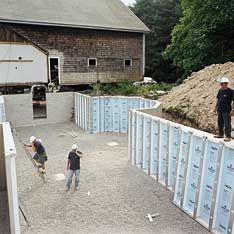
If you’d blinked, you might have missed the construction of the ell and the new master bedroom suite at the project house in Carlisle, Massachusetts. In the space of a single day, an empty hole acquired a finished foundation of precast, insulated concrete panels. A few days later, prefab I-joist floor sections went in. Then came framed, sheathed, and insulated walls — all at once, using structural insulated panels (SIPs) that were custom-made in a factory 800 miles away. A few more days and the SIP roof panels were lowered into place with a crane, followed by 12-inch-thick SIP floor panels for the 155-year-old barn.
It’s all part of the This Old House plan to demonstrate how modern building technology can help bring a tired old house back to life in a fraction of the time it used to take. By contrast, it would take TOH general contractor Tom Silva’s crew two weeks just to frame and sheathe this much house — about 7,000 square feet of exterior walls and roof — plus a day to insulate. That’s not taking into consideration the time needed to form and pour a concrete foundation and frame up 3,300 square feet of new floor joists and subfloor.
This form of panelized construction is still a niche business — about one percent of American homes are built with SIPs — but it’s easy to see why the industry is growing by 25 percent annually. “The panels are fast, they’re straight and true, and they don’t move around,” says Tom. Plus, they’re stronger and more environmentally friendly than stick construction. Still, speed is the main advantage for the TOH team, who have to adhere to a television show’s strict schedule. With the new construction taken care of, Tom and his crew will have the time they need to carefully renovate the older parts of the house.
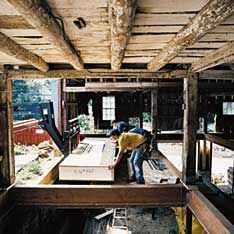
Foundation in a Flash
Beneath the SIP walls in Carlisle lies a foundation to match — custom-made of 26 precast, insulated concrete panels that were set in place by a crane one day in July and then bolted together. The precast concrete panels are a proprietary system manufactured by Superior Walls, a Pennsylvania-based company, primarily in factories located in the Northeast and upper Midwest, where full basements are the norm. Unlike the systems used in insulated concrete forms (ICFs), which are poured in place, the concrete in the Superior Walls panels is cured in a factory under ideal conditions, resulting in a wall that is virtually flawless and able to withstand 5,000 pounds per square inch of pressure. “You could probably get the same strength from concrete poured in place, but you’d need perfect job-site weather — no cold, no rain, and no blistering heat,” says Mel Zimmerman, the company’s founder.
Considering their strength, the concrete panels are remarkably thin — a 1 3/4-inch concrete face braced by a top and a bottom plate and concrete “studs” every 2 feet — all of it cast in one monolithic pour around a network of steel reinforcing bars. “It’s built like a bridge, only vertical,” says Zimmerman, who explains that the greatest pressure on any foundation is not from the weight of the house above but from hydrostatic pressure — the force of the water in the surrounding soil pushing on the walls.
But the system offers more than strength. Each panel is bonded to a foam envelope that provides insulation value up to R-12.5. The mix of the concrete makes it dampproof, so no additional water-resistant treatment is needed. In fact the company warrants against water penetration of its foundation walls for 15 years. “The basement will be a dry and comfortable living space with nine-foot ceilings,” commented Zimmerman as he watched a panel being lowered into place on a bed of crushed stone. (Independent footings aren’t necessary — they’re part of the wall — although Tom will need to pour a slab floor after the foundation goes in.)
Preattached galvanized steel nailers on each “stud” allow Tom to easily finish this basement in drywall, after wiring and plumbing are run. “It’s a great system if you’re planning to get a lot of use out of your basement,” says Tom. “When you look at it that way, it’s about the cheapest living space in a new home.”
The Carlisle ell and master bedroom foundation, about 237 linear feet, will cost about $21,000. Tom estimates that a poured-in-place foundation with insulation, interior furring strips, and waterproofing would have cost $28,000. But precast systems are not always cheaper than other foundations. The price depends in part on location because the panels are made in many different factories across the country. Any price advantage over poured-in-place would depend on shipping costs, and also the cost of wet-concrete delivery in your area. One thing is clear as workers put the last panel into place: No other foundation goes in as quickly. The company says most foundations are installed in just five hours — with no curing time required. “With a regular foundation,” says Tom, “I have to wait several days before I can start laying the sill plates. With this, we’re good to go.”
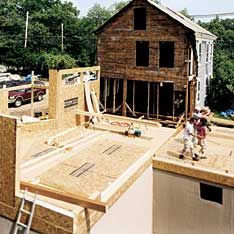
Fully Framed in a Day
Structural insulated panels have many advantages in today’s building world, key among them that they go up fast, withstand more stress than stick-frame construction, and conserve energy. That’s all due to the way they’re constructed, like giant ice cream sandwiches with two “wafers” of 7/16-inch oriented strand board (OSB) around 3 to 12 inches of expanded polystyrene foam (also known as beadboard), all of it bonded together with special glue.
It seems hard to believe that walls with no studs could be strong, but in fact these are three times stronger than conventional construction, according to Jim LeRoy of PanelPros, the Northeast installer for SIPs made by Insulspan, which manufactured the ones used in the Carlisle project. “The panels form a skin that’s very much like an airplane fuselage,” says LeRoy.
Those panels are fabricated using software that translates architectural drawings into machine codes, which in turn lay out panel sizes down to the fraction of an inch. “It’s a one-day job to manufacture them,” says Insulspan founder Frank Baker. “Contractors often wonder how long they’ll have to wait for the panels, but usually we’re ready before they are.”
Speed and strength are just part of the SIP equation. Because SIP walls have no studs, as long as they’re properly sealed there’s no place for heat and cold to seep through. “It’s a total energy envelope,” says Baker. So while an SIP’s R-value — the standard measure of thermal resistance — is already higher than that for fiberglass batts (a 6-inch SIP wall is rated at R-24 to R-27, versus an R-19 for a 6-inch stud wall with fiberglass), the overall performance is even greater. According to the U.S. Department of Energy, SIP construction can result in a 12 to 17 percent saving in energy costs, though tests currently under way at the Oak Ridge National Laboratory suggest that that saving may be even higher. A home built with SIP walls generally calls for smaller, less expensive heating and cooling appliances, notes TOH plumbing and heating expert Richard Trethewey.
However, because SIP homes are so tight, Richard recommends installing an air exchanger to cut down on the moisture trapped in the house. This added expense offsets the energy saving in the first few years. Moisture has also proven to be a problem with SIP roofs in colder climates. If the joints are not properly sealed, escaping moisture vapor can get trapped beneath the roofing, eventually rotting the OSB. That’s why when working with SIPs Tom takes no chances. On a simple gable roof, he ventilates by nailing furring strips to the OSB and adding another layer of 1/2-inch exterior-grade sheathing before putting on the felt and shingles. “This keeps the underside of the roof shingles cooler and the top side of the panels dry,” says Tom.
With a complex roof that has many intersections and valleys, as at Carlisle, Tom will roof right over the SIPs, but first the installers, in addition to joining the panels with flexible caulk, inject a foam sealant into the joints and tape the underside of the panels. They also tar the seams as a temporary measure before the roofing goes on. Tom takes an extra precaution by covering the whole roof with a layer of waterproof membrane before he lays the shingles.
Still another advantage of SIPS is that they’re environmentally friendly. First, they help conserve old-growth trees, since the OSB panels are made of fast-growing sustainable wood. And the controlled factory environment means less job-site waste and more recycling. Also, the foam itself is inert, and its manufacture does not use ozone-depleting chemicals. Making the foam, on the other hand, does require toxic substances, like benzene, a known carcinogen. Environmentalists are also concerned about the addition of widely used brominated flame retardants, which may be toxic and are probably “bioaccumulative,” meaning they hang around the environment forever. But Alex Wilson, editor of Environmental Building News, still gives SIPs high marks. “There are some issues related to materials used in SIPs, but because they allow us to build energy-efficient homes, they are considered green,” he says.
Two downsides of SIPs: They can be a draw to insects (unless treated with boric acid), and rodents can be attracted to the warmth of their insulated wall cavities. Another complication associated with SIPs is running wiring in the walls. SIP panels can be ordered with predrilled channels through the foam, designed to accommodate wires at standard heights for outlets and switches. (Plumbing chases can also be predrilled, although in cold climates you shouldn’t run anything but a vent pipe in an outside wall.) Another wiring solution is to use baseboard outlets, available in a range of styles. The most versatile method is to cut vertical slots into the SIP panel (through the wood and about half an inch into the foam) using a plunge router. “That gives you the flexibility to run wires wherever you want,” says LeRoy. Drywall covers the slots, and because the walls are so straight and completely sheathed in wood, even that goes up more quickly and with less waste.
Running the Numbers
Though it would seem that the speed of SIP construction would automatically lower costs with savings on labor, that isn’t always the case. The actual cost relative to conventional stick-frame houses depends on where you live. In southern climates, where job-site labor is fairly cheap and energy standards more relaxed, SIPs are generally more expensive than conventional framing. But in the North, SIPs can be competitive with 2-by-6 walls and spray foam. (Six-inch-thick custom-cut SIPs, like the ones at Carlisle, run $4.50 to $5.50 per square foot delivered.) To find out whether there’s a cost benefit to SIPs in your area, contact a manufacturer (www.sips.org has listings), who will run your house plans through their computer and give you a precise estimate at no charge. Then you can take that figure to your builder and stack it up against other options.
Where to Find It
Architect:
Jeremiah Eck Architects
Boston, MA
617-367-9696
Precast concrete walls:
Superior Walls
New Holland, PA
800-452-9255
SIPs:
Insulspan
Blissfield, MI
517-486-4844
Northeast Insulspan distributor and SIP installer:
Panel Pros
Keene, NH
800-721-7075
Green building newsletter:
Environmental Building News
BuildingGreen, Inc.
Brattleboro, VT
800-861-0954