radiant heating—either cables installed in the floor or thin mats of resistance wire mounted on fiberglass netting—is retrofitted in single rooms rather than whole homes. It’s faster and less expensive to install, and it makes a good retrofit for a bathroom, say, or a small dressing room. But TOH‘s Richard Trethewey doesn’t recommend electric radiant for larger spaces, like a kitchen or a finished basement. “With the high cost per kilowatt-hour, it isn’t a good principal heating source—particularly in cold climates,” says Richard. “Hydronic radiant is so efficient because it uses water to transfer heat throughout the building. And water is the ultimate transfer medium. Period.”