Hidden Gems
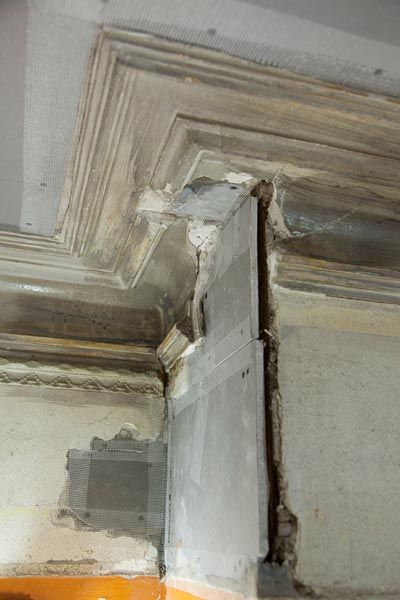
The question had been hanging over their heads for years. Eight feet overhead, to be exact. Ever since Heather and Malcolm Faulds bought their 1872 Italianate, in the Arlington suburb of Boston, five years ago, they wondered if there might be something interesting hidden above the suspiciously low ceilings of the parlor rooms.
But it wasn’t until their home became the star of the current TOH TV season that they would get an answer. Once TOH general contractor Tom Silva and the crew had set up shop, Tom wasted no time cutting a peephole in the ceiling. Heather stood at the foot of the ladder, waiting for his assessment. “Oh, you’ve got to see this,” he said.
Heather was up next, and she shined a flashlight into the dead space above the false ceiling. “The original ceilings were stunning,” she says. There was a robust medallion and cove-style plaster crown molding in a band around the dining and living rooms. “We were blown away.”
Shown: A strip of orange paint stopping abruptly a couple of feet below the plaster crown molding shows how much of the room had been closed in by an ugly drop ceiling.
Arlington Italianate House: Before
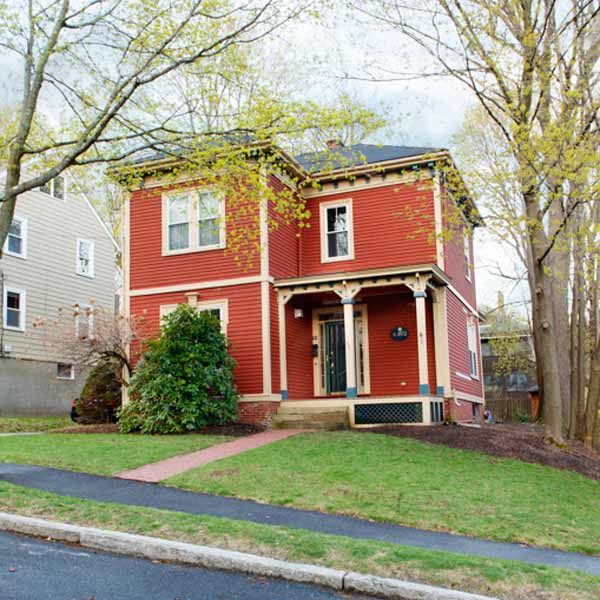
The discovery fit right into the couple’s overall approach for the renovation of their 2,100-square-foot home. “We really wanted to create a more open and brighter feel while preserving the period character of the house,” says Heather. The Fauldses, who have two children, are adding a master suite above a single-story bumpout at the back; a mudroom, a half bath, and a larger kitchen on the first floor; and finished space in the basement. In the process, though, they’re committed to preserving the historical features of the 141-year-old house, such as the corbeled cornice outside and the original stairs and balustrade inside.
Nowhere is that dedication more evident than in their decision to invest unbudgeted time and money in restoring the ornamental plaster. “We’re a bit puzzled that anyone would ever cover up these ceilings to begin with,” says Malcolm. Someone had used 2√ó4s and drywall to lower the ceiling height from 10 feet to 8 feet, probably, says Tom, to make heating the rooms easier.
Shown: The front of the 1872 Italianate will get a new front door, porch railing, and second-story window.
Holding on to The Past
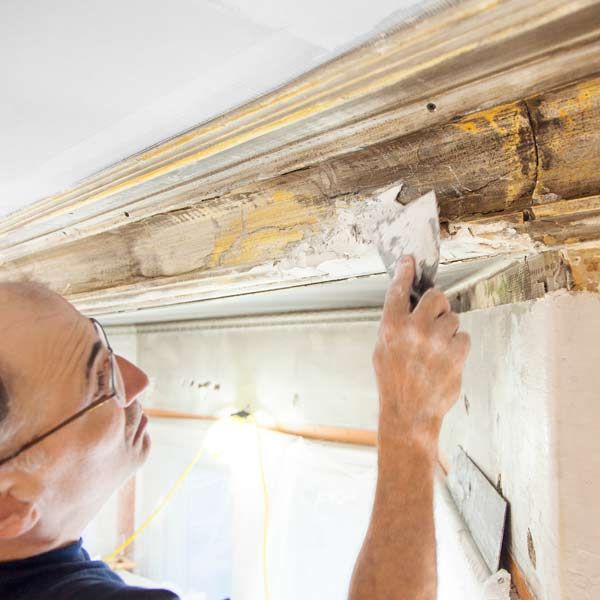
Being up high provides ornamental plaster with protection from the dents and dings of everyday life. Being covered up protects the details from being ripped out altogether by hasty homeowners. Still, the Fauldses’ ceiling would require a lot of work to restore. “The plaster is more than a century old, so it was in tough shape in some places,” says Bob Bucco, the plaster contractor on this and many past TOH TV project houses.
The Fauldses’ house was built on a rubblestone foundation, and as the structure settled over time, the framing twisted, causing the rigid plaster to crack. Large chunks of the crown molding had come off in a number of places. In the living room, the old plaster ceiling was largely intact, as was its medallion, minus one chunk near the edge. But in the dining room, the medallion was missing and needed to be re-created, and the entire ceiling had to be replaced.
But as Bucco—after 33 years in the trade—can attest, plaster is sturdy stuff, and moldings that are still well anchored to wall and ceiling can be repaired right in place—at a certain cost. “Sure, some people might have torn the old stuff out and replaced it with new materials,” says Bucco. “But I’m glad they decided to repair the original work because it fits the home, even with all the repaired dents and holes. New plaster molding looks too perfect.”
Shown: Bob Bucco, plaster contractor on the TOH TV project house in Arlington, Massachusetts, fills a gap in the original plaster crown molding.
Holding on to The Past
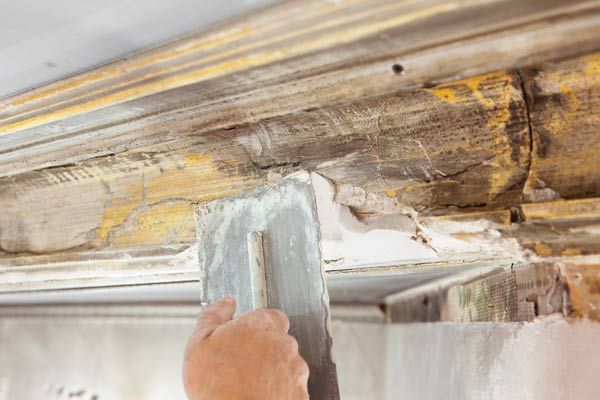
Restoring old plaster is a multistep process. Working from a 4-foot-high scaffold, Bucco and his team first went about patching all the holes in the walls and the living room ceiling, then covering the repairs with fiberglass mesh and a coat of veneer plaster. With a solid surface to build upon, the crew turned to the ornamental work.
Shown: Bucco packs the area with a layer of high-strength plaster; he scores the area and continues layering until the patch stands proud of the adjacent surfaces.
Shaping Contours
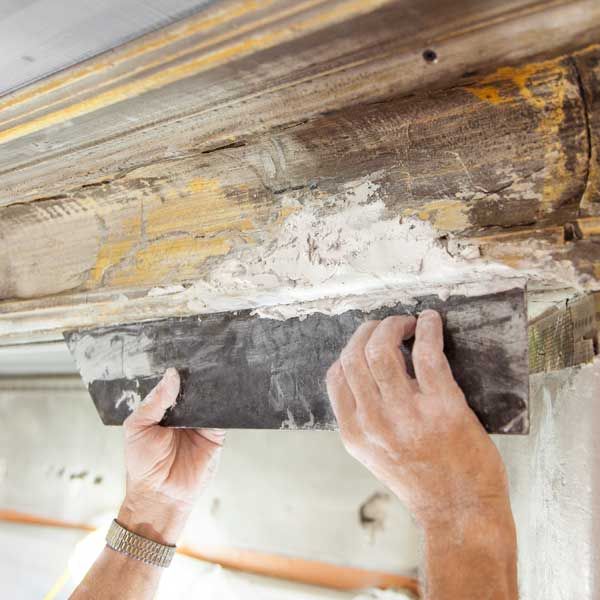
“The crown molding was the most tedious part of this job,” says Bucco. He started above the bay window in the dining room, filling a hand-size hole in the crown that went all the way down to the wall. He built it up with layers of high-strength molding plaster, mixed by hand in small batches. Then he dragged a stainless-steel straightedge, called a joining rod, over the repair like a squeegee. “It takes time and patience to get the surfaces to meet so that they look nice,” he said.
Shown: He drags a steel straightedge over the protruding plaster, shaping it to the contours of the old profile.
Sharpening Details
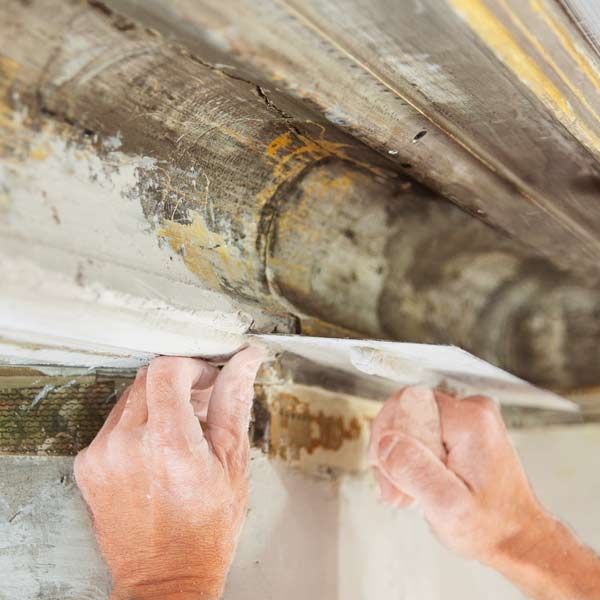
While the plaster is still soft, he uses a trowel to sharpen details by hand.
Timeless Restoration Methods
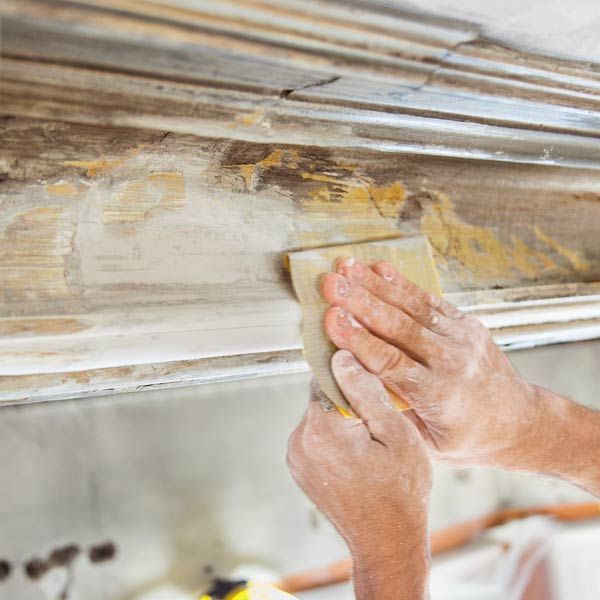
When the plaster finished setting, Bucco and his crew sanded the surfaces smooth by hand before they started work on the two dozen or so other damaged areas. Each hole in the crown took about 4 hours to repair, start to finish, using pretty much the same methods tradesmen would have used a century ago.
Shown: Once the repair has set, Bucco uses sandpaper to smooth out any seams, blending new and old.
Making The Mold
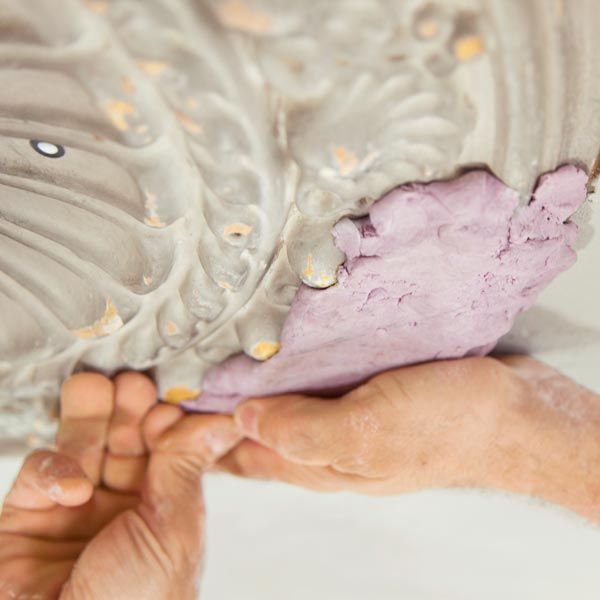
Repairing the ornate ceiling medallion required a different strategy. To replicate its details, Bucco created a mold and used it to cast a plaster patch. After Tom had done a bit of surgical trimming to both the patch and the edges of the hole with an oscillating tool, Bucco buttered the back of the patch with plaster and pressed it in place. Then he used his fingers to pack the joint with plaster. Holding up a plaster-coated hand, he said, “That’s the most important tool you need.”
Shown: Bucco presses a two-part modeling putty onto an undamaged section of the medallion to make a mold.
Light to Appreciate a Patched Medallion
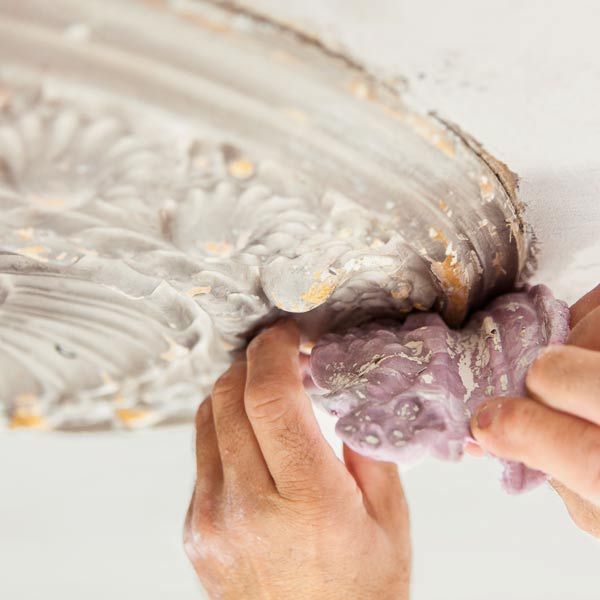
As part of the overall project, the passage between the two rooms was enlarged, opening up new sight lines from the dining room to the front windows of the living room and out onto the tree-lined street. “The false ceiling butted right on top of the casings, giving the room a cramped, dark look,” says Malcolm. “One of my favorite things about the new look is that it lets more light in and you can appreciate the casings.”
Shown: Once the putty sets, it remains flexible and can be peeled off.
Putting The Mold to Work
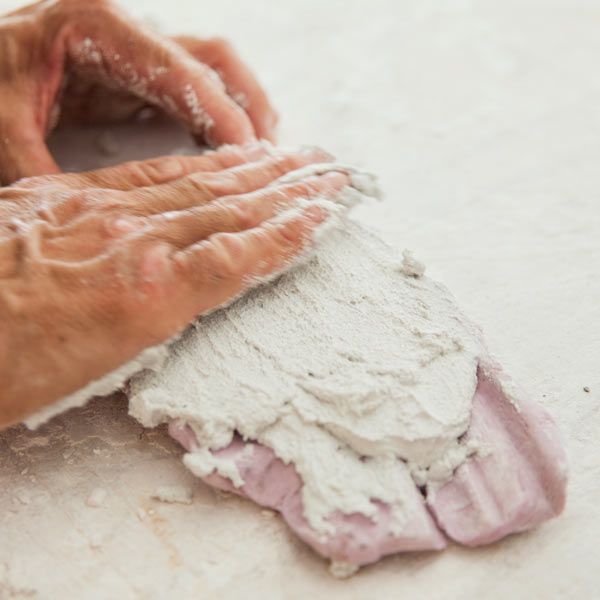
The transformation of the two rooms is dramatic. The restored 24 inches of headroom and the ornamental plaster provide a touch of grandness despite the rooms’ modest footprints.
Shown: He covers the mold in a thick layer of plaster, pressing it into all the detailed ornamentation.
Ornamental Plaster Saved
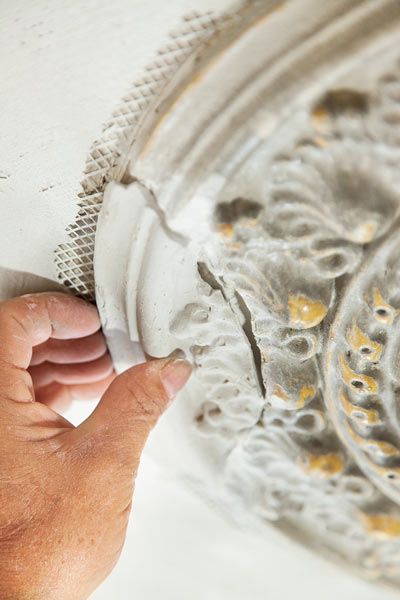
“We’re delighted we were able to save the ornamental plaster,” says Malcolm. “Someone in the past put a lot of work into making the rooms special, and now Bob has made them look fantastic again.”
Shown: Once the plaster sets, the patch gets trimmed to shape and plastered into place.
Replicating a Medallion With a 3-D Printer
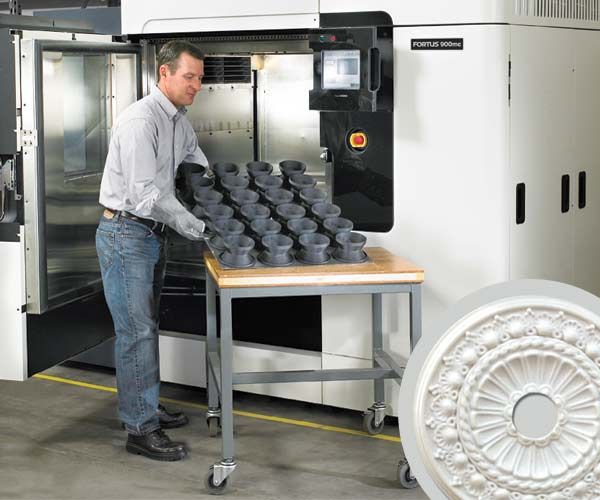
In contrast to the old-world methods used to repair the medallion in the living room, the TOH TV team turned to a decidedly 21st-century solution to replicate the one missing from the dining room. That solution came by way of David Kempskie, a senior technology consultant with AET Fab Labs, in Essex, Massachusetts. Using a handheld 3-D scanner, he stood below the living room medallion, made a three-dimensional digital map of it, and sent the map to a 3-D printer like the one at far left. The printer head moved back and forth, spraying millions of atomized droplets of resin with each pass and slowly building up a physical version of the digital file. The replica at left can be used to cast a new one in plaster or can go directly on the ceiling, to be primed and painted, as it did at the Faulds house.