Before Starting the Remodel
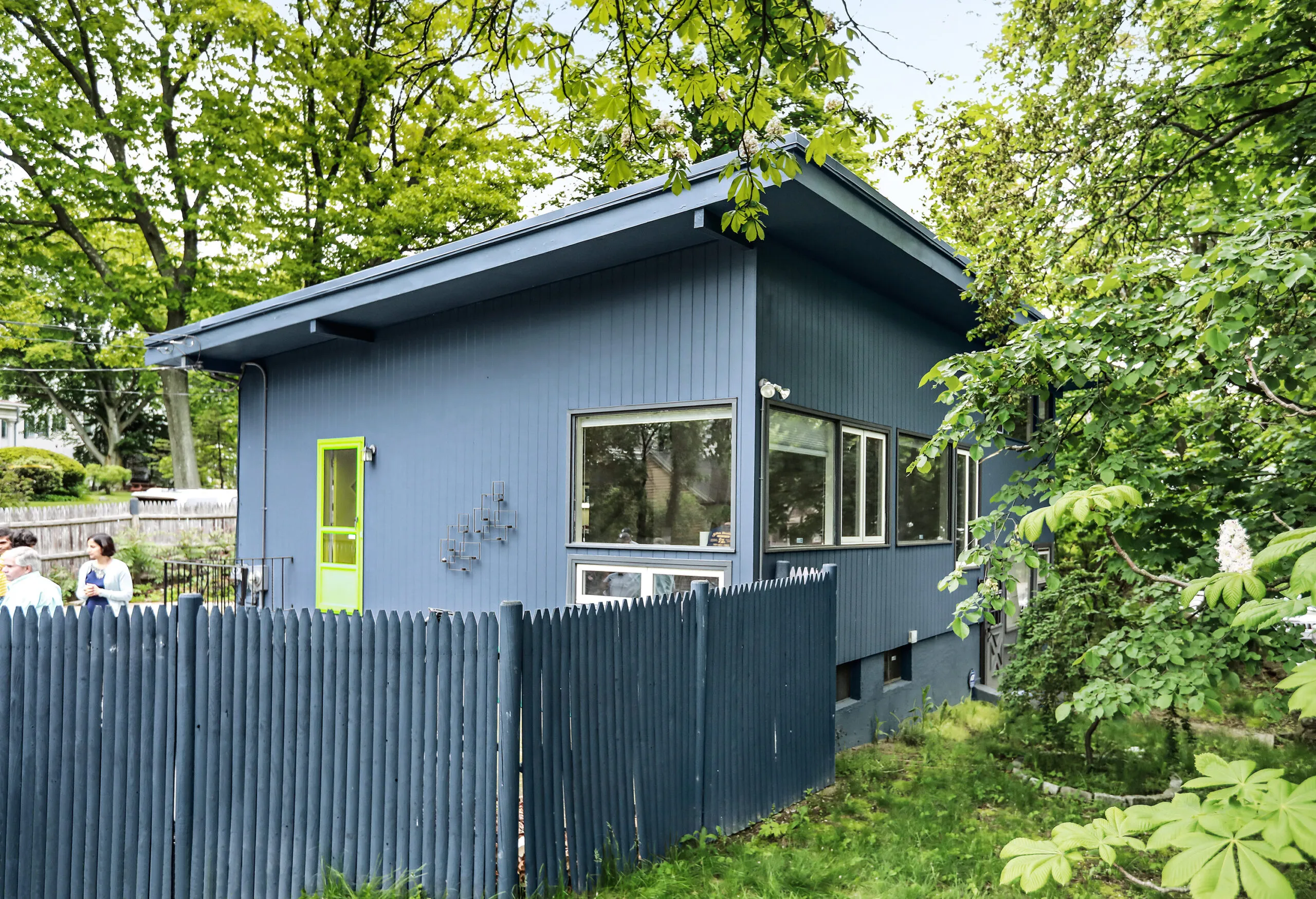
A funny thing happened to Dr. Sunil Ghelani and his wife, Dr. Neha Kwatra, on their way home from a real estate open house two years ago: They fell for a house they’d had no intention of buying. The couple had just visited one disappointing house in the Boston suburb of Brookline, when they drove past another open for viewing. “From the outside it was a gray box, and we didn’t think we’d be interested, but we had a little time so we stopped by,” Sunil recalls. For this pair of physicians (he’s a pediatric cardiologist, she’s a pediatric radiologist) and parents of a toddler (Nisa, age 3), spare time is a rarity.
Shown: The house’s north side served as the main entry for the previous owners. The vertical siding and horizontal band of windows are typical of the mid-century modern style.
Foundation Work
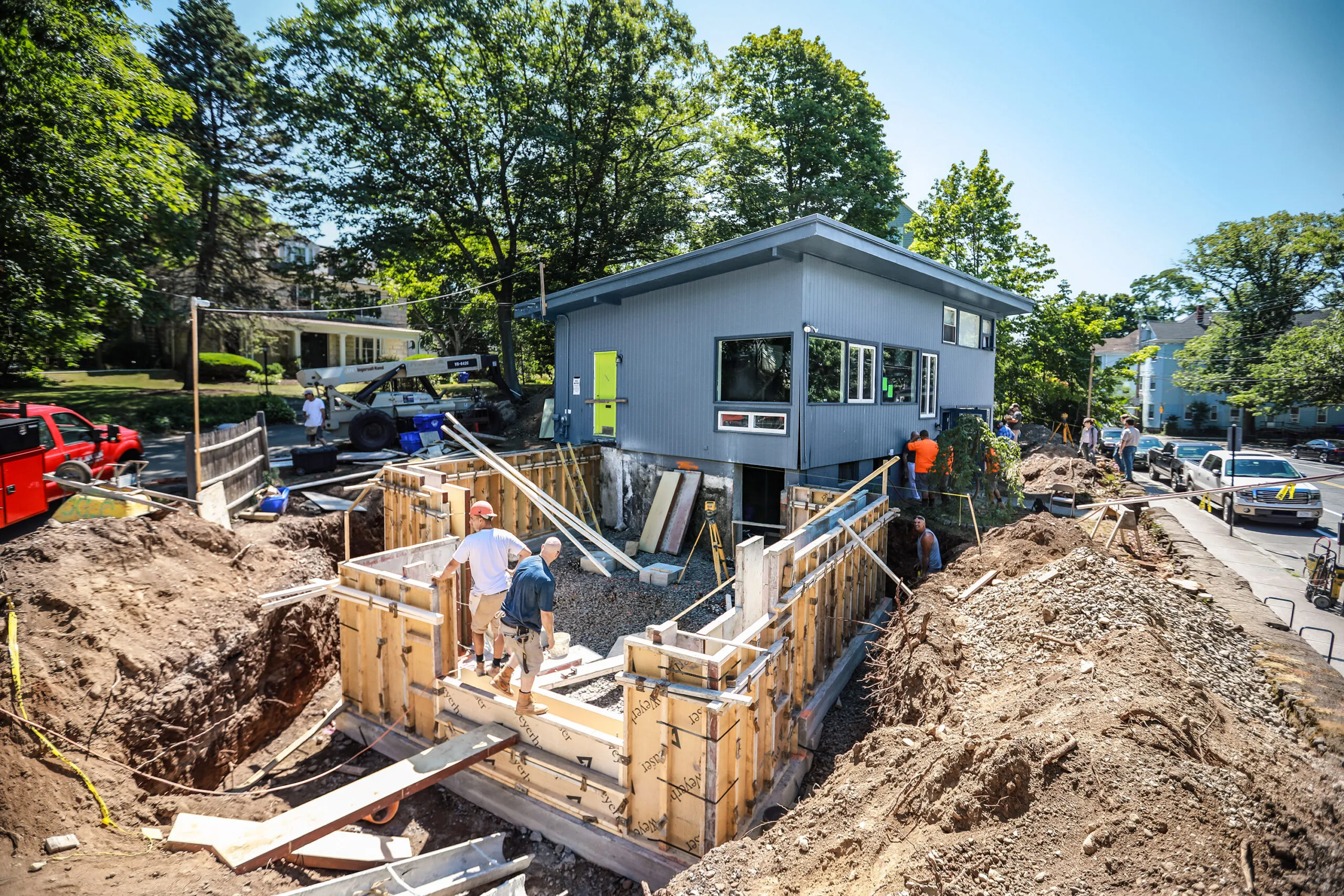
“We stepped inside, saw the 12-foot-high ceilings and the open space, and instantly thought if we could expand in the areas we wanted, it could be our dream house,” says Sunil. The location—a mile from Boston Children’s Hospital, where they both work, and on a bus line, near a park, in a good school district—added to the appeal. “We were aware the house was in a historic district, and that it would likely be a difficult renovation,” he says. “But we bought it anyway!”
Shown: The crew sets the forms for the north addition’s insulating concrete foundation walls; foam insulation panels will boost the walls’ R-value even more. The addition will hold a garage beneath the new living room.
Doctors at Home
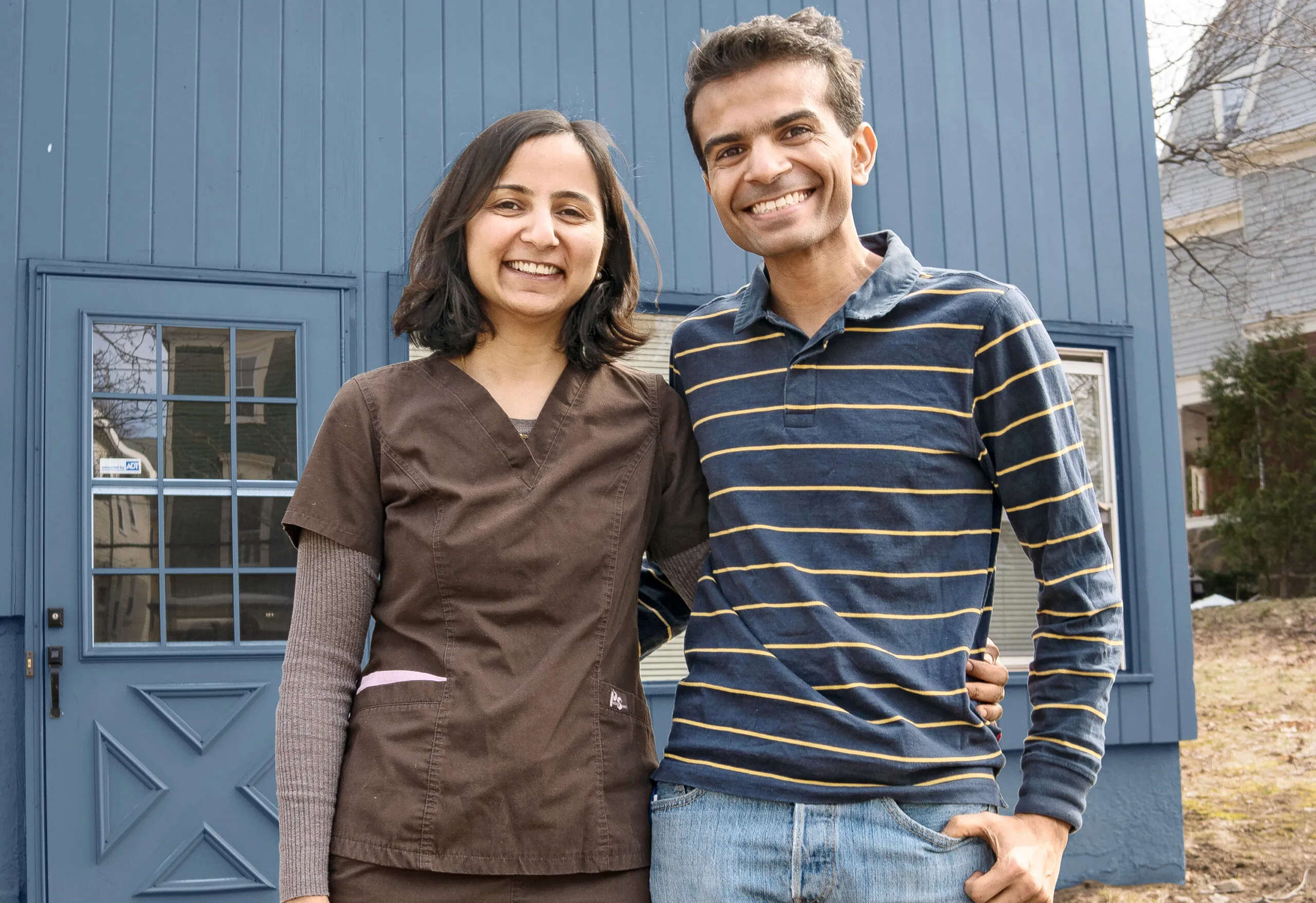
While the house had some heritage—it was designed in the 1950s by noted architect Jan Reiner—the “gray box” had some shortcomings, too. At approximately 1,400 square feet, it was small, with a tiny kitchen, four split levels, four cramped bedrooms with windows that didn’t meet modern egress code, concrete floors with layers of linoleum in some areas, shoddy wood floors in others, and electric baseboard heat.
Shown: Homeowners Dr. Neha Kwatra (left) and Dr. Sunil Ghelani.
I-Beam Install
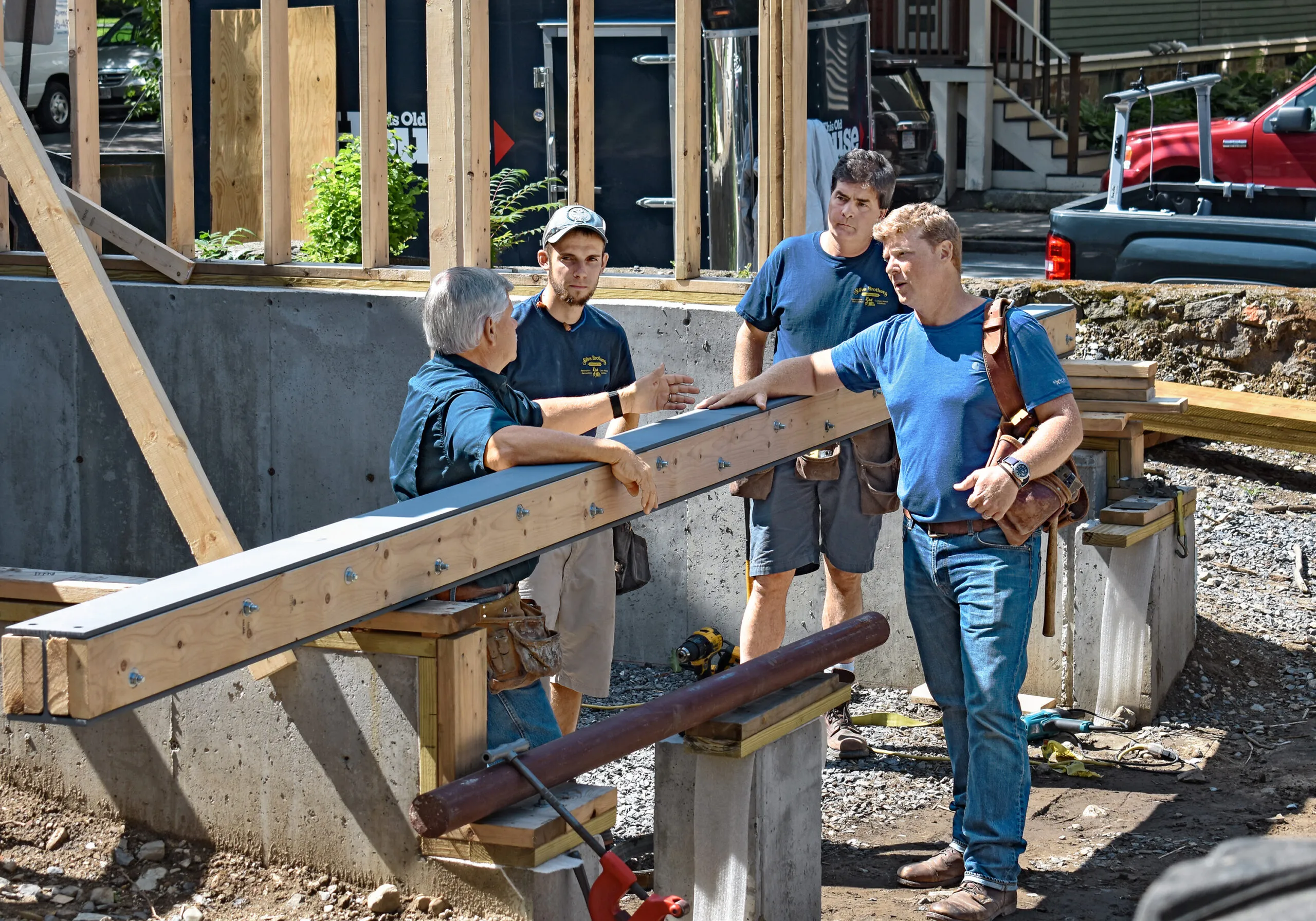
Working with local architect Linda Hamlin, Sunil and Neha decided on a plan that would more than double the home’s size to about 3,200 square feet by way of two hexagonal additions that echo the geometry of the original house. Avid cooks, they envisioned a large kitchen-dining area as the heart of the home, in the existing gray box. Embracing the open-plan, split-level style of architecture, they opted for a new living area in the 1,050-square-foot north addition adjacent to and up a few steps from the kitchen, with a soaring ceiling and a wall of glass doors leading to a balcony; underneath will be a one-car garage. To welcome family for extended visits, they allocated space for a private guest suite on the lower level of the 750-square-foot south addition, the upper story of which will hold their master suite, plus a bedroom and bath for Nisa.
Shown: Standing at the garage-door end of the concrete foundation for the north addition, the team of (from left) Tom Silva, GenNEXT apprentice Erick Ellison, Charlie Silva, and TOH host Kevin O’Connor gets ready to slide a wood-packed I-beam into position inside the existing basement to support the kitchen floor.
Richard Installs the Mini-Duct System
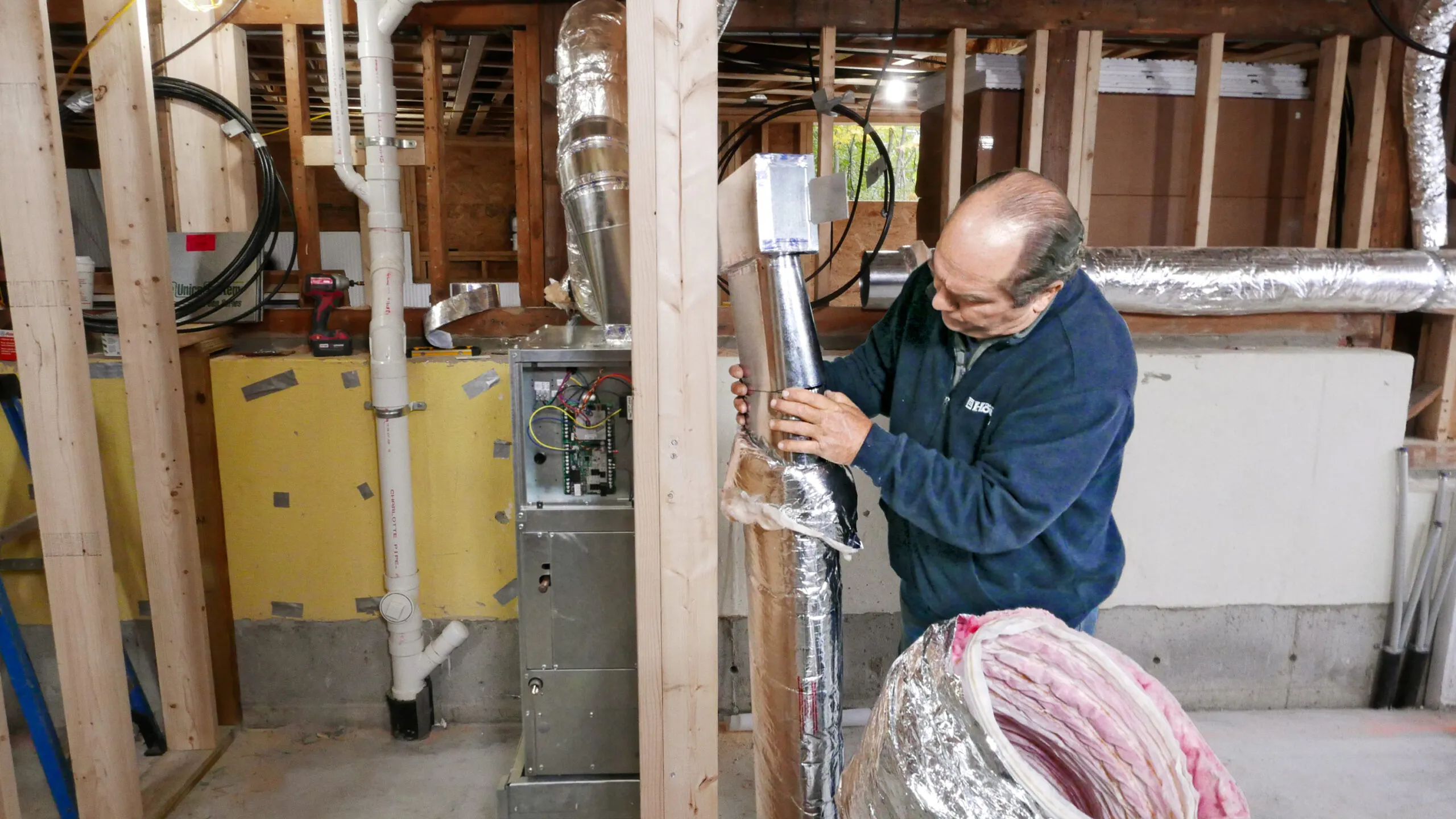
“Sunil and Neha definitely wanted to emphasize openness, and we did that with ceiling height and glass,” says Hamlin, who is very familiar with the house, having lived on the street where it sits for almost 30 years. “Since it’s in a historic district, we had to be sensitive to the original structure—essentially a square box with a shed roof—and make sure the additions didn’t dwarf it,” says Hamlin. The terraced corner lot called for further creative problem-solving, with its odd shape, which Hamlin describes as “half a guitar,” and its location at the intersection of a private street and a busy thoroughfare. “There was complicated geometry in many ways,” she says.
Shown: Richard Trethewey installs the return air connection to the mini-duct system for cooling, positioning the ductwork to carry air straight up into living spaces above.
Mini-duct AC: The Unico System
Kevin Jackhammers
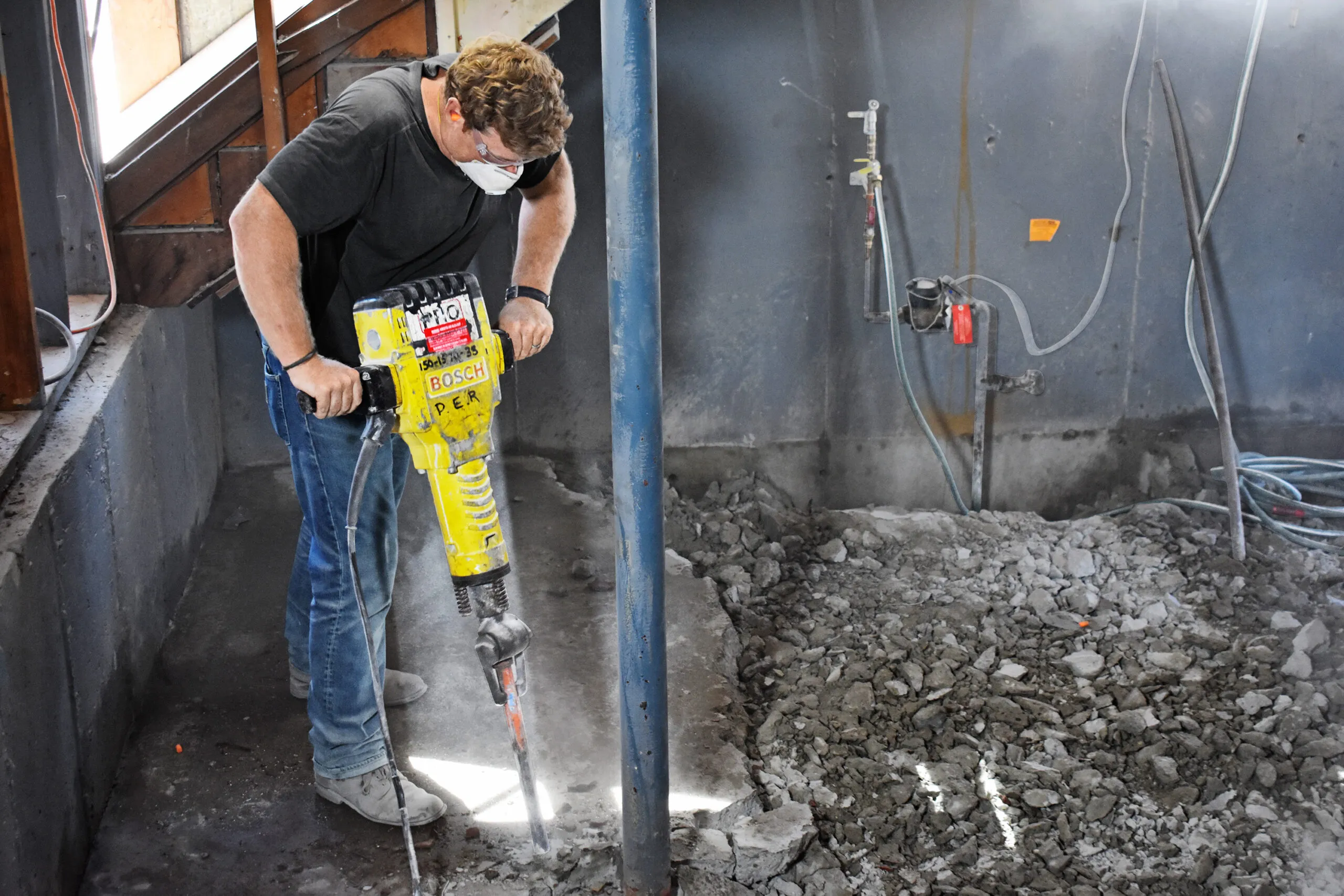
They also had to respect the look of the original front of the house—the west facade—which featured vertical cedar siding and horizontal bands of windows. “To complement that look, we chose horizontal cedar siding and vertical windows for the two additions,” says Hamlin. While the west facade, which faces a busy street, is prominent in the eyes of the Brookline Preservation Commission, Sunil and Neha are turning the east facade—facing the quiet private street—into their front entry, with a hallway leading to the kitchen-dining area.
Shown: Kevin O’Connor jackhammers the existing basement floor to gain headroom for finished spaces on the lower level.
Tom Checks Level
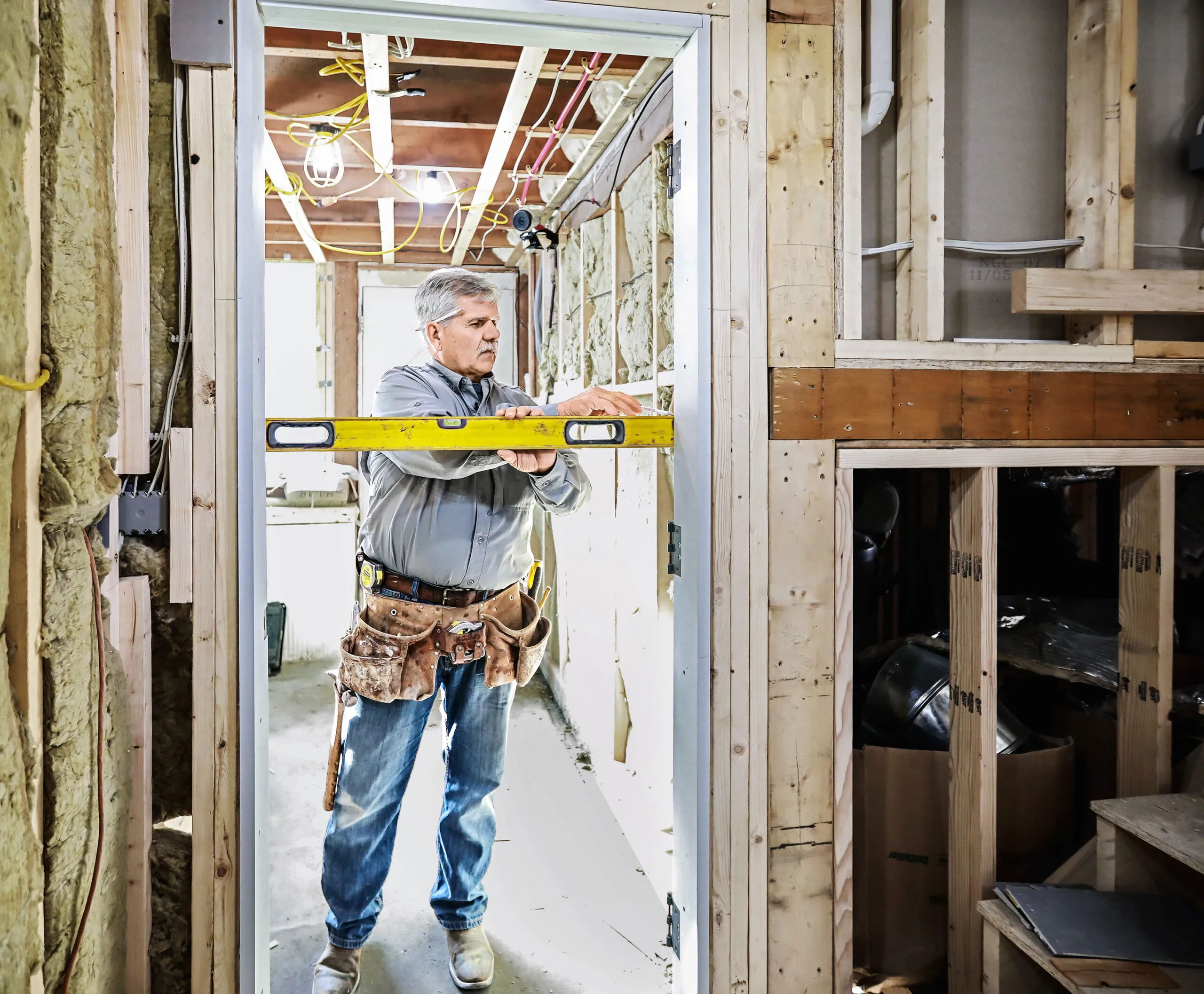
The ambitious renovation plan presented some holdups for the TOH TV team right from the start—beginning with demolition to take the house down to the studs. Based on This Old House general contractor Tom Silva’s suspicions, they called in an expert who confirmed the presence of asbestos, which was common in 1950s building materials-, requiring a hazardous-material crew to come in and remove it. Another delay cropped up after an inspector found deterioration in the main sewer and water lines, which meant they had to be replaced.
Shown: Tom Silva checks the level of a new door frame in the basement; the space behind him will become a playroom.
Norm and Tom Measure a Post
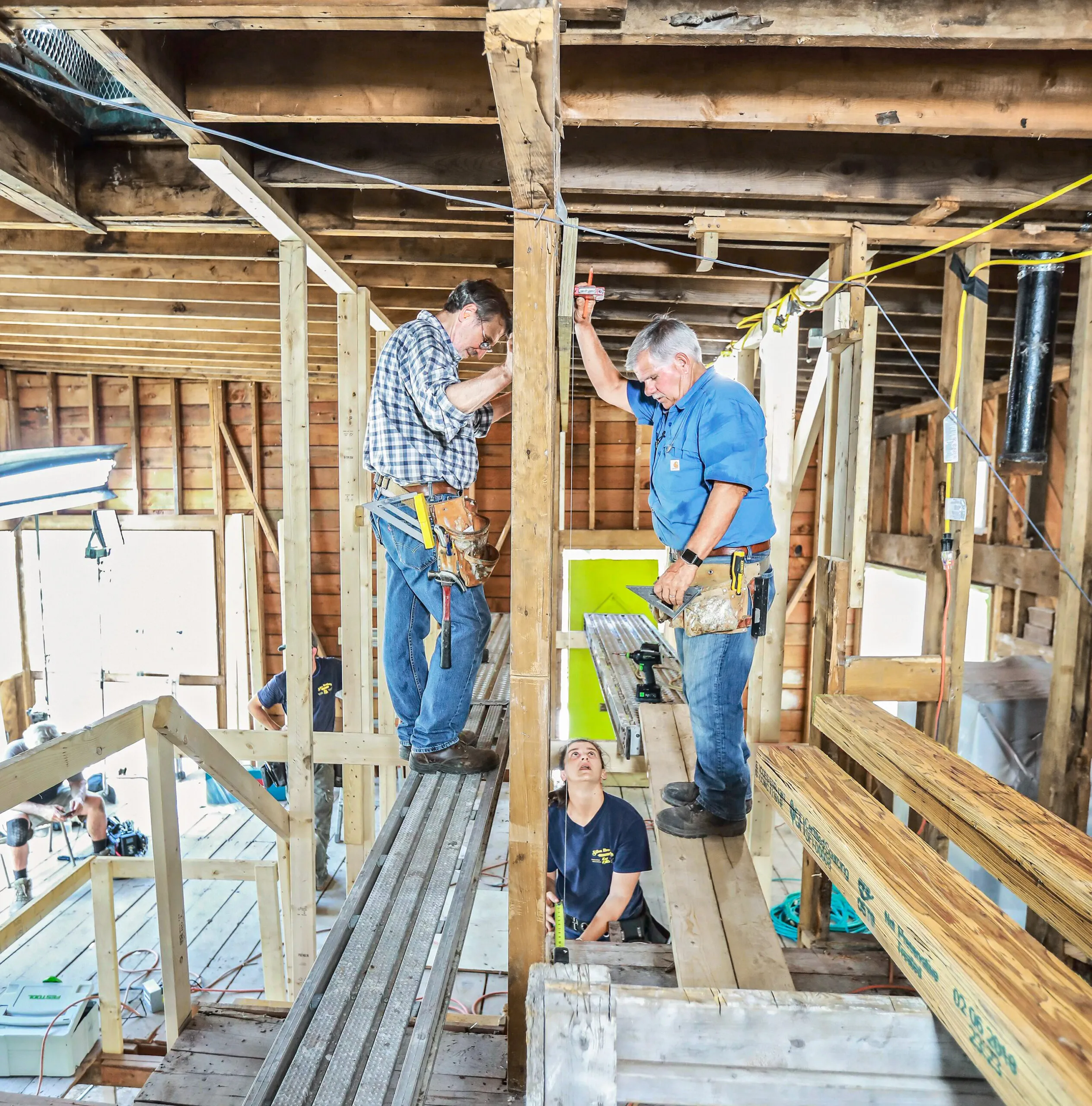
When building got under way, concrete foundations were poured for the additions, with the team adding insulated foam panels on the new and existing foundation walls as needed. They chose a one-step continuous panel system that goes in ready for drywall, with preformed channels to run conduit.
Shown: TOH master carpenter Norm Abram, GenNEXT apprentice Carly Comitino, and Tom Silva measure a post to jack up an existing beam in the kitchen-dining area in preparation for sistering the beam with two laminated-veneer-lumber (LVL) beams.
More Tips for the Apprentices
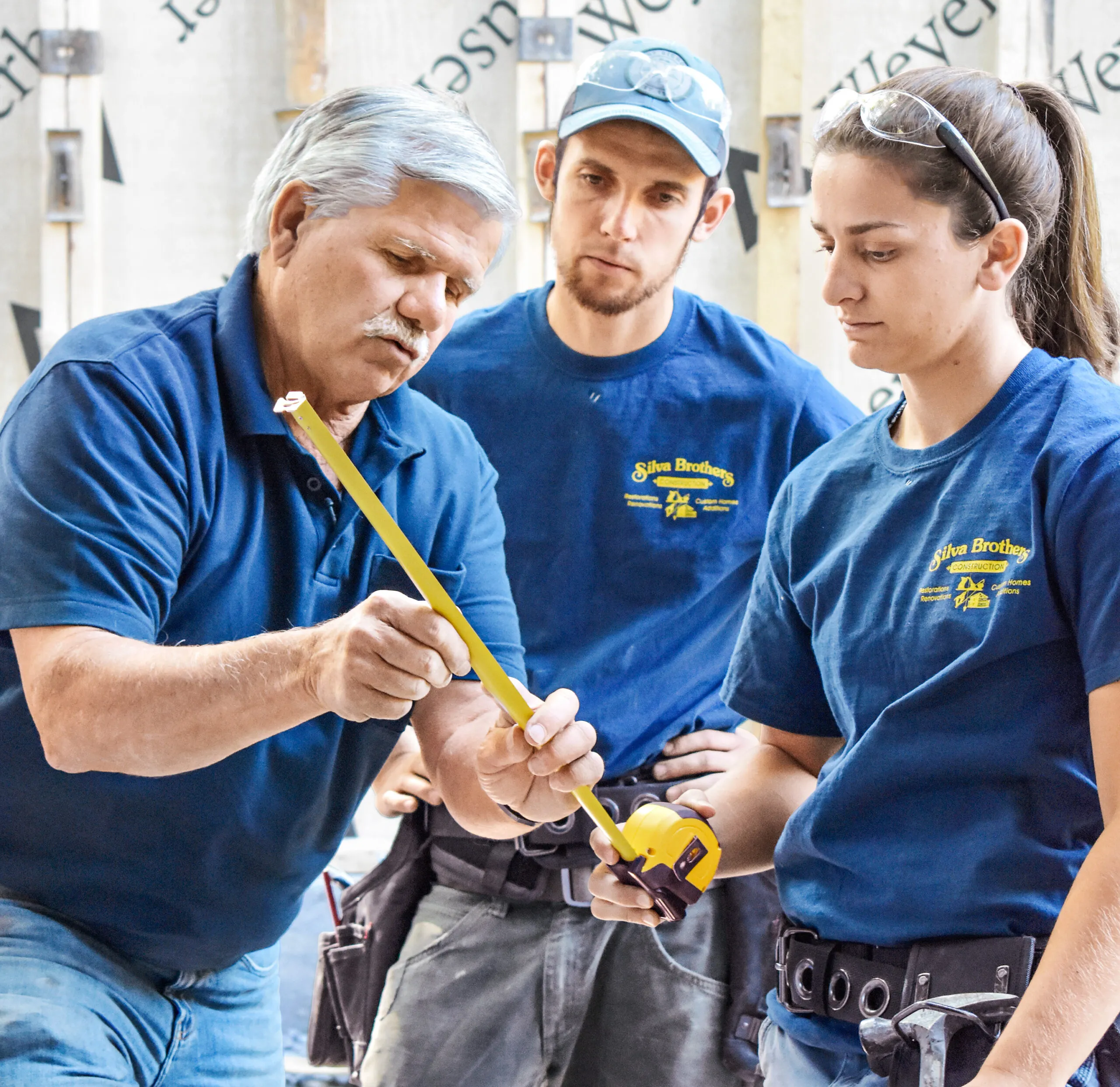
Throughout the project, they faced two sets of challenges: structural support and headroom adjustments. For example, the upper level of the north addition required special structural engineering. “With the plan calling for the big open living area above the garage, and a wall of glass doors from the living area to a balcony, we used a combination of structural lumber, LVLs, and steel,” says TOH home builder Charlie Silva. To gain headroom in the existing basement, they took a multifaceted approach, jackhammering to dig down, replacing a low-hanging beam with a steel beam installed between the joists, and cutting into the ceiling to create clearance.
Shown: Tom Silva teaches GenNEXT apprentices Erick Ellison and Carly Comitino a different use for a tape measure—it will help them mark where to scribe the existing foundation wall.
Driveway Prep
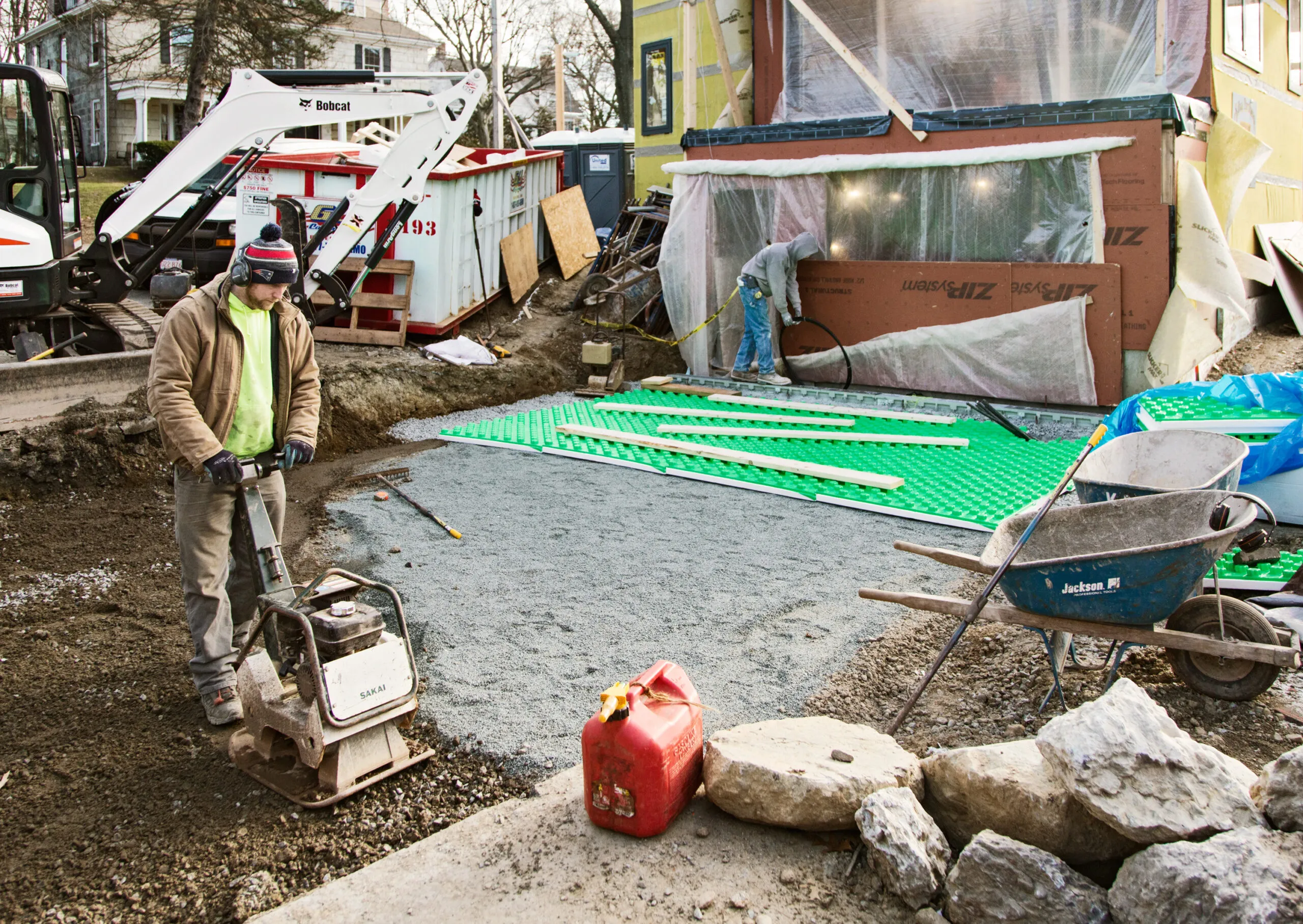
Even greater hurdles came once the additions were framed and the team had to stare down some mid-century modern, split-level, flat-roof facts of life: “There’s no attic, no unfinished basement space, eight different levels, and nothing conventional about running ductwork. For mechanical systems, this was a huge challenge,” says TOH plumbing and heating expert Richard Trethewey. Radiant floor heat made sense given the split-level layout—and resulted in 11 different heating zones—but to run the ductwork for the cooling system, Charlie and Richard had to get creative. “We fit things in closets, made soffits and chases on the lower level to feed up to the kitchen, created specially built soffits, and chose the locations for the two air handlers based on where we could run the ductwork,” says Charlie.
Shown: The crew compacts gravel and adds green insulation panels to the driveway in preparation for a snow-melting radiant heat system.
Insulated floor panels: Crete-Heat
Driveway snow-melting system: Viega
Adding Sills
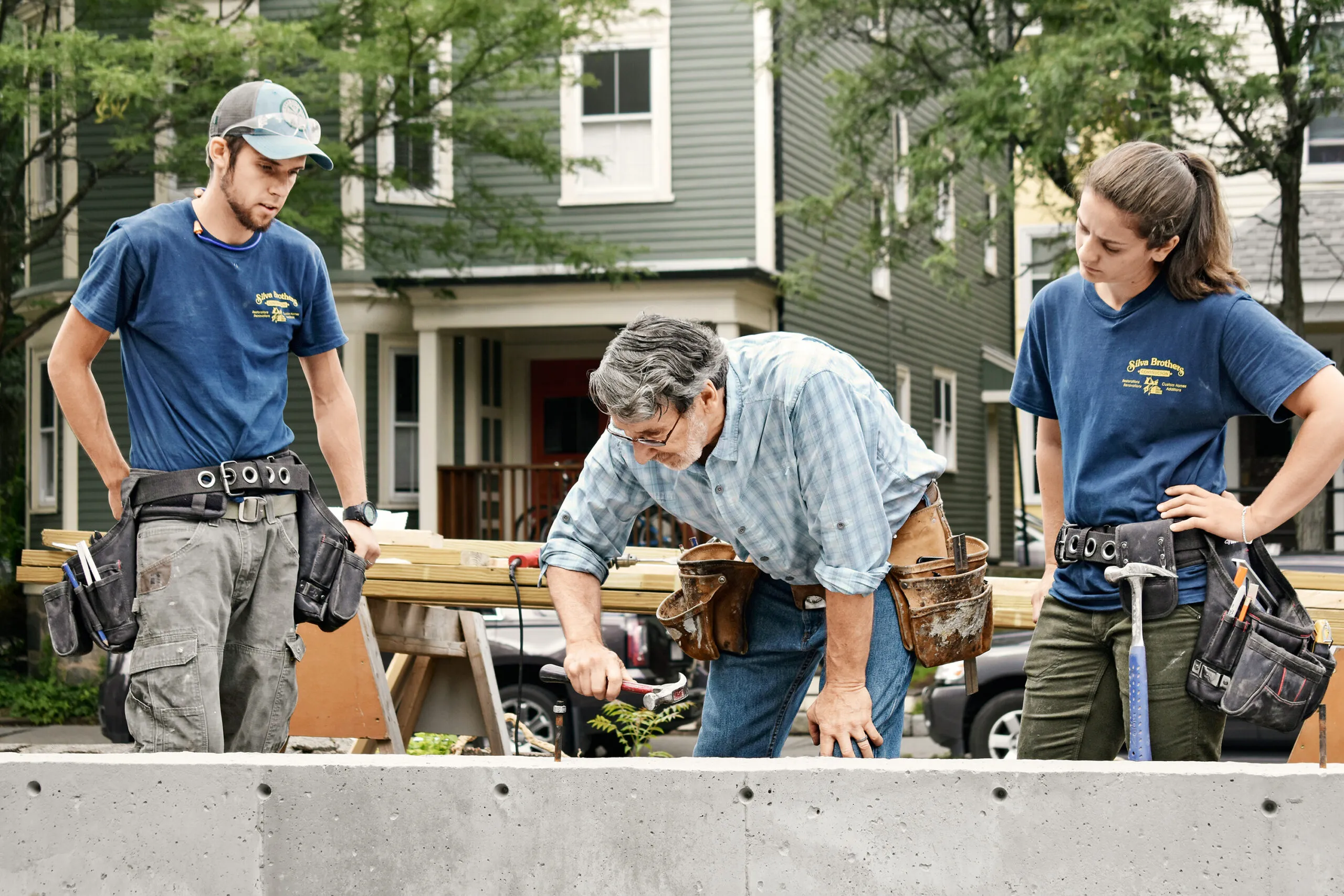
They solved an extreme version of the where-to-place-the-ductwork puzzle in the kitchen, where the plan called for a bank of west-facing windows from counter height up, along the cooktop wall. For the vent hood, Charlie ran ductwork straight up into the ceiling, then turned it 90 degrees and ran it along the entire 25-foot width of the house in the roof framing, terminating through the back wall. “That’s the fun of it, making the house work right,” he says.
Shown: Norm Abram gives apprentices Erick Ellison and Carly Comitino a lesson in one of the first steps of the house-building process: adding sills to the concrete foundation.
Finished Render
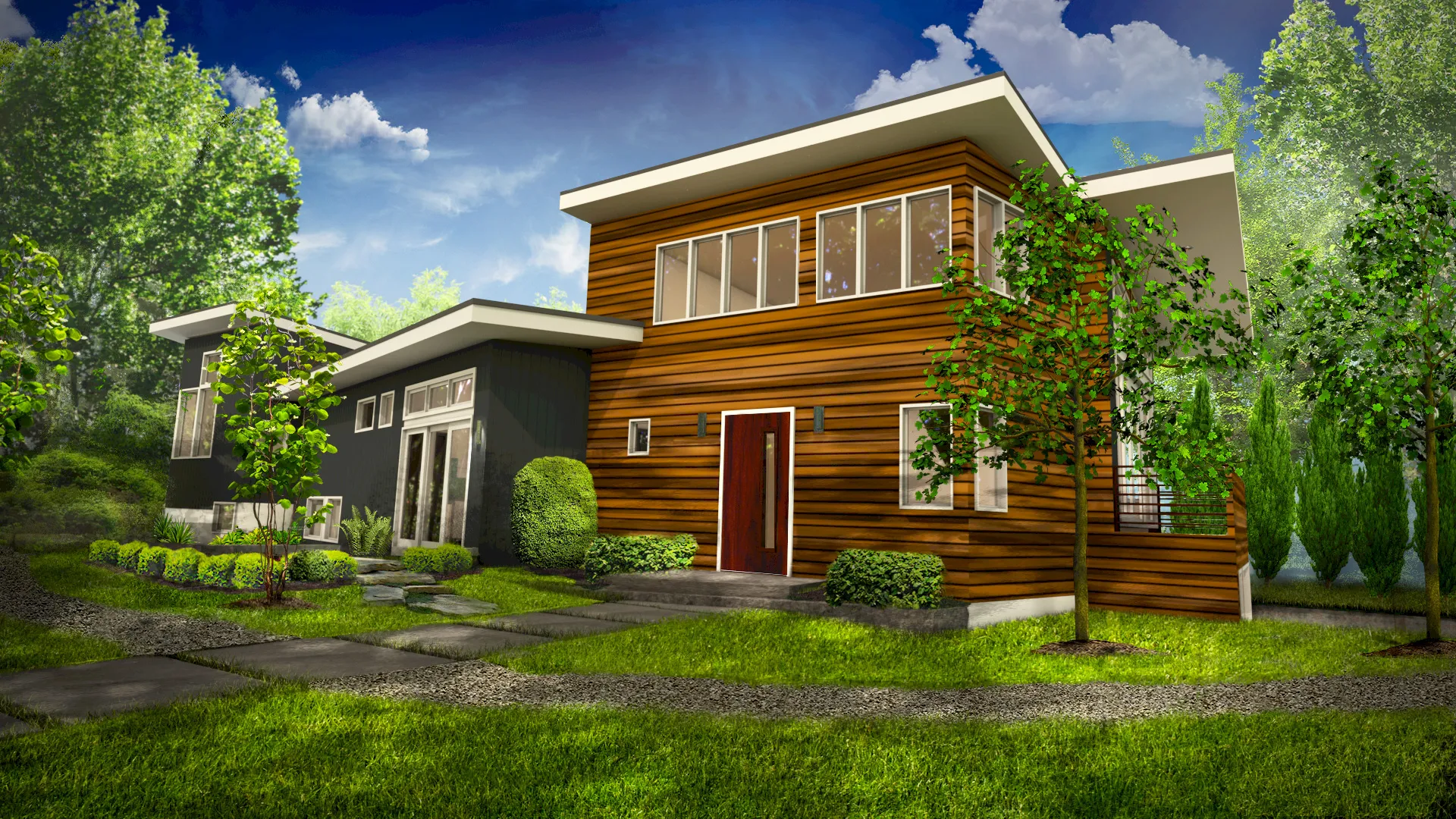
The house’s minimalist look requires a different approach for everyone working on it. “The big thing about this project is that it’s a mid-century modern with simple trim, but the simple is a little more difficult in that it hands off the final step to the plasterer,” says Tom. Instead of leaving rough window and door openings awaiting casing and trim after the walls are finished, the team had to precisely frame the openings, then step aside to let the plasterer create the flush look called for. “It changes the timing and the process.”
Shown: A rendering of the finished house shows the two additions, both clad in horizontal siding, flanking the original house. The natural-cedar north end holds the new front entrance to the home.
Roger Stomps the Pavers
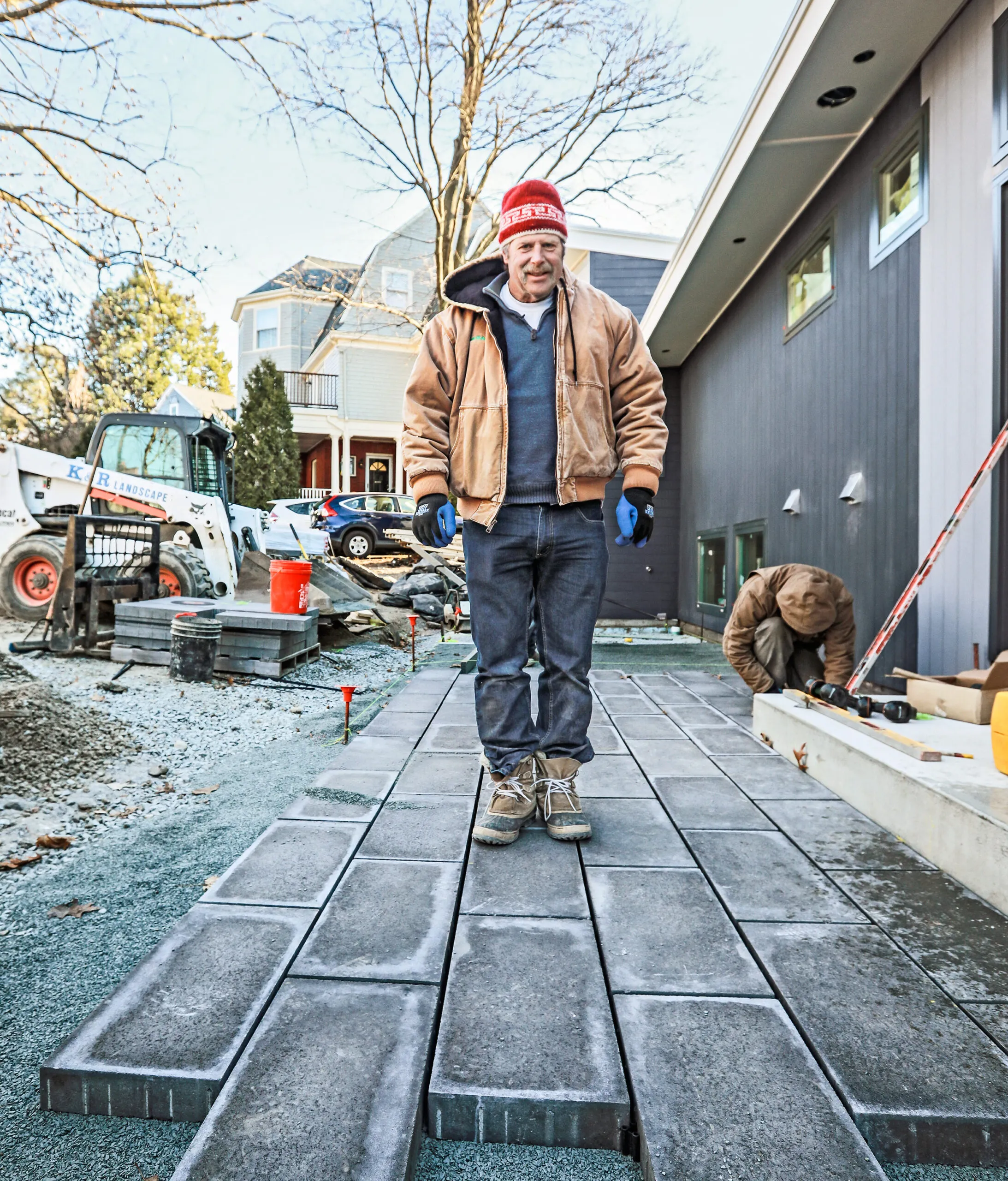
That modern simplicity is exactly what the homeowners are after. “We both grew up in Mumbai, where there are lots of concrete buildings and rarely a peaked roof,” says Sunil. “Even though we found this house almost by accident, we love that we have a modern house in the middle of Victorians.”
Shown: TOH landscape contractor Roger Cook gives the permeable patio paving outside the dining area a test stomp.
Pavers: Unilock
Angular Shapes
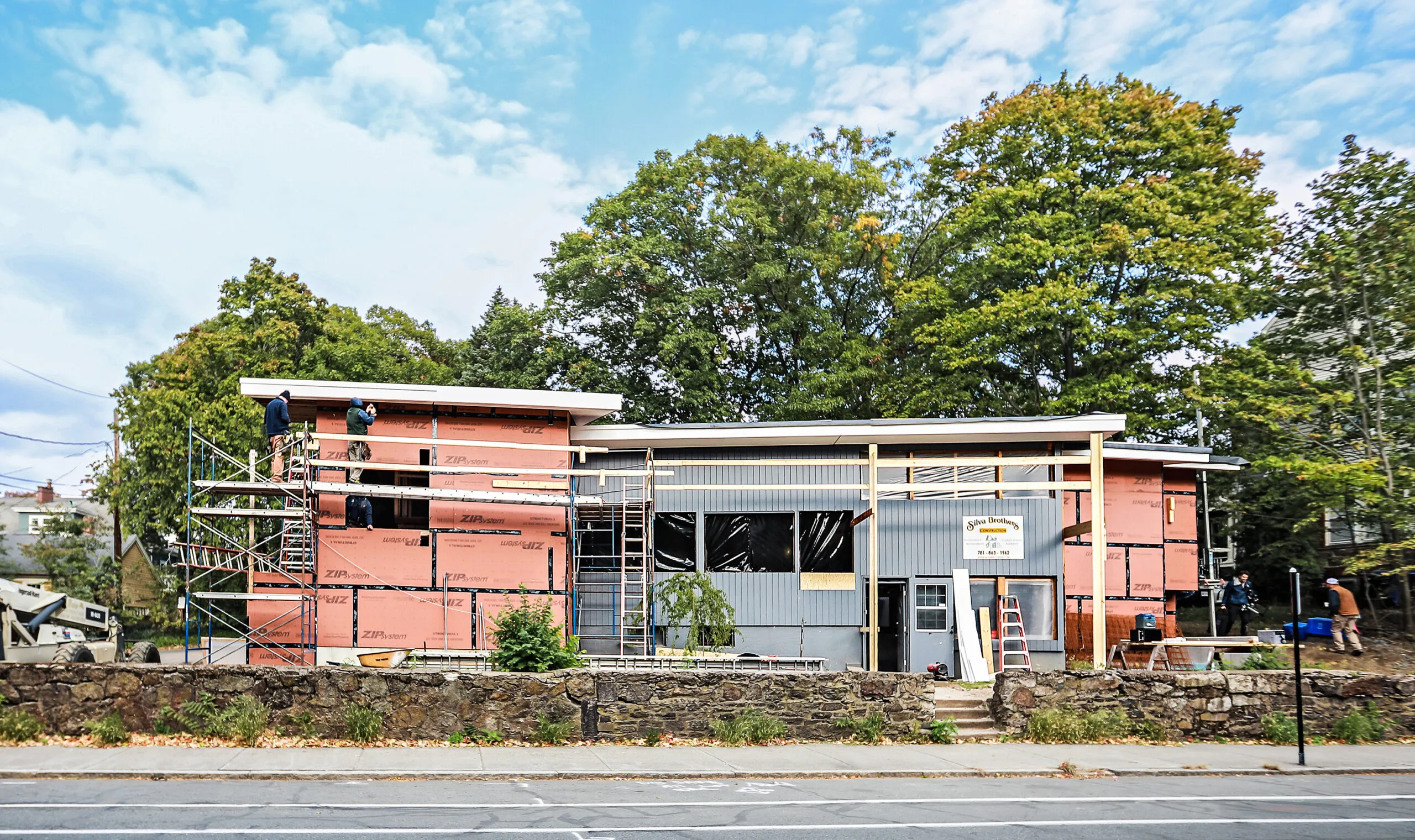
Hamlin sees some destiny at work as well. “This house is in Pill Hill, which got its name because doctors moved into the area in the early 1900s, attracted by the proximity to Boston’s hospitals,” she says. “We now have medical professionals in three of the seven houses on the street—it’s interesting to see.”
Shown: Both additions repeat the house’s angular shape and shed roof; they are sheathed with engineered-wood panels faced with a factory-fused water and air barrier.
Sheathing: ZIP System
Windows: Marvin Windows and Doors
PVC fascia: AZEK
Privacy Hedge
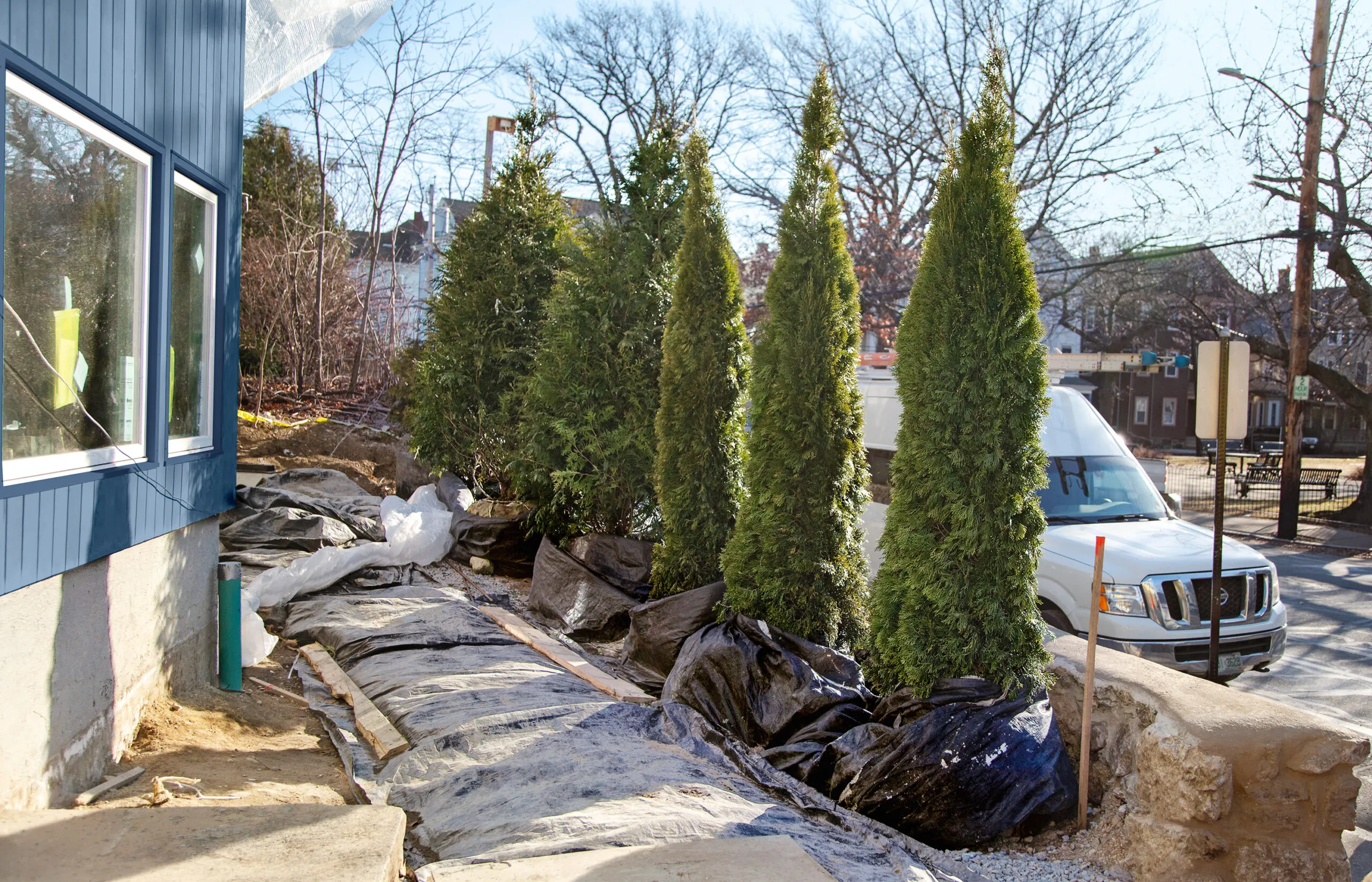
A freshly planted row of arborvitae creates some privacy between the house and a busy street.
Lumber Yardstick
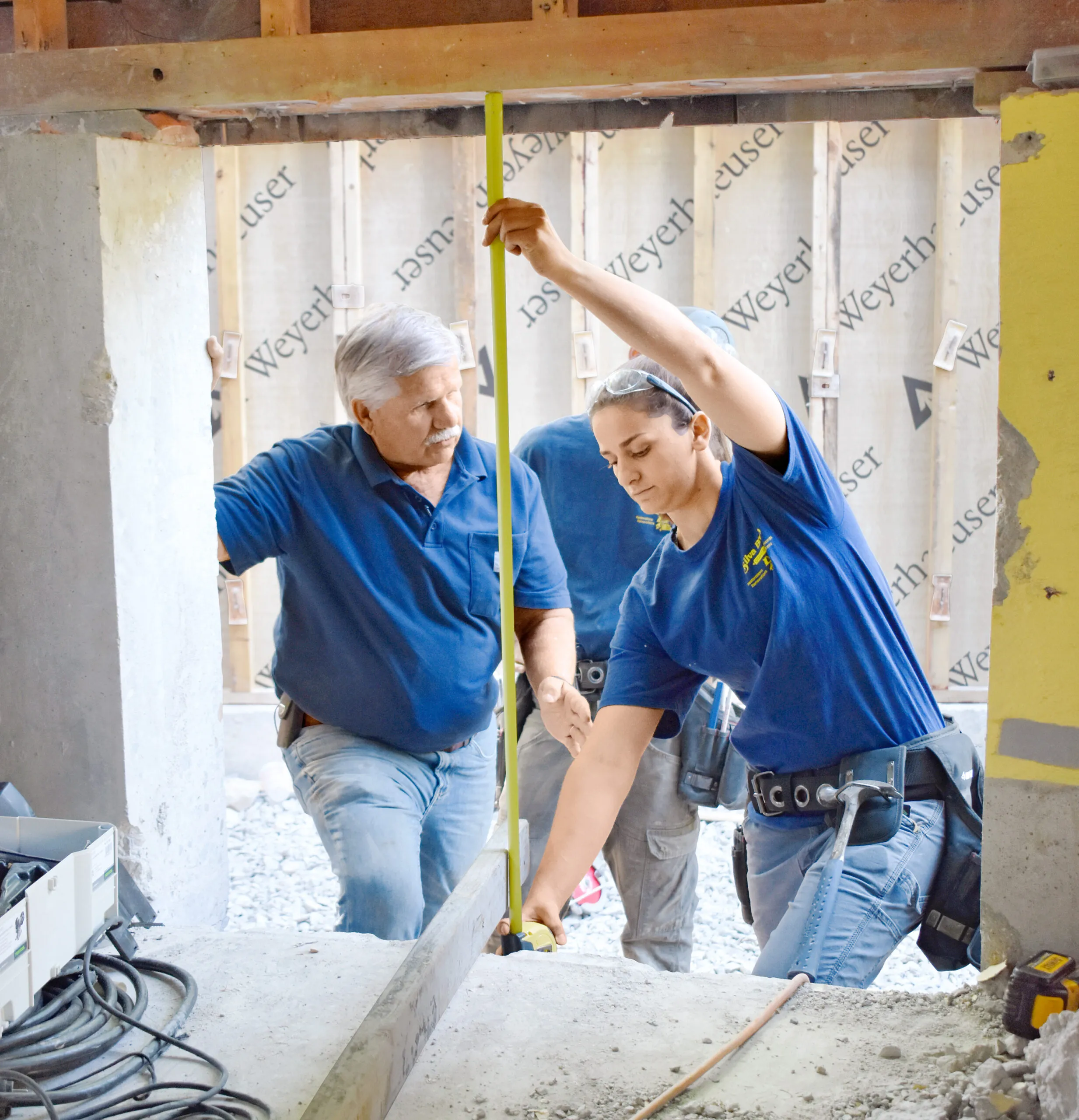
Tom Silva shows apprentice Carly Comitino how to use a piece of lumber to measure the floor and header heights where the south addition meets the existing basement.
Cutting Filler Boards
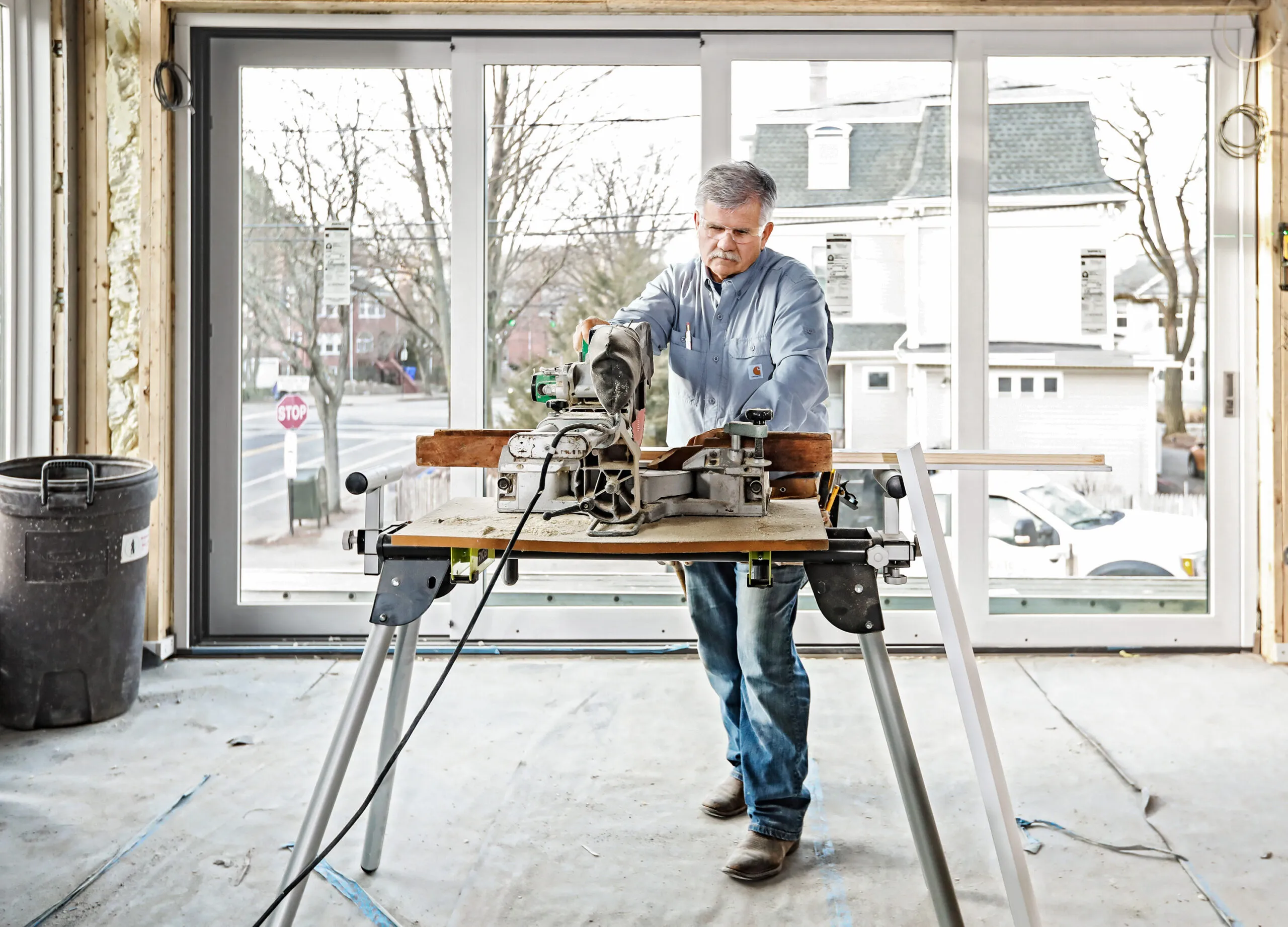
At a table saw set up in the living room near a 14-foot-wide set of glass doors, Tom Silva cuts filler boards to be used in making door and window jambs.
Patio doors: Marvin Windows and Doors
Tom’s Rabbet
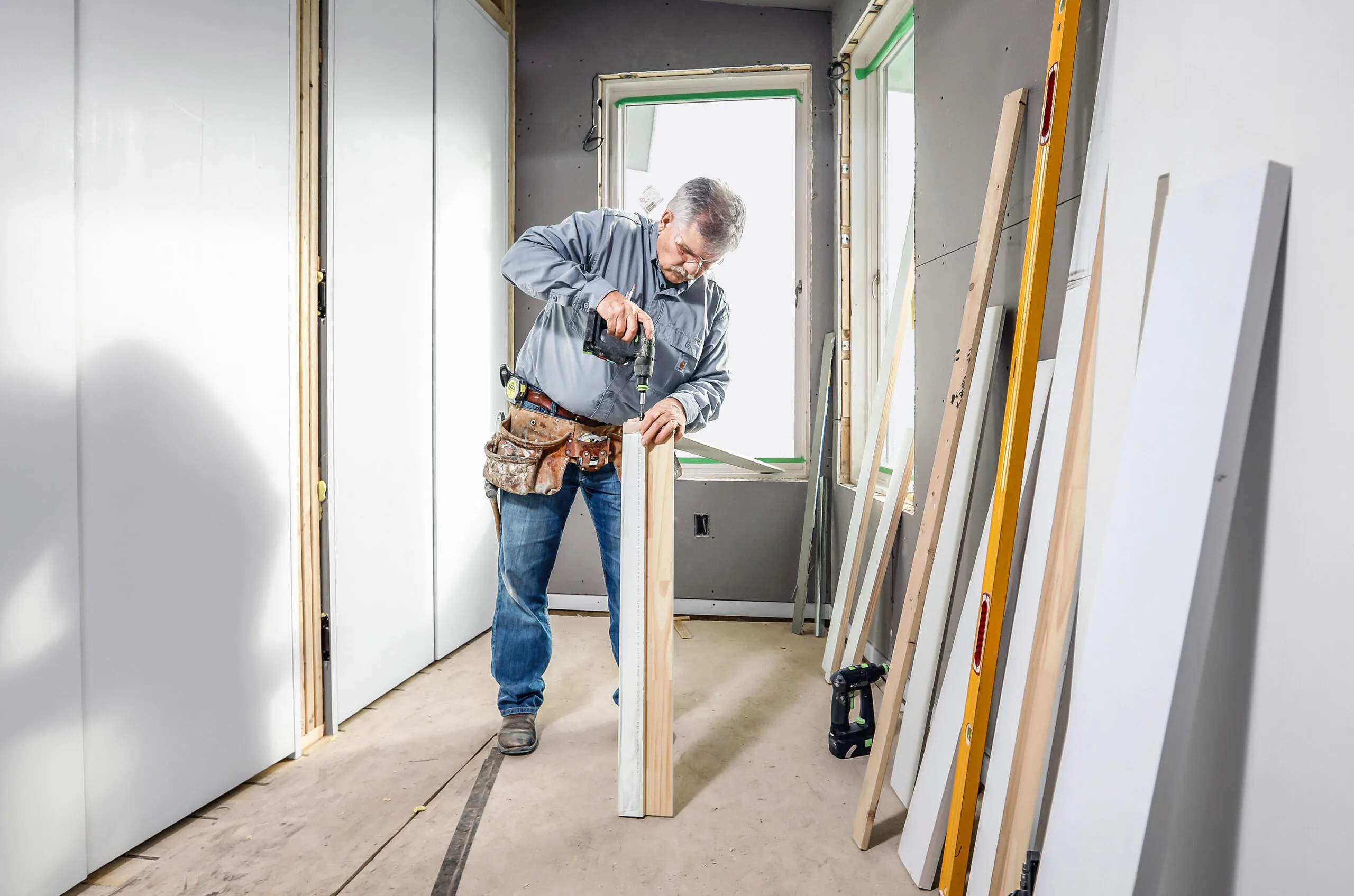
Tom Silva makes a rabbeted extension jamb for the bedroom windows to create a finished window trim that matches the streamlined mid-century modern aesthetic.
Insulation Panels
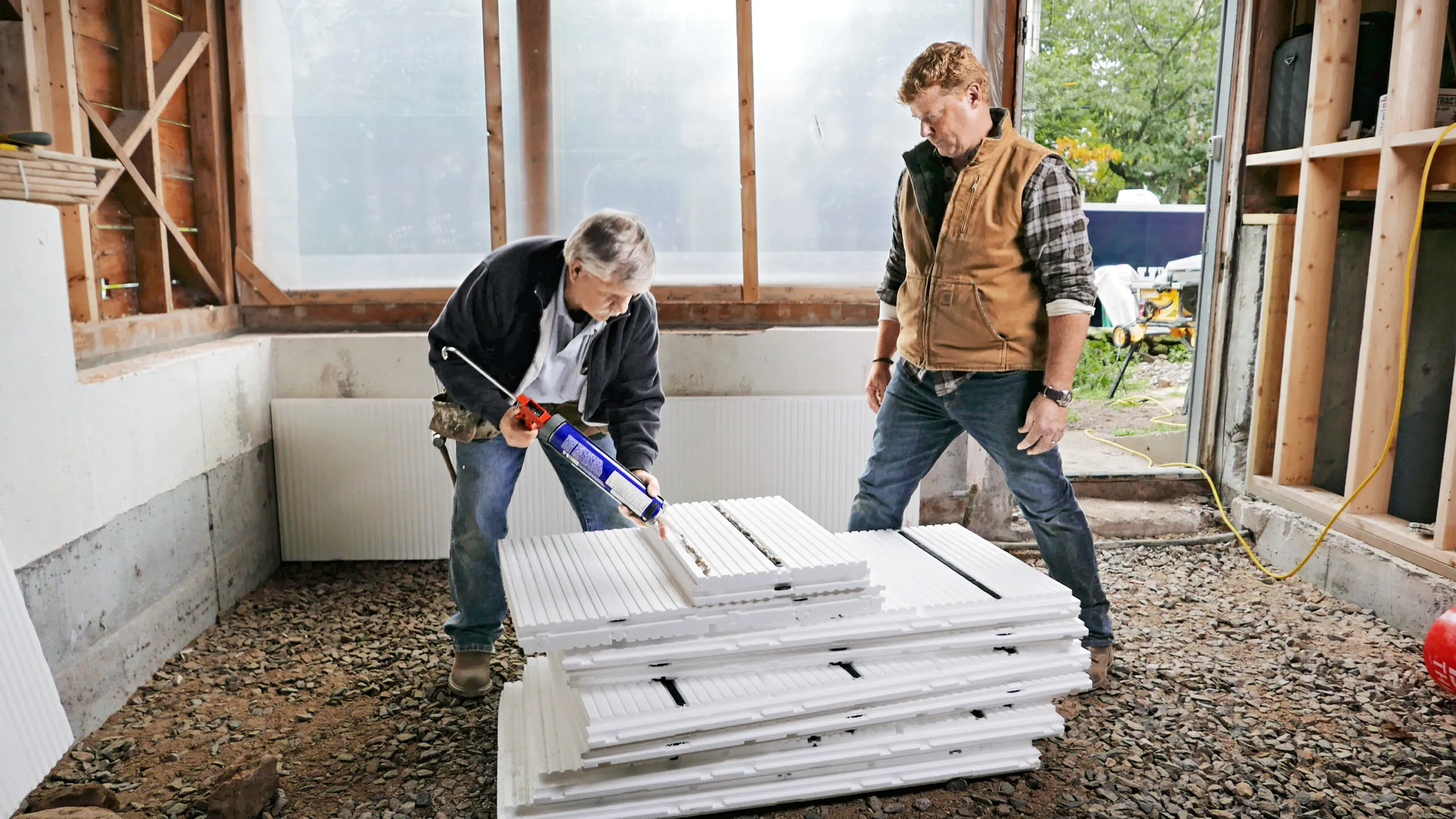
Tom Silva applies a bead of adhesive to drywall-ready foam insulation panels before he and Kevin O’Connor put the panels on the concrete foundation walls.
Continuous insulation panels: InSoFast
Radiant Floor Prep
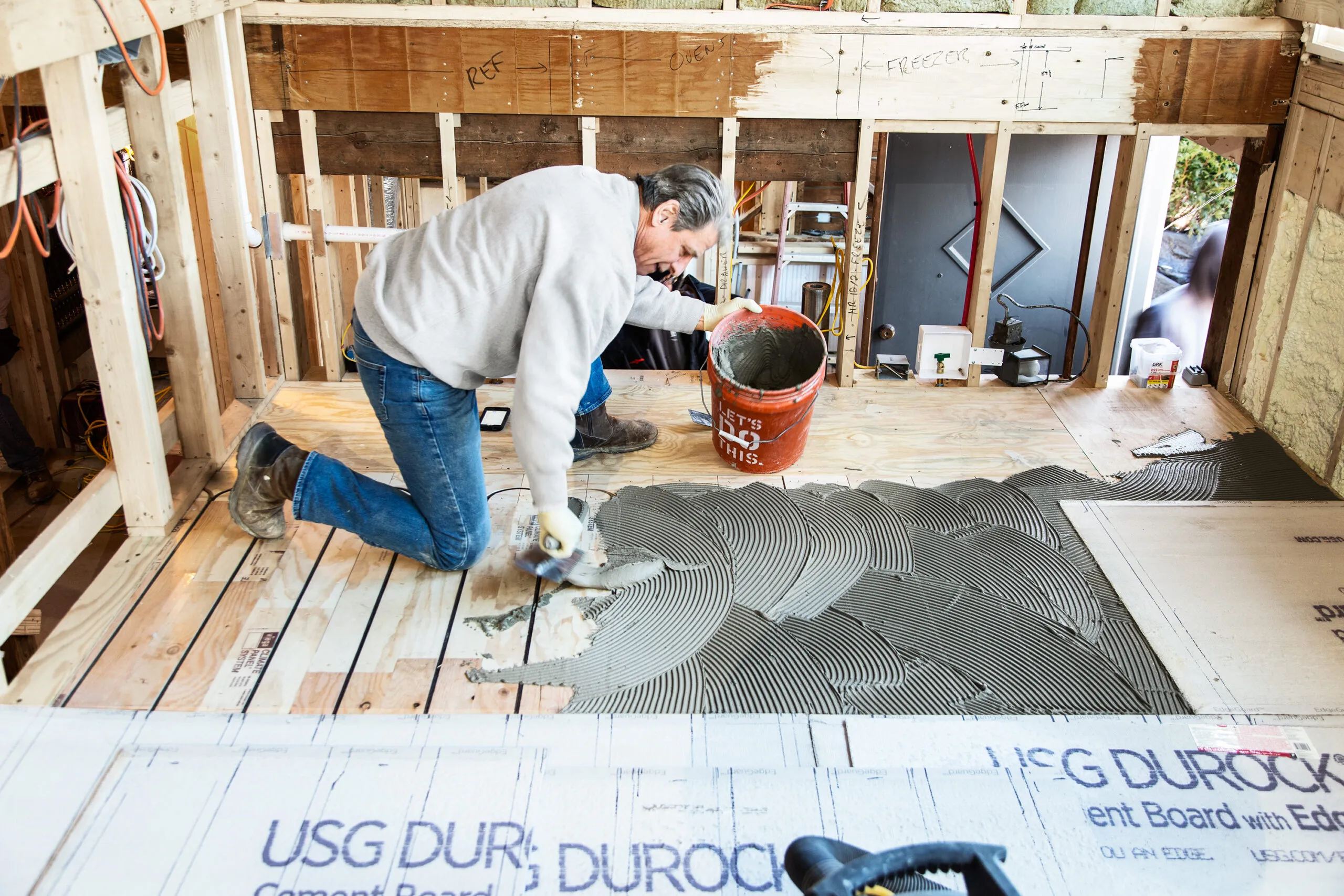
Tile contractor Mark Ferrante spreads mortar over the kitchen’s radiant-floor tubing before installing a cement backer-board underlayment, which will then be finished with tile.
Floor tile underlayment: USG Durock
Backer-Board Underlayment
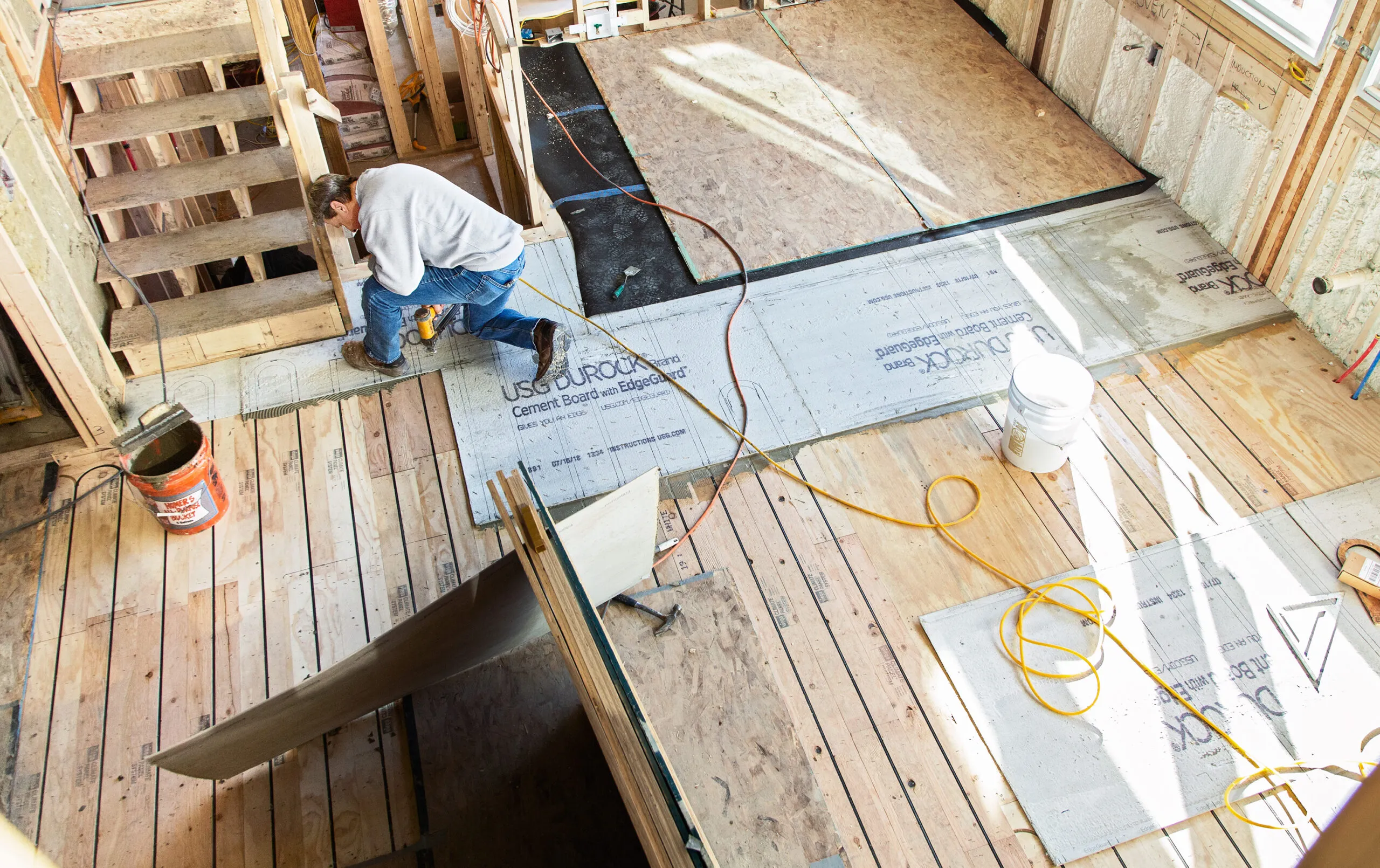
Tile contractor Mark Ferrante checks the cement backer-board underlayment in the kitchen area, which will eventually have a tile floor; the steps go up to the bedroom level.
Floor tile underlayment: USG Durock
Pipe Discussion
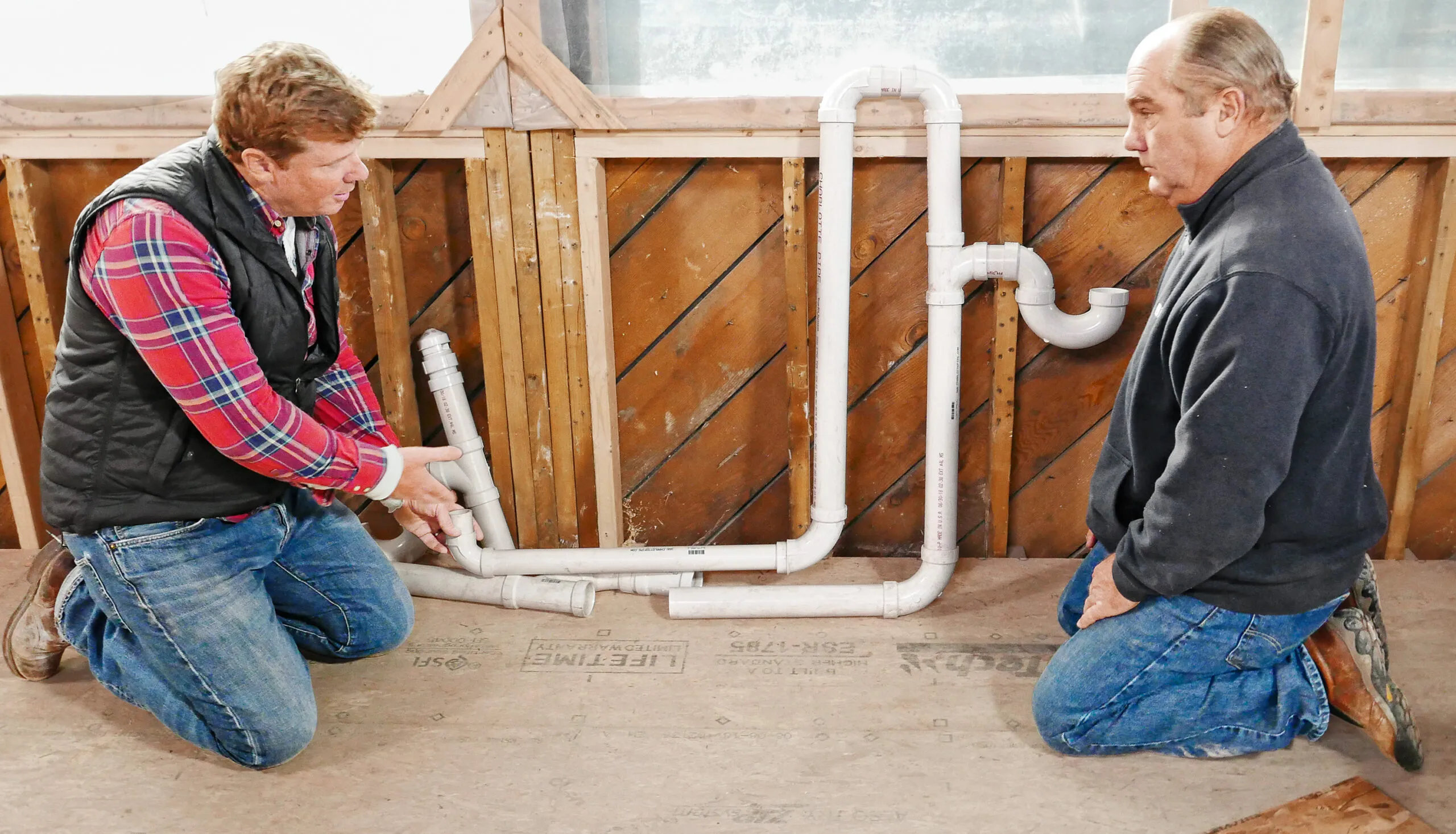
Kneeling in the kitchen area, Kevin O’Connor and Richard Trethewey discuss the proper piping method for the sink, which will require a bow vent because the sink will be installed along a wall of windows.