Start with a Ranch
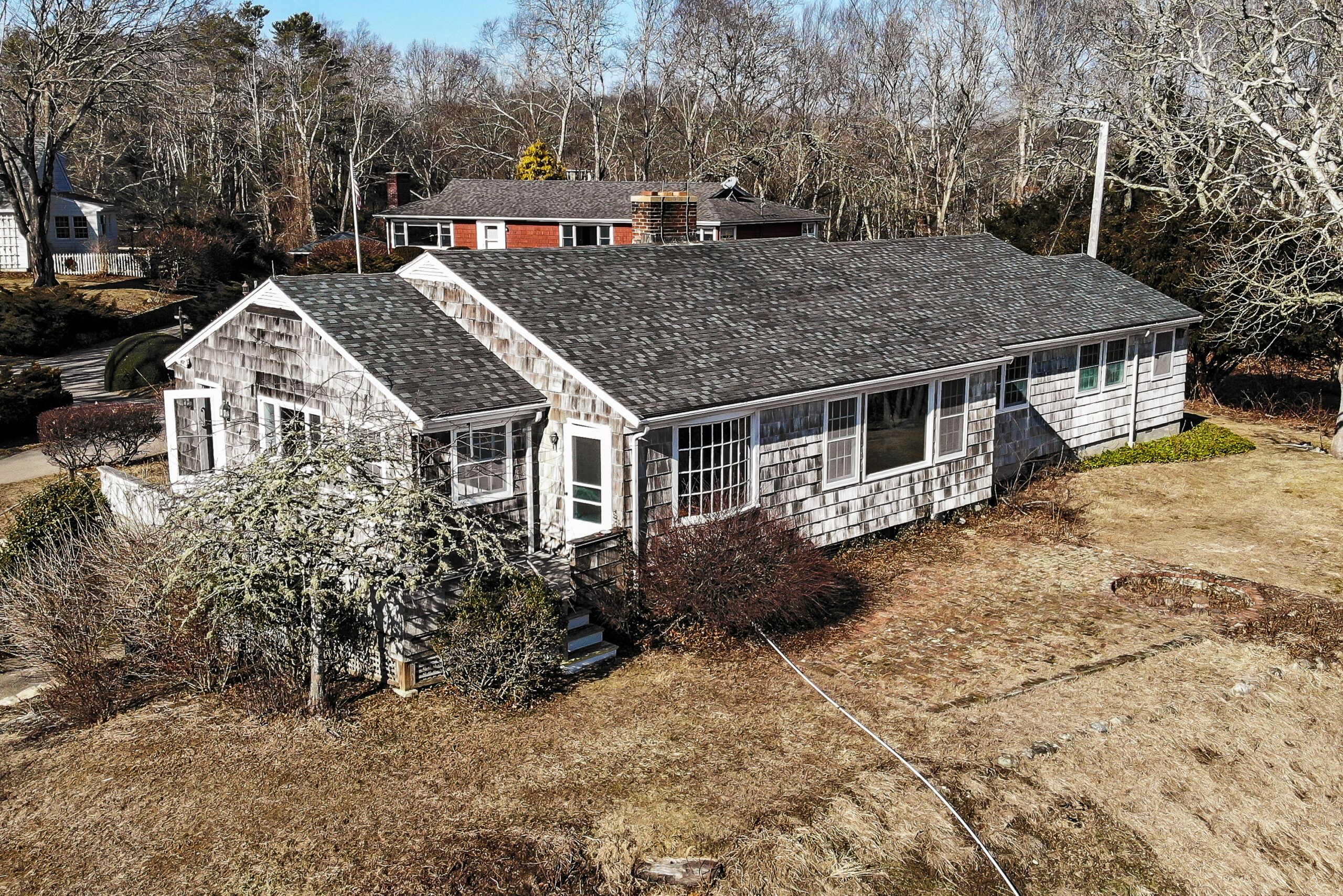
From the very first visit, Shayla Adams saw the possibilities for the one-story ranch house on a quiet cul-de-sac in Westerly, Rhode Island, in part because a majestic oak tree in the yard reminded her of her childhood home. Her husband, Scott, however, needed some convincing. He liked the lot—the 1.7-acre property was much larger than the fifth-of-an-acre that surrounded their home at the time. He also liked the location, just a mile from Misquamicut Beach, which he grew up visiting with family friends in Westerly. But he isn’t a fan of ranches. Scott is drawn to iconic shingled New England beach houses, and he had been watching TOH home builder Jeff Sweenor’s work along the Rhode Island coast for years. So Scott called Jeff for a walk-through and heard some magic words: structurally sound, ready for a second-floor addition, gambrel roof, shingled, classic New England. Sold!
Shown: Built in 1949, the ranch-style house was solid structurally, but offered only one floor of living space.
Into a Dutch Colonial
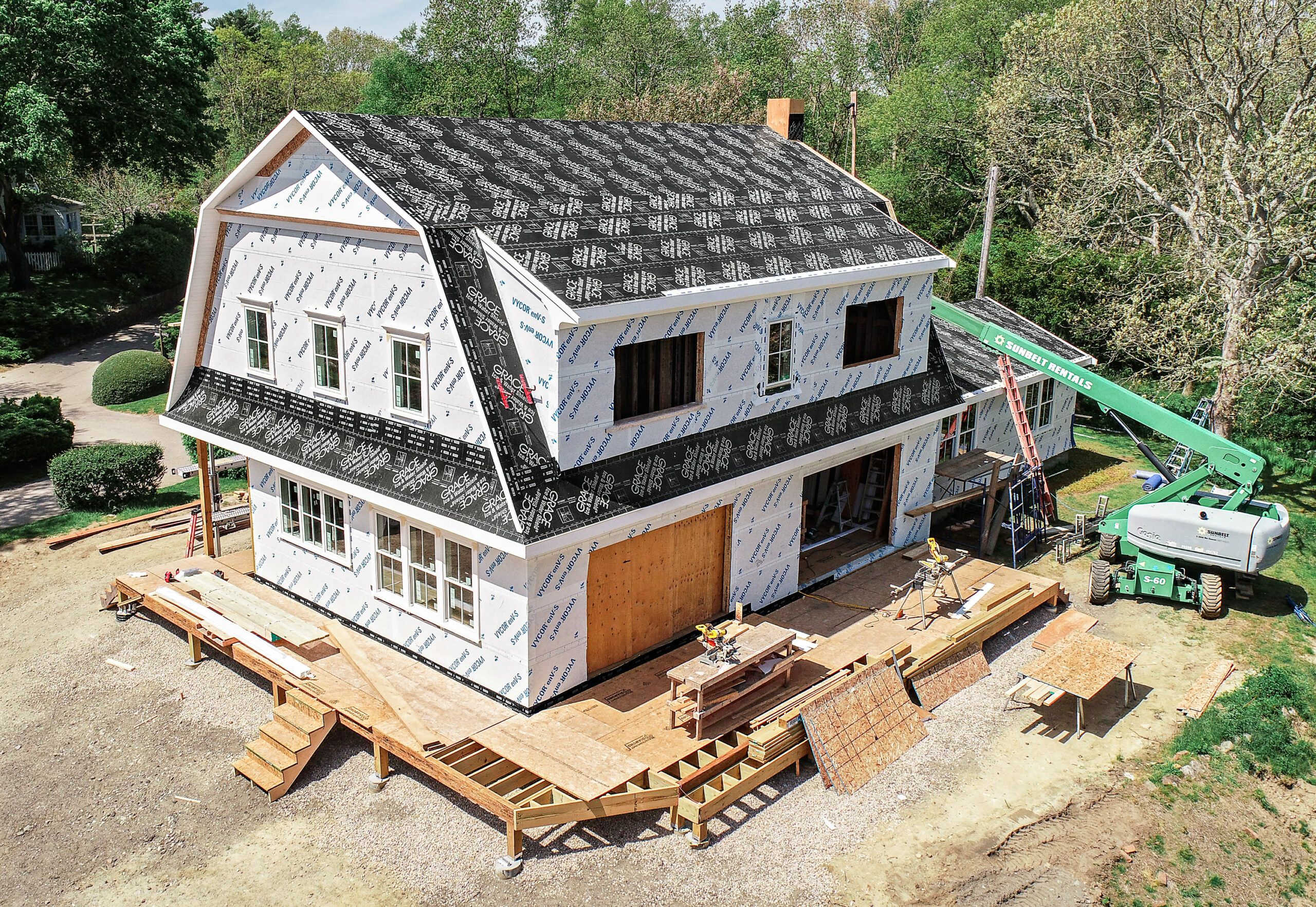
Jumping into the project with Sweenor’s design team, Scott and Shayla’s main priority was making more space for their family. With two daughters, Malin, now 6, and Emily, 2, the family had outgrown their small, no-backyard house, also in Westerly, and were looking to the 1949 ranch as a canvas for their dream home. The 1,850-square-foot house’s solid structure was a plus, but the warren of rooms covered in floor-to-ceiling knotty pine had to go, as did the massive fireplace that divided the front portion of the house from the back.
Shown: A gambrel roof with large shed dormers gives the renovated house its distinctive new look, while allowing for three bedroooms and two baths on the new second story. The remodeled house stayed within the existing footprint; adding a wraparound deck provides an indoor-outdoor connection the home previously lacked.
UNDERLAYMENT: GCP Applied Technologies
RAIN SCREEN: Mortairvent
BATT INSULATION: Rockwell
SPRAY-FOAM INSULATION: Gaco Western
INSULATION INSTALL: Ecologic Insulation
An Assist from Tom Silva
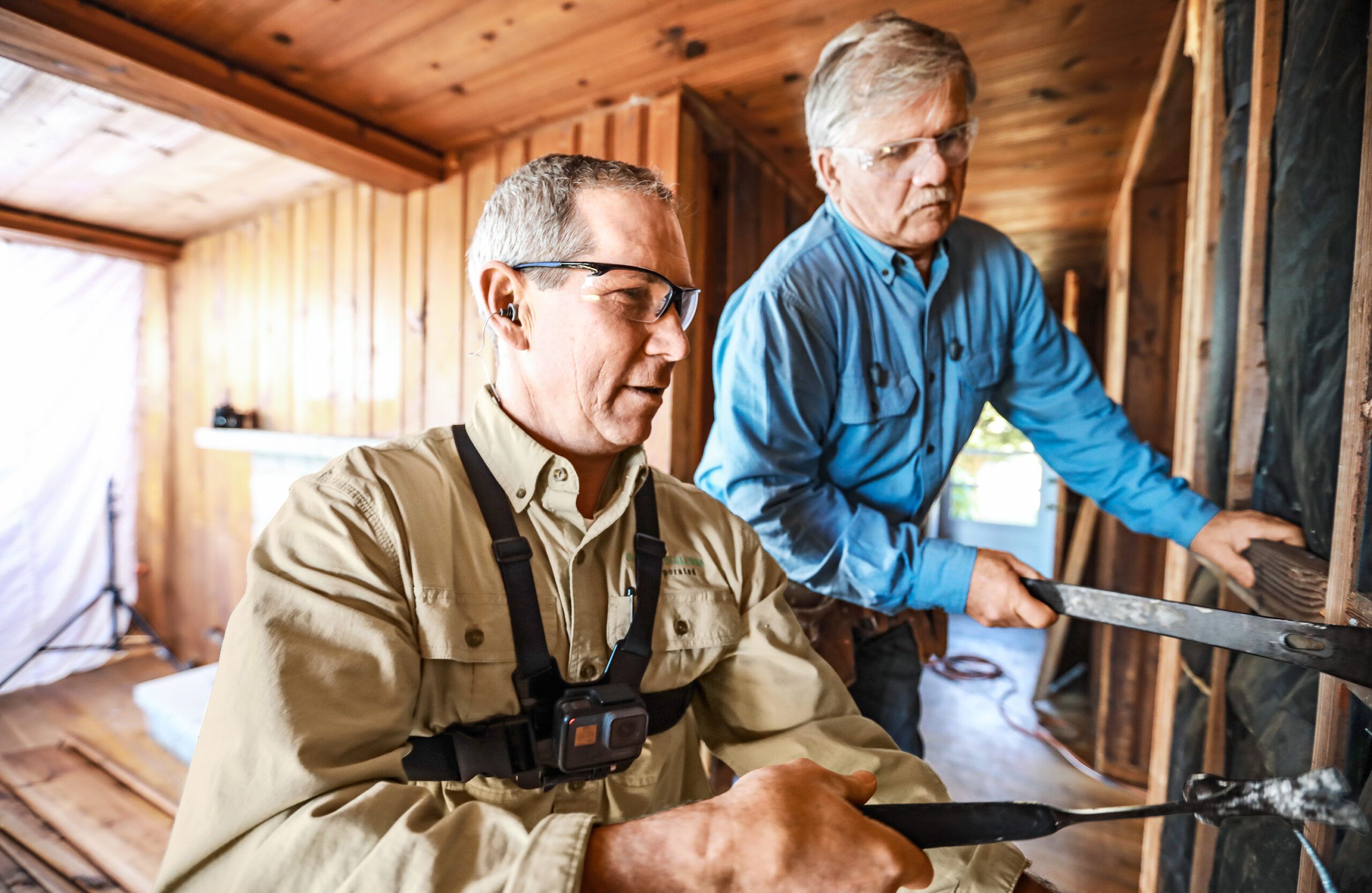
“We wanted an open-plan, light-filled main floor,” says Shayla. Adding a second story was key to making room for a master suite plus two bedrooms and a shared bath for the girls—with views of the ocean—and would enable the first floor to become the spacious, free-flowing living-kitchen-dining area they envisioned, while fitting in a mudroom entry, home office, and laundry. They decided to leave a 1970s bedroom addition at the north end of the existing house as a one-story structure that, combined with part of an existing bedroom, could be repurposed as a playroom/guest room. The plan also called for a wraparound deck downstairs, looking out over the yard—and Shayla’s tree. Scott wanted all that, plus more. “Swoops were a must!” he says, referencing the flared lines of the houses he admired.
Shown: TOH home builder Jeff Sweenor gets an assist from TOH general contractor Tom Silva as they carefully remove knotty pine from the walls for reuse in a new playroom/guest room in the renovated house.
GENERAL CONTRACTOR: Sweenor Builders
Landscape Options
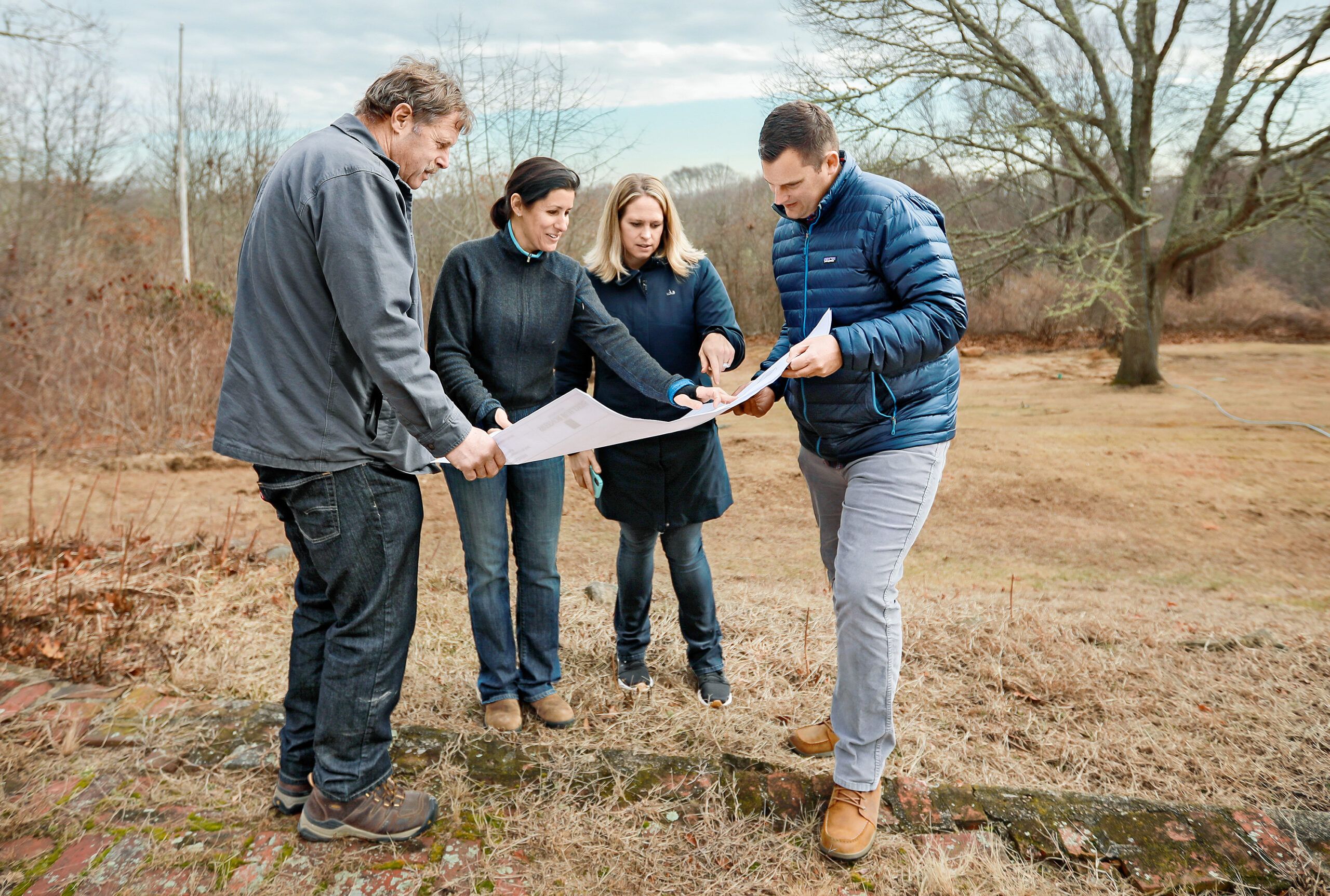
Adding the gambrel roof with large shed dormers would create the needed ceiling height for the rooms on the second floor, says Sweenor Builders architectural designer Lori Foley. But this is no basic suburban Dutch Colonial. Large soffit overhangs, gable build-out details, and those wall “swoops” suggest the gracious shingled homes that dot the region’s coastline—and those curves have become something of a Sweenor Builders signature.
Shown: Homeowners Shayla and Scott Adams discuss landscaping options for their nearly two-acre property with TOH landscape contractor Roger Cook and TOH landscape designer Jenn Nawada.
ARCHITECTURAL DESIGNER: Lori Foley
Raising a Gambrel
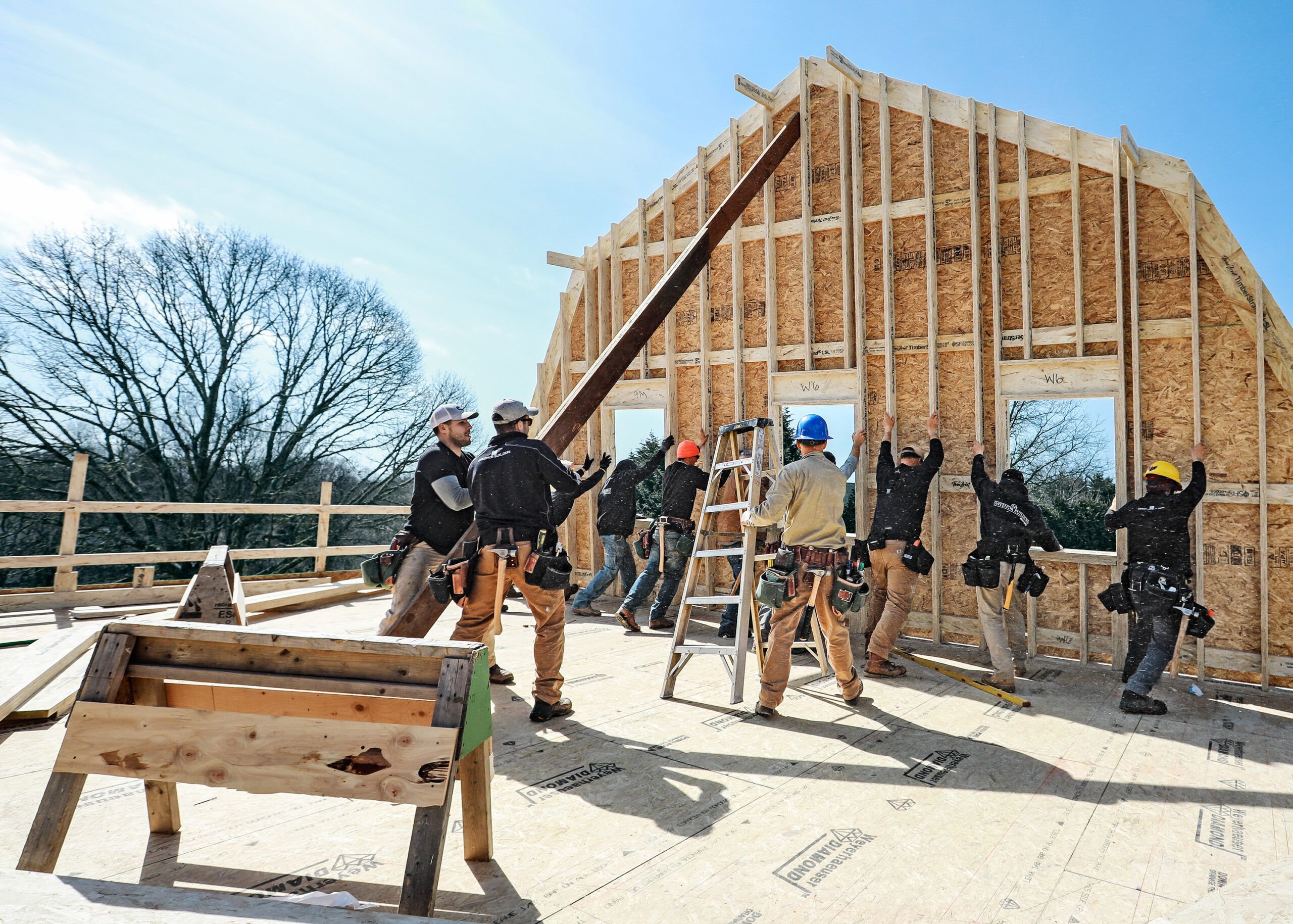
Jeff knew he had a good starting point: The house was solidly built, with 1×6 diagonal floor planking as underlayment and old-growth Douglas fir framing, and it had been left relatively untouched. So his first order of business wasn’t correcting structural or foundation work but dealing with demolition of the interior walls, knotty pine paneling, fireplace, and chimney.
Shown: The crew raises the south-facing gambrel end; it was built on the floor deck using sheets of OSB (oriented strand board) and LSL (laminate strand lumber) studs.
FRAMING MATERIALS: Weyerhauser
Marks for Roofing
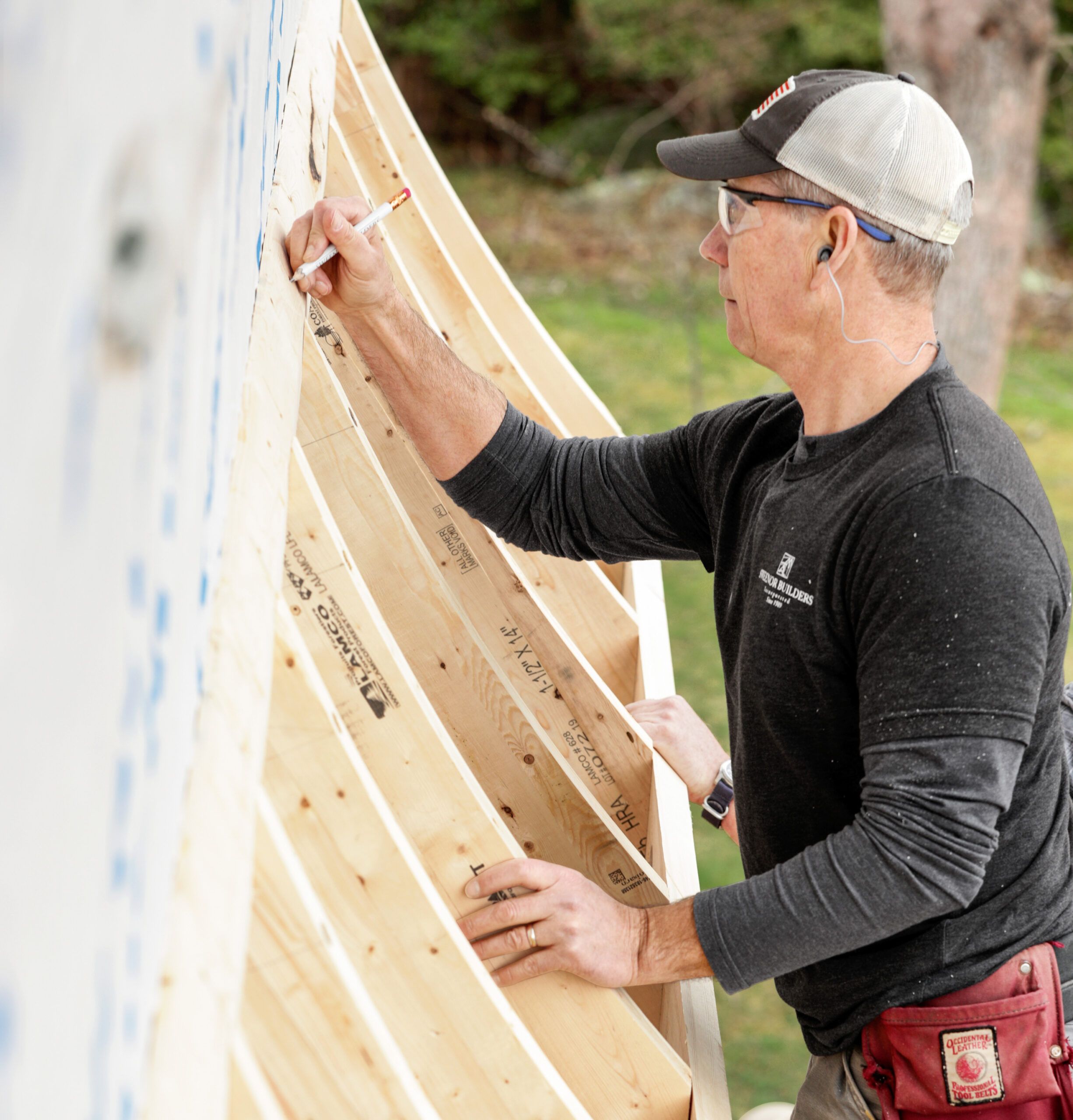
“True to the period, the house was filled with knotty pine, which had darkened over the years but was nicely done, and we knew we could reuse it,” says Jeff. Some of it will be used in the new playroom, the rest donated to Habitat for Humanity. The crew also carefully salvaged the hand-nailed oak strip flooring for the daughters’ bedrooms.
Shown: With the rafter tails in place, Jeff Sweenor marks the location of the roof sheathing.
RAFTER TAILS: Lamco
GenerationNEXT Apprentices
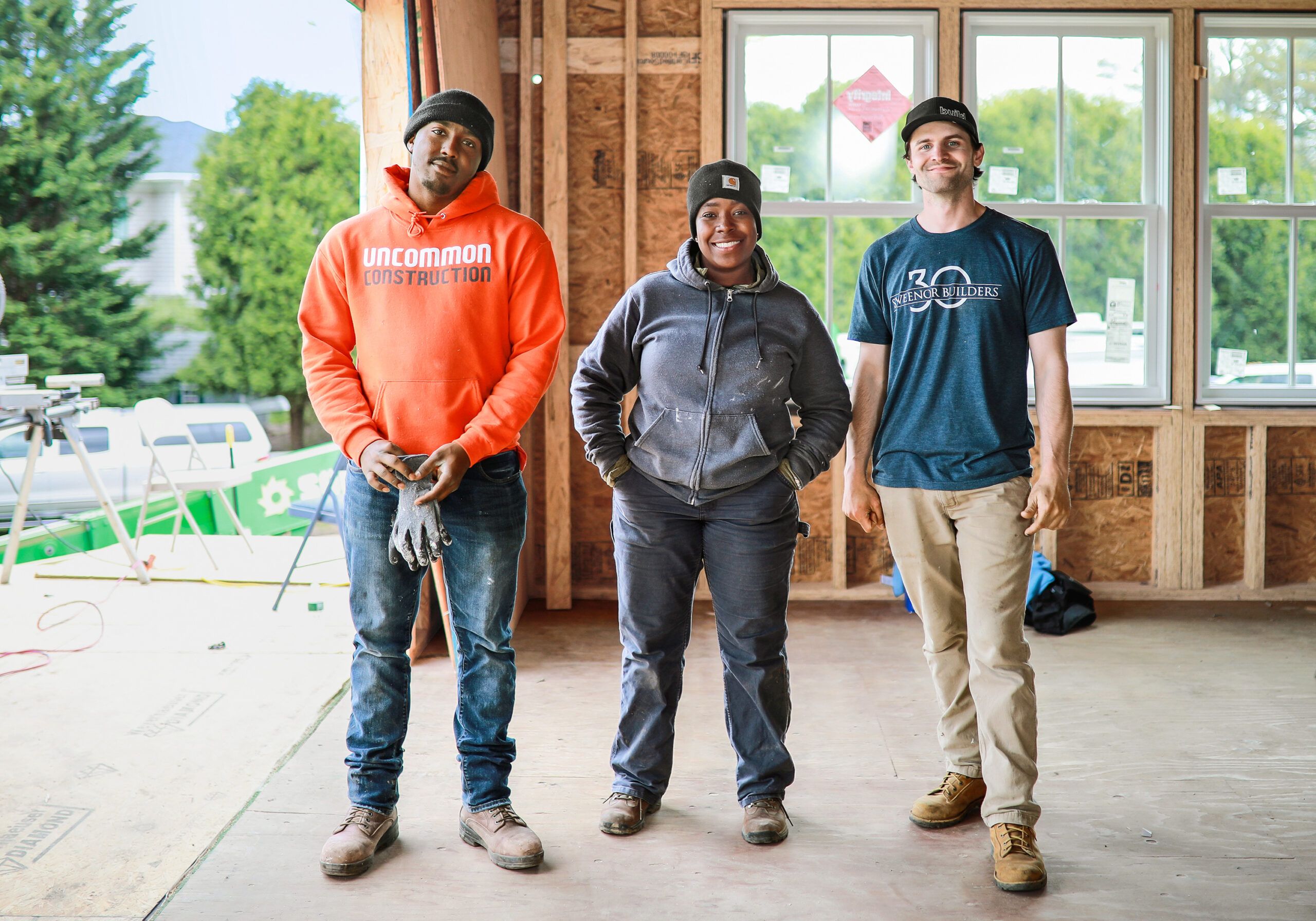
The two-sided fireplace, which divided the original entry from the living room, and its massive brick chimney, however, simply had to come out. Jeff tackled it with TOH mason Mark McCullough at his side. “It was so well built, it took a lot to get it down,” Jeff says.
Shown: This Old House GenerationNEXT apprentices De’Shaun Burnett and Kathryn Fulton (left and center) team up with Sweenor Builders crew member Ryan Dolan at the Westerly project.
Installing Windows
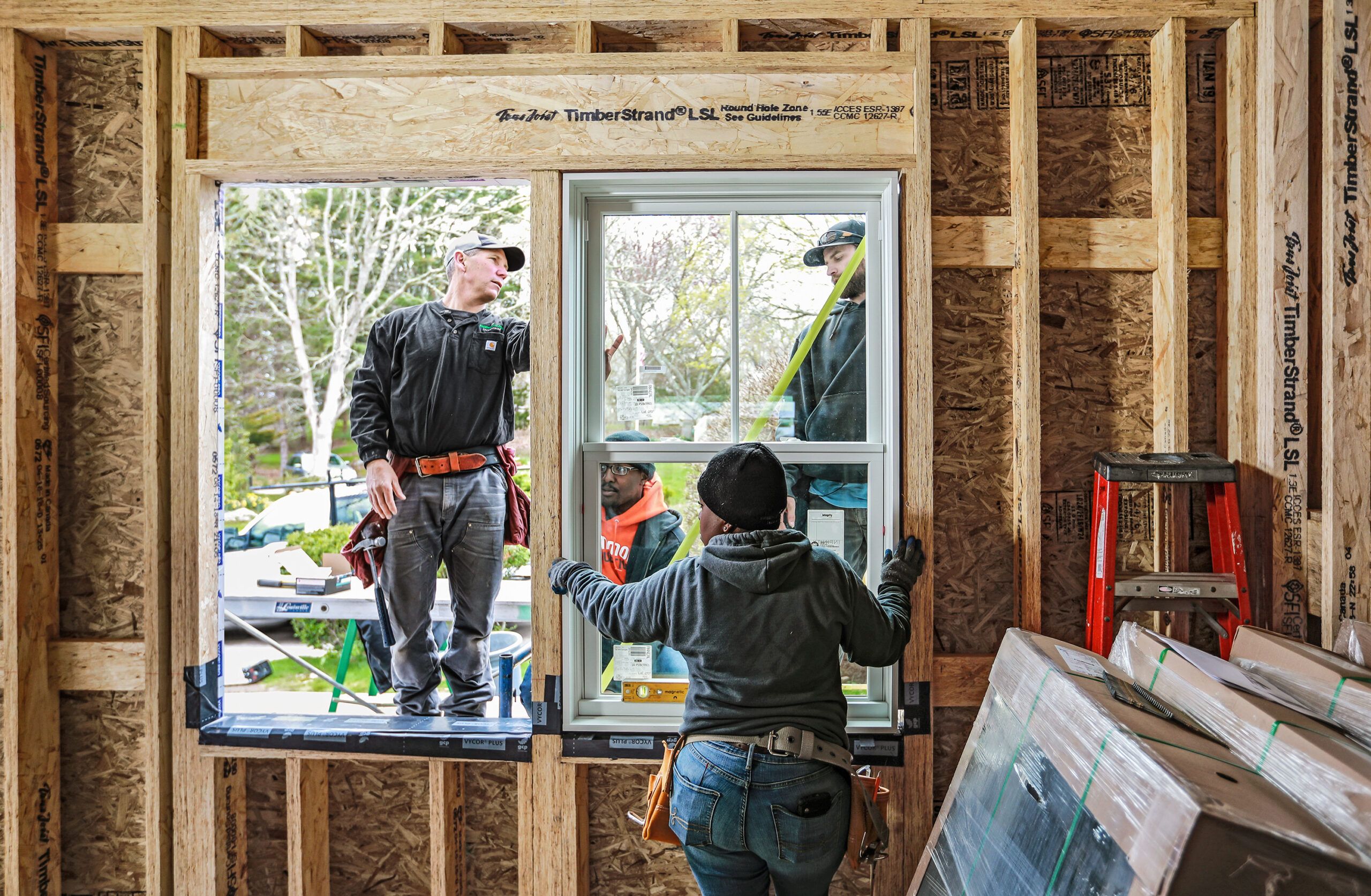
The exterior walls of the original house also needed to come down to create the 9-foot-high ceilings, open layout, and new window and patio door placements that were on the design plan. “You can’t just add one foot to the eight-foot-high original exterior walls, because that would create a hinge effect,” explains TOH general contractor Tom Silva. To support the weight of the second floor, and accommodate the open layout, Jeff decided to rebuild entirely with engineered lumber, which is extremely strong, straight—and heavy. As a first step, his crew used industrial-size jacks to crank a 40-foot-long, 1,500-pound parallel-strand-lumber engineered beam up 10 feet in the air, and muscled it into place to span the renovated downstairs area.
Shown: Jeff and Dolan give the TOH apprentices a lesson in installing windows; these open up the new kitchen to the yard.
WINDOWS: Marvin
Coffered Ceiling Install
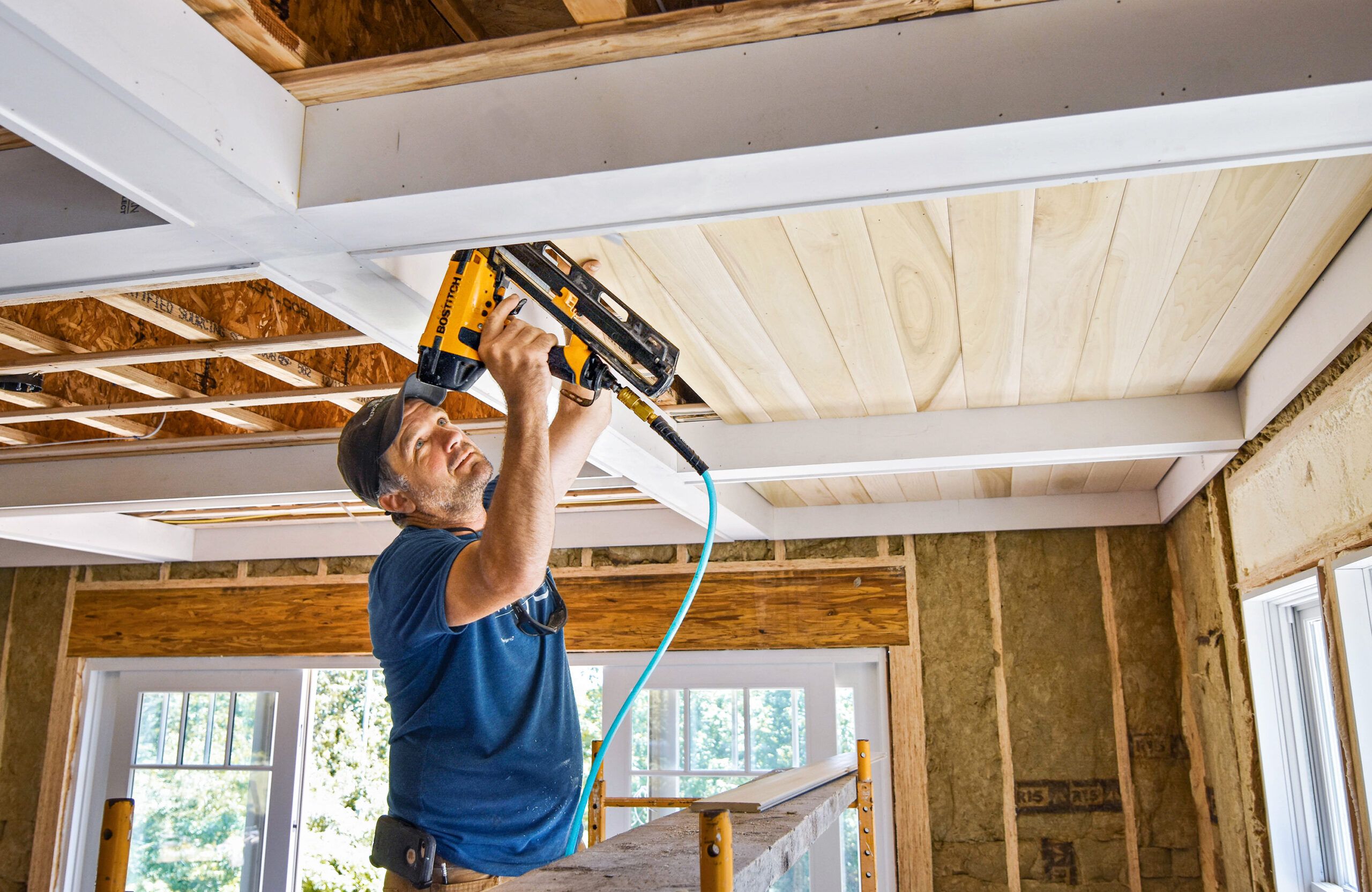
The iconic gambrel roof that the homeowners wanted led to another barn-raising-type day on the project. “We built the end walls and roof profile as one piece, and pulling all that into position required a lot of manpower,” says Jeff, whose help on the Westerly project includes three TOH GenerationNEXT apprentices.
Shown: Sweenor Builders project foreman Garrett Kirwin installs the living area’s coffered ceiling. With the grid in place, each section is finished with 16 tongue-and-groove poplar V-board that will be framed with crown molding.
COFFERED CEILING INTERIOR TRIM: Baird Brothers
Chimney Upgrade
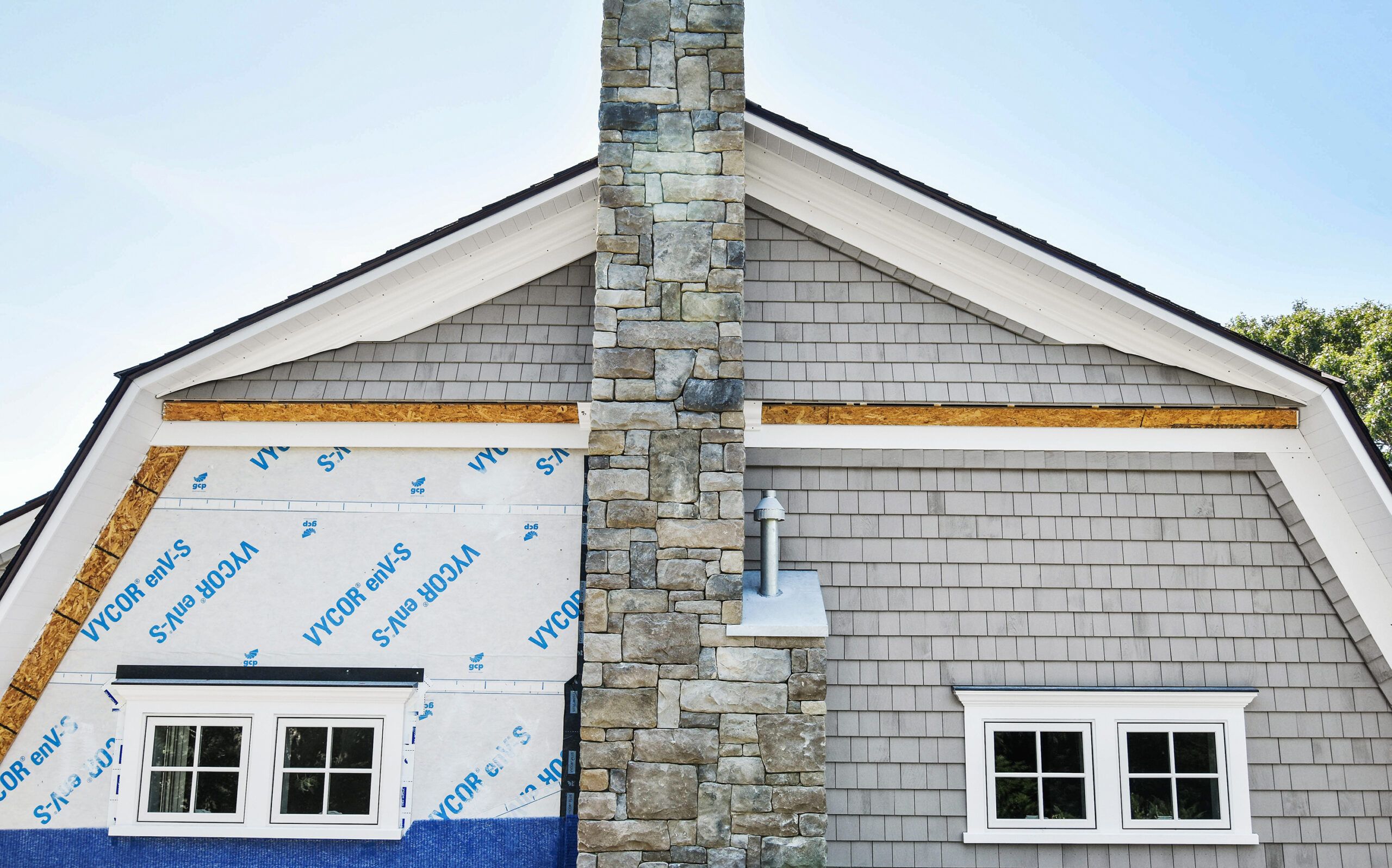
For TOH plumbing and heating expert Richard Trethewey, the renovation early on was all about installing interesting systems. A 1,000-gallon liquefied petroleum gas (LPG) tank was installed in a large underground trench, anchored to the earth to prevent any chance of the tank moving if the water table rises; the LPG will provide gas for the kitchen stove and the house’s heating. The original cesspool was replaced by a 1,500-gallon septic tank combined with an advanced secondary treatment system that converts nitrogen to gas, which is vented through the roof of the house. “Being this close to a pond and the ocean, we had to step up to a higher level of septic system,” says Richard.
Shown: Shingles go up around the new chimney, which also wraps the furnace flue. The manufactured stone veneer, which is lighter and easier to cut than natural stone, is mortared onto cement backer board.
ENGINEERED STONE VENEER: Eldorado
Gable Finishes
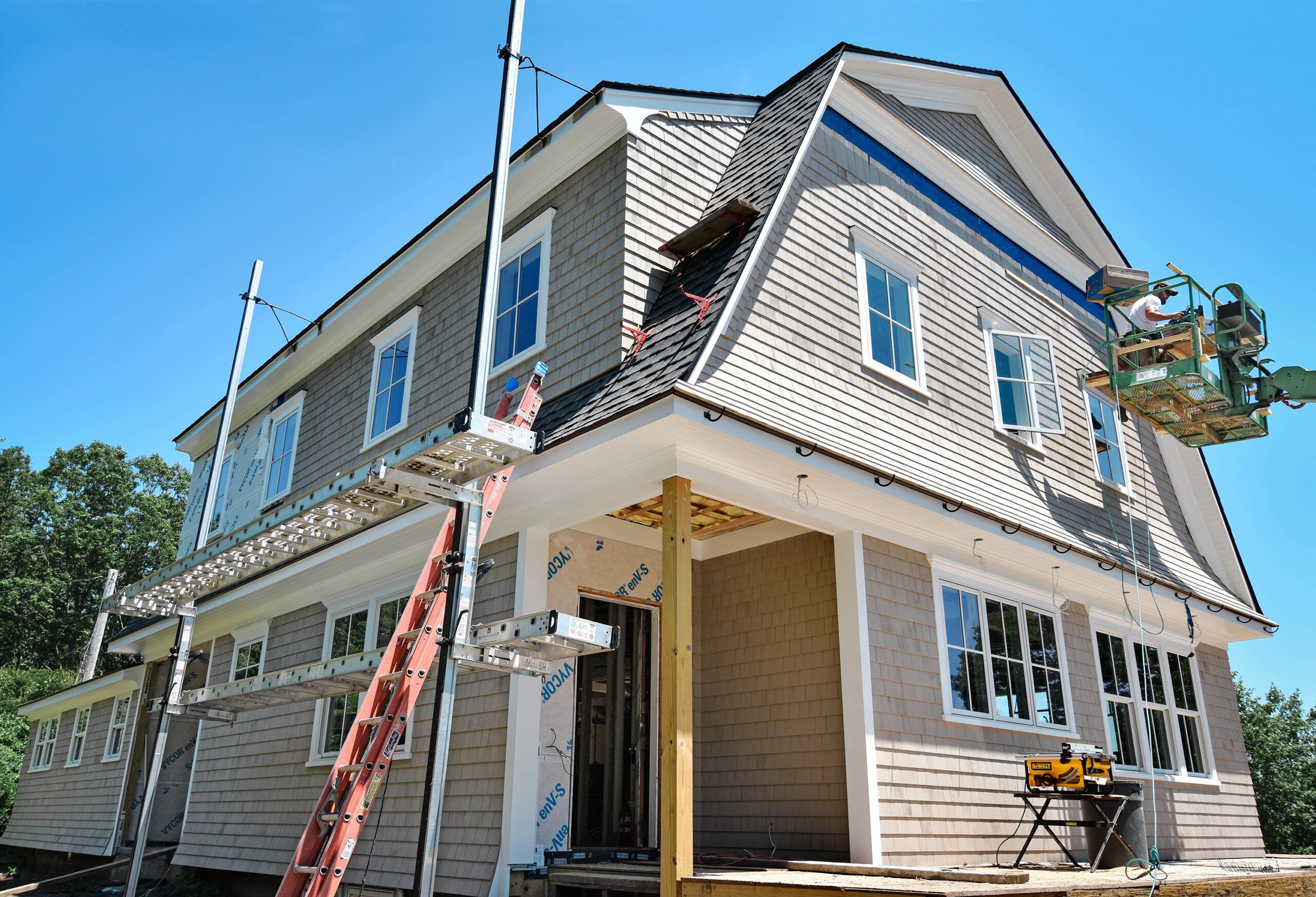
With work in full swing, the house’s architectural details began to emerge, including the coffered ceiling that will unify the living-dining-kitchen area downstairs. On the exterior, one very important detail got Jeff’s full attention: those swoops that Scott Adams was after. In a matter of hours, on a cold spring day, the crew framed them out using 150 machine-milled curved rafter tails around the base of the second-story addition. “That eave detail makes all the difference,” Jeff says—and is key to the kind of classic seaside New England home the Adamses are after.
Shown: A bucket hoists Sweenor Builders crew member Adam Spink up to the south gambrel gable, where he installs the prestained white cedar shingles.
SHINGLE SIDING: SBC Cedar
Finished Rendering
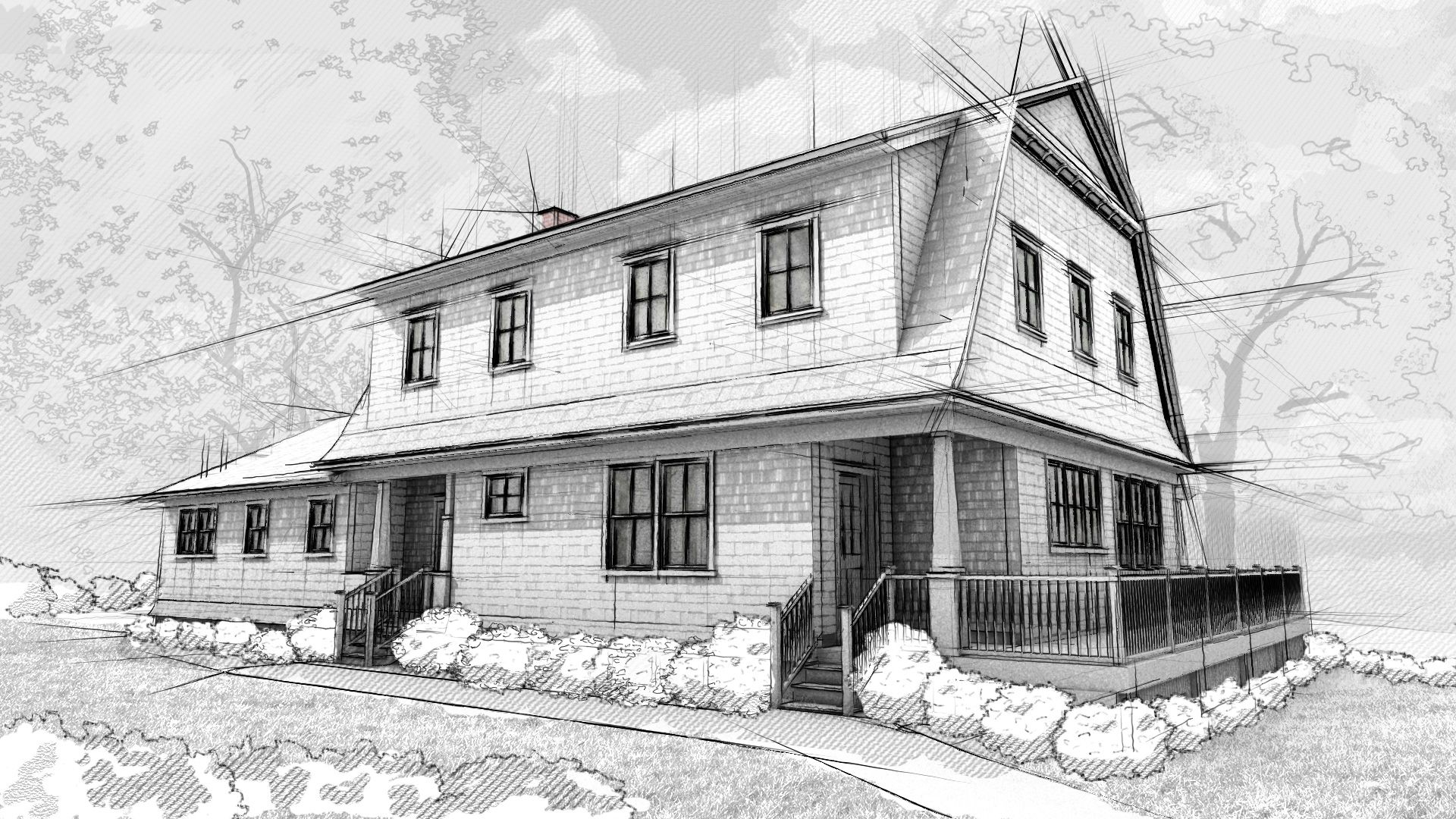
Shown: The finished house, as seen in this rendering, shows the everyday entry (on the right), which leads to a mudroom off the kitchen, and the formal front door (on the left).
Trim Work
Jeff Sweenor (on scaffold) installs trim where the coffered ceiling meets the shiplap fireplace wall, as Tom Silva and TOH host Kevin O’Connor look on.
INTERIOR TRIM: Baird Brothers
COFFERED CEILING: Baird Brothers
Flooring Install
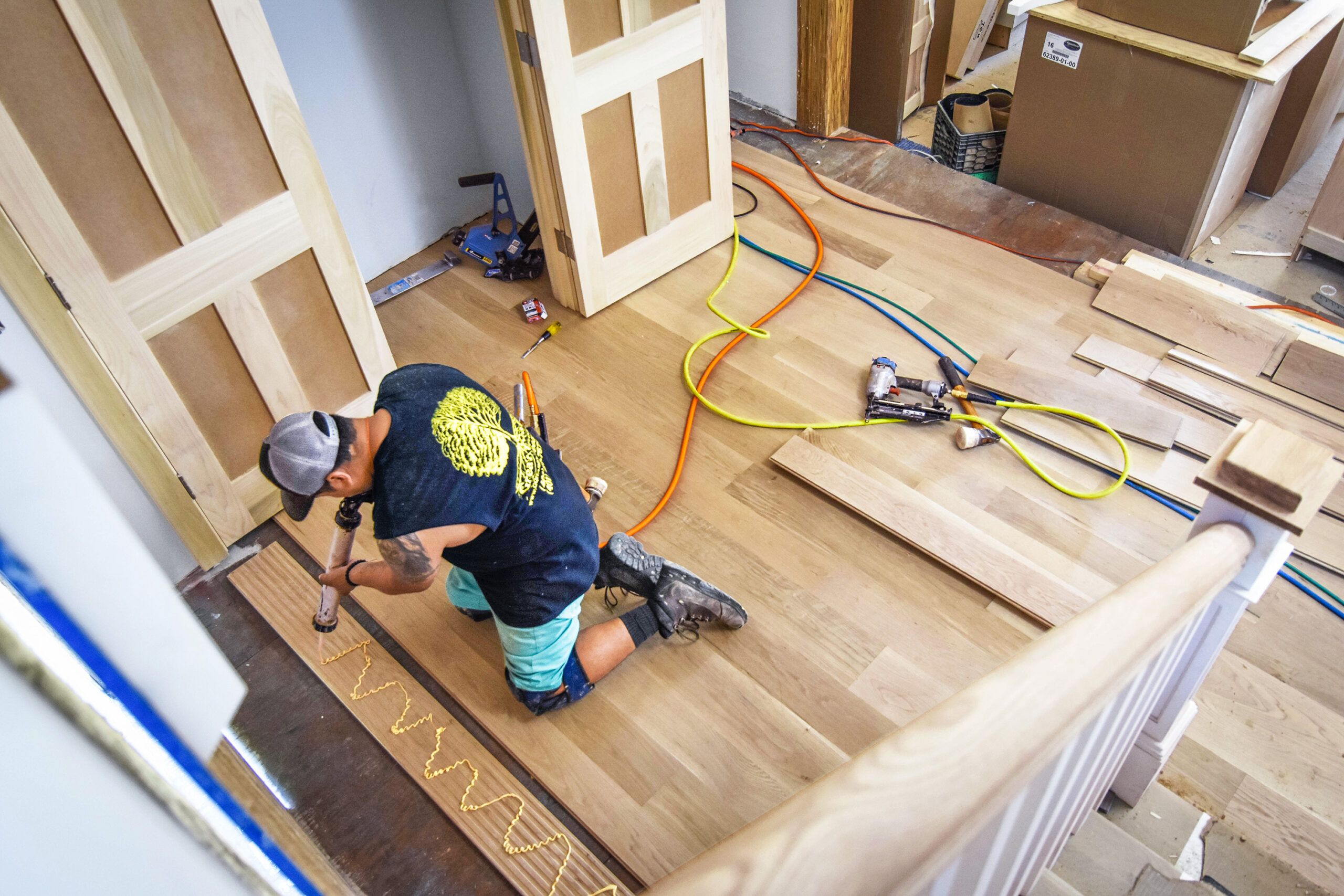
Jonathan Gramajo of GQ Hardwood Floors glues down random-width—5-, 6-, and 7-inch—white oak boards in the entry.
HARDWOOD FLOOR INSTALLATION: GQ Hardwood Floors
OAK FLOORING + INTERIOR DOORS: Baird Brothers
Window Trim
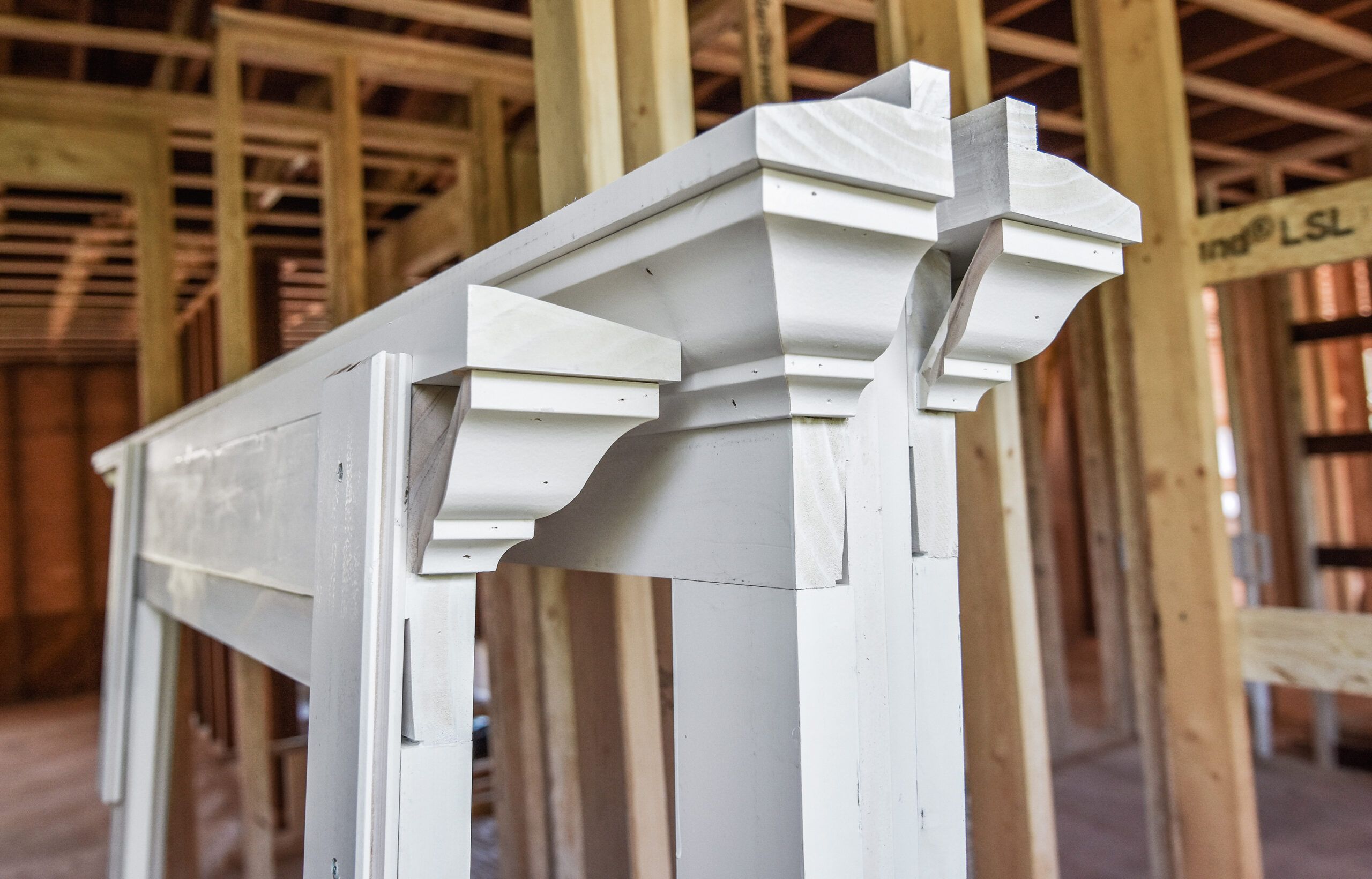
Exterior window trim was pieced together in advance of installation to create tight joints that can weather rain, wind, and cold.
RADIATA PINE EXTERIOR TRIM: Lifespan
Before Facade
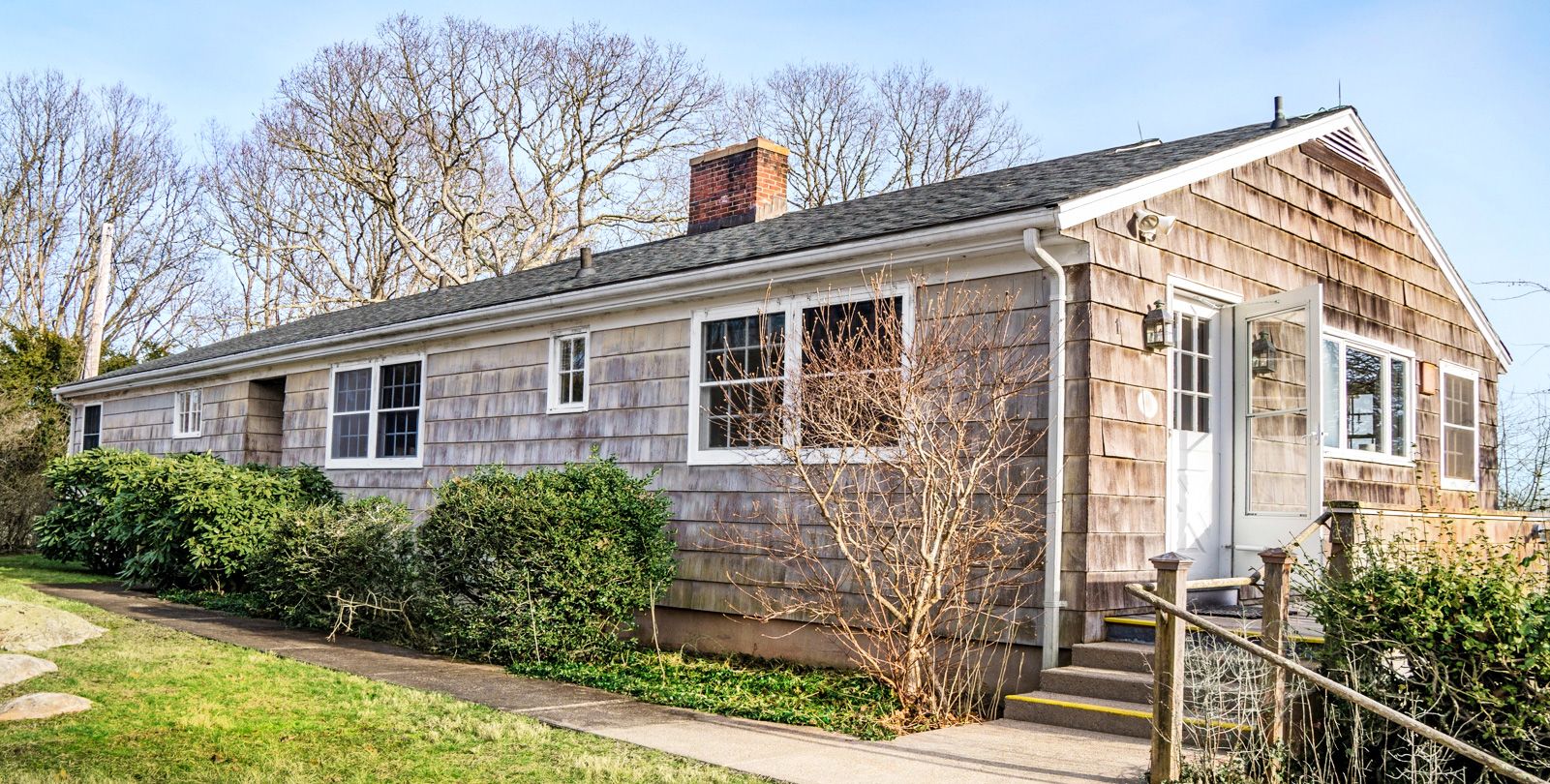
The front facade of the existing house had the everyday entry on the gable end.
Shingling the South Gambrel
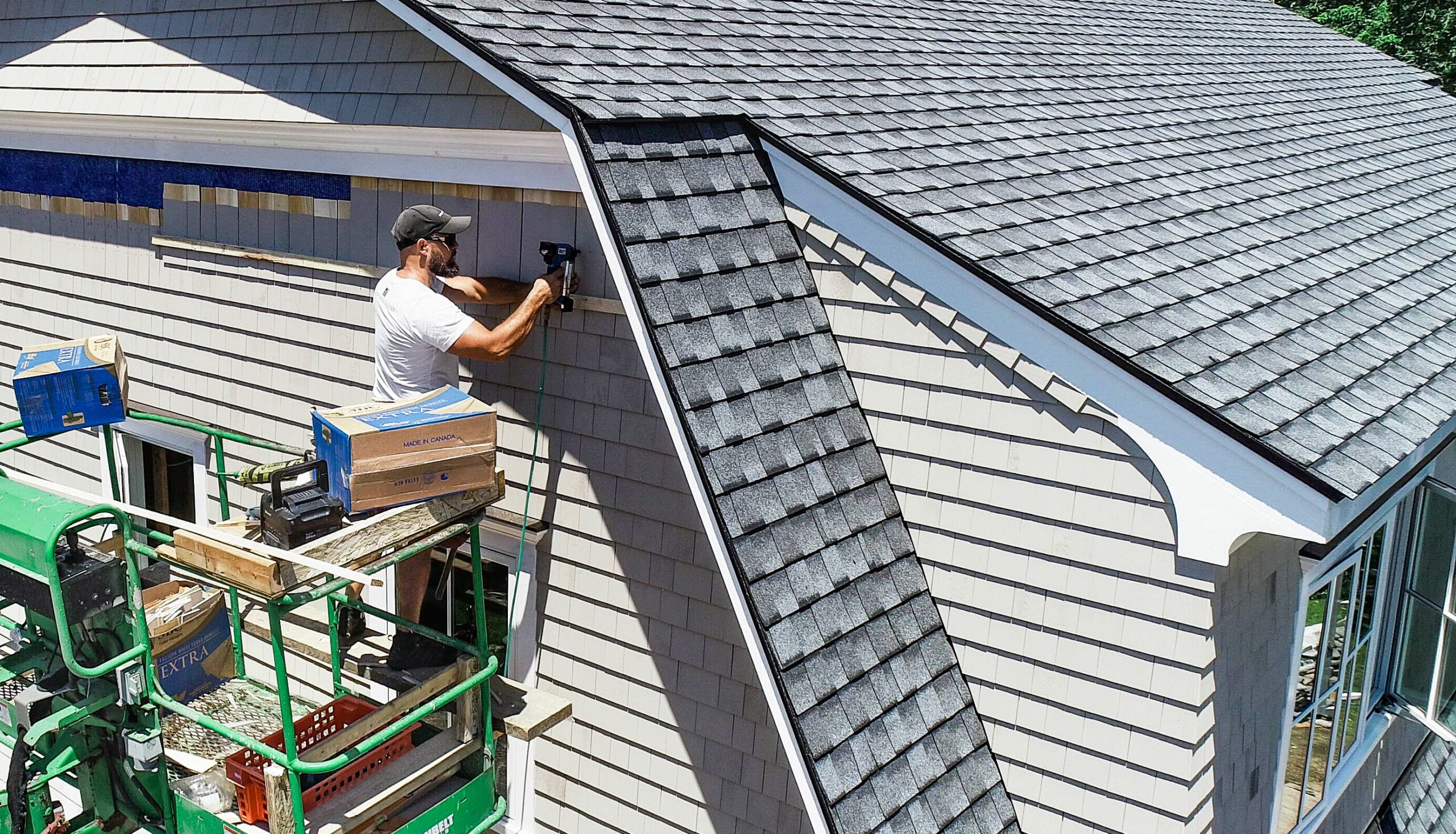
Sweenor Builders crew member Adam Spink uses a bucket to finish shingling the south gambrel gable end.
ROOF SHINGLES: GAF
EXTERIOR TRIM: Lifespan
Apprentice at Work
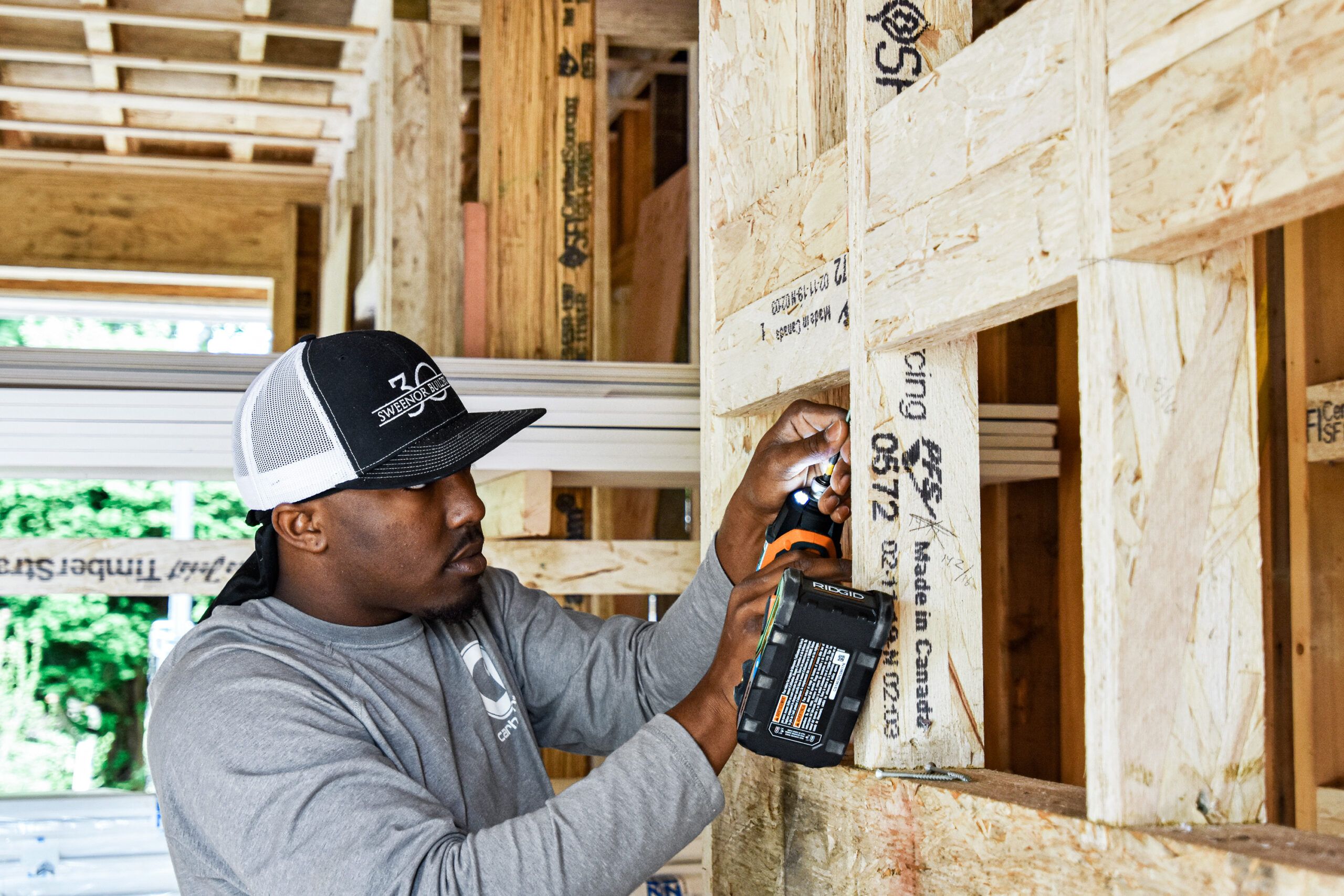
TOH GenerationNEXT apprentice De’Shaun Burnett installs blocking for the framing of the first-floor living area.
Open Plan Framing
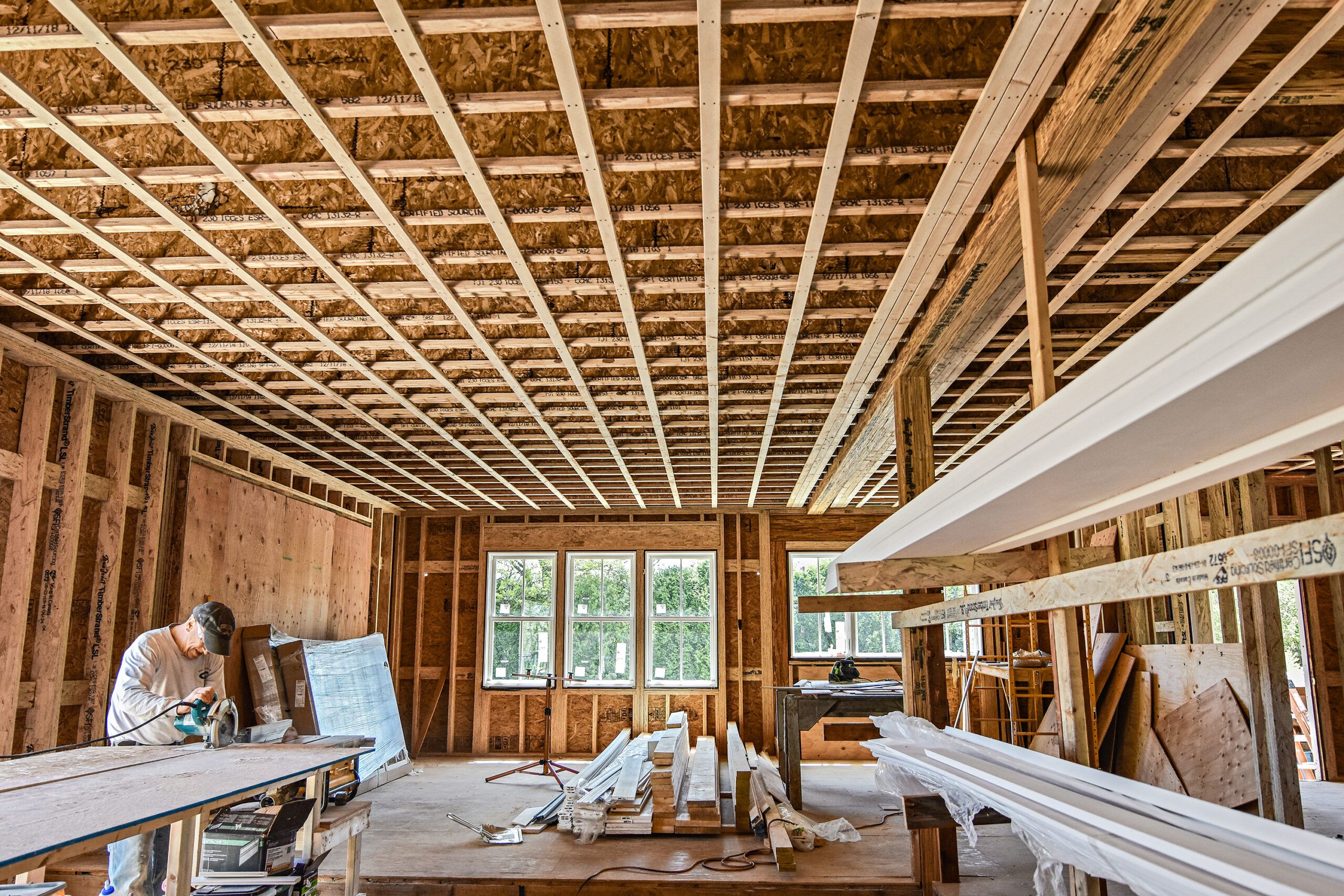
Crew member Wayne McDowell cuts down a plywood sheet in the rebuilt open-plan first floor. In this view, looking toward the kitchen’s south-facing windows, more plywood covers an opening on the left, which awaits patio doors.
FRAMING MATERIALS: Weyerhauser
WINDOWS: Marvin
Hoisting a Rafter Tail
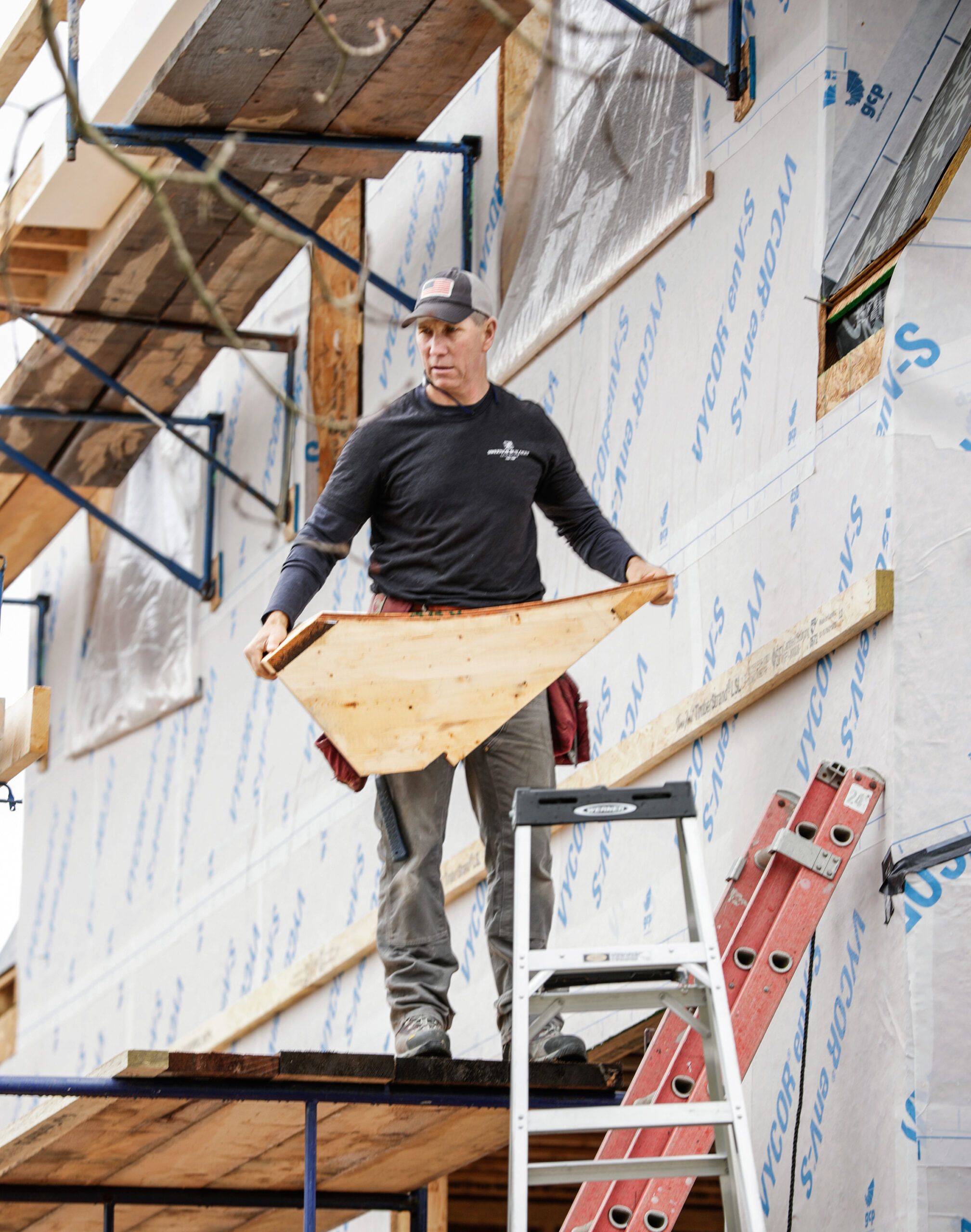
Jeff Sweenor hoists a rafter tail; 150 of these engineered-wood wedges were created using CNC (computer numerical control) milling for a uniform shape that will form the swoop detail around the base of the second-floor addition.
RAFTER TAILS: Lamco
Assist from Kevin
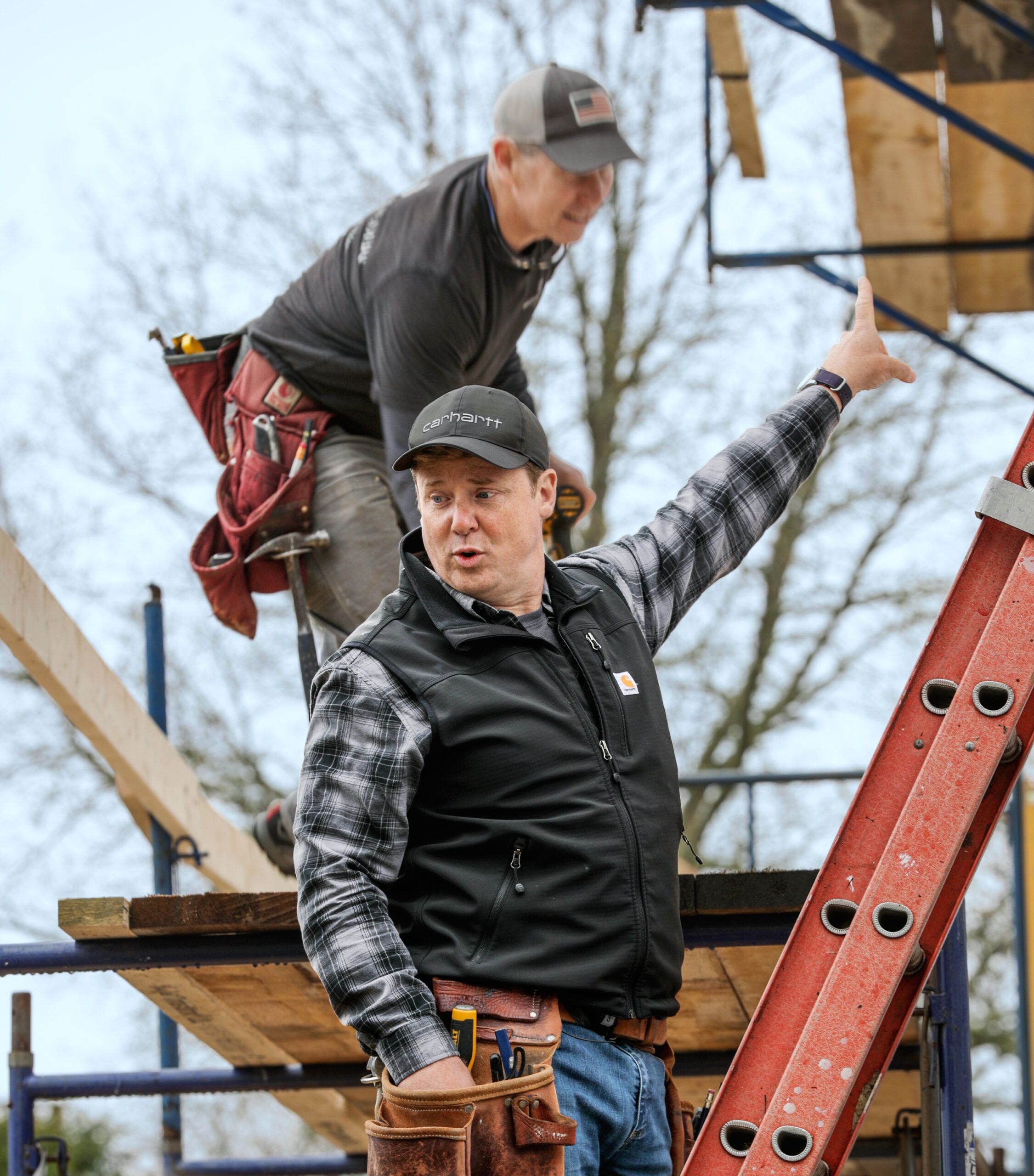
TOH host Kevin O’Connor lends Jeff Sweenor a hand in installing the series of rafter tails.
RAFTER TAILS: Lamco
Siding Details
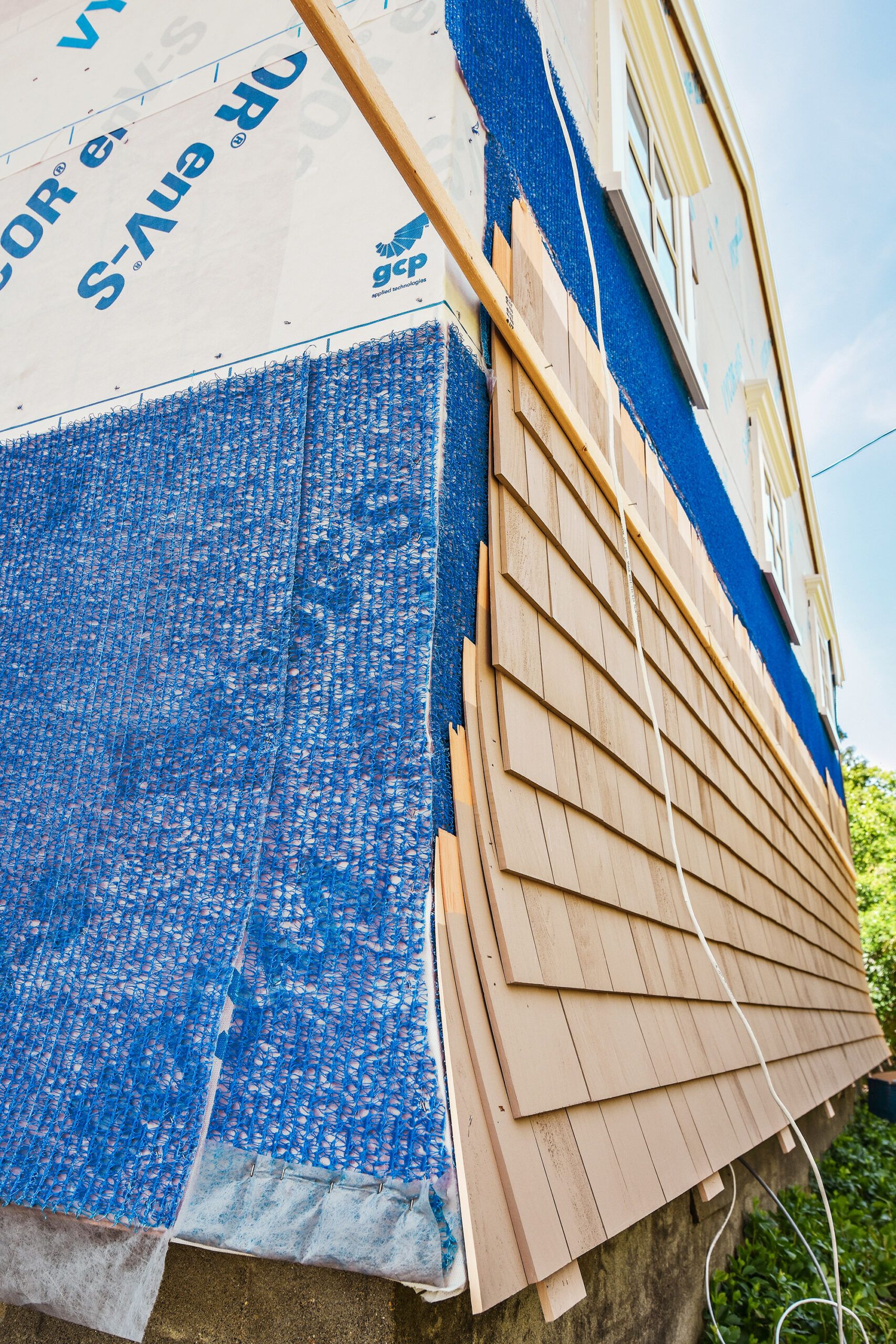
Cedar shingles are installed over a rain screen that allows water to drain and air to move, extending the life of the wood siding.
SHINGLE SIDING: SBC Cedar
RAIN SCREEN: Mortairvent