Tin punching is a centuries-old craft that gives your decor a touch of rustic charm. Whether you’re looking to personalize your furniture or make custom light fixtures, learn the tools and techniques you need to master it.
What Is Tin Punching?
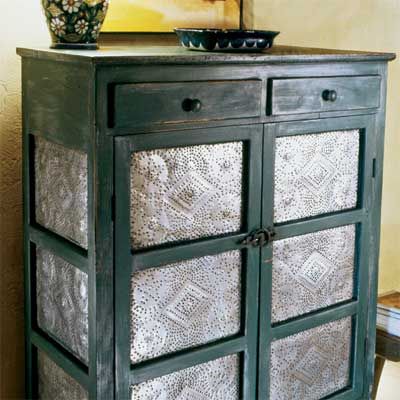
Tin punching, also known as pierced tin, is a decorative metalworking technique that originated in colonial America. Back then, it adorned everything from lanterns to pie safes. Today, it’s experiencing a revival among DIY enthusiasts. By punching small holes or indentations into thin metal sheets, you can create patterns that allow light to shine through, creating a beautiful lace-like effect.
Essential Tools For Tin Punching
To get started with tin punching, you’ll need a few basic tools and materials.
Patterns
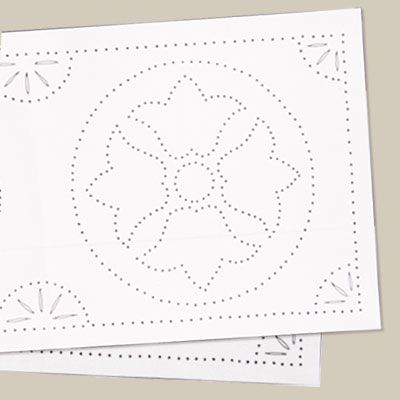
Using a pattern makes it easier to plan your design and transfer it onto the metal. You can sketch or print your design on plain printer paper, or purchase a predrawn option online.
Metal Sheets
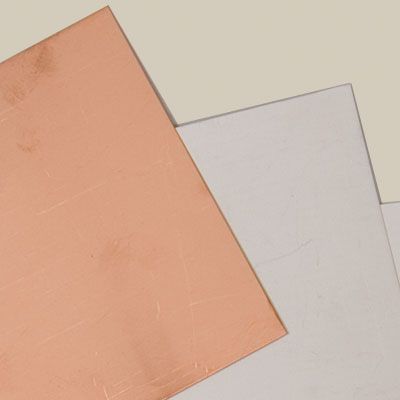
For most projects, 24- or 28-gauge metal works well. Modern crafters often use a variety of metals for their projects, including the following:
- Tin: Tin is classic, easy to work with, readily available, and ideal for beginners.
- Copper: Copper gives projects a warmer tone and slightly more durability than tin.
- Aluminum: Aluminum is lightweight, easy to punch, and resistant to rust.
Nailsets

Nailsets are the first of two types of tools you’ll use to punch the metal. They have round tips to make uniform dots of different sizes.
Cold Chisels

Cold chisels are generally in 1/4- or 3/8-inch sizes. They come in handy for punching out dashes and lines in the metal.
Hammer
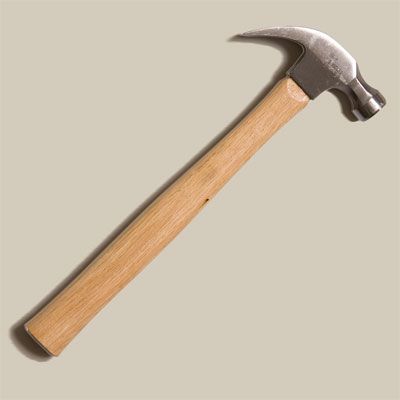
Claw hammers are your primary tool for tin punching. You’ll use them to drive nailsets and cold chisels through the metal.
Rawhide Mallet
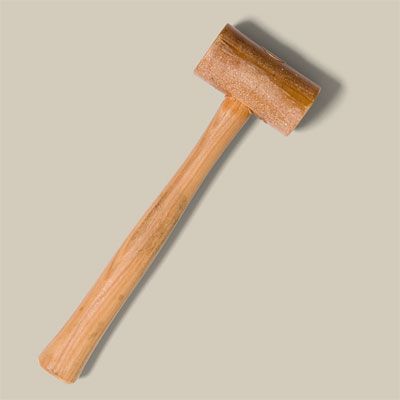
Once you’ve transferred your design to the metal, you’ll use a rawhide or rubber mallet for the finishing touches.
Tin Punching Step By Step
Follow these steps to create your own tin-punched masterpiece.
Getting Things Ready
Trace or print a pattern that fits your project’s dimensions. Back it with thin cardboard for durability.
Then, prepare the metal sheet for punching. Clean it with a mild soap and water solution and dry it thoroughly. Use tacks or double-sided tape to secure your pattern in place.
Punching Techniques
Do the punching work on a sturdy work surface, such as a piece of scrap wood. Hold your nailset or chisel perpendicular to the metal surface and strike down firmly with your claw hammer.
Start with the outline, then work from the center outward so the metal holds its shape. For more complex designs, punch a few holes at a time and check frequently for issues or bending metal.
Finishing Touches
Once you’re done punching, take off the pattern and flip the sheet over. Use your rawhide mallet to flatten any sharp points on the reverse side. Lightly sand the surface with a scouring pad, and apply a clear lacquer spray to prevent the metal from tarnishing.
Tips For Achieving Professional-Looking Tin Punching Results
To take your tin-punching projects to the next level, follow these tips:
- Practice punching techniques on a sheet of scrap metal before you start your main project.
- Vary your punches’ size and spacing to create pieces with depth and texture.
- Use fine-grit sandpaper to clean up any burrs or rough edges from the metal.
- Experiment with different finishes, such as paint or patinas, to enhance your designs.
Safety Precautions When Tin Punching
Tin punching involves working with sharp objects and metal sheets. To ensure a safe crafting experience, use work gloves when handling the metal and safety glasses to protect your eyes from shavings. If you’re finishing your piece with lacquer or other chemicals, work in a well-ventilated area.
Our Conclusion
With just a few basic tools and some practice, you can use tin punching to transform simple metal sheets into intricate works of art. All you need is a high-quality pattern, some basic tools, and a little practice with different techniques.