For the last three years, since moving into their 1909 Arts and Crafts house in Arlington, Massachusetts, Nick and Emily Deldon have lived in dread of their heating-oil bill. “During the coldest part of the winter, we were spending about $3,000 a month on fuel deliveries,” says Nick. “It was costing us more than our mortgage just to stay warm.” Thankfully, the Deldons’ money-down-the-drain feeling has come to an end, as their house undergoes a top-to-bottom renovation on the current season of This Old House, with general contractor Tom Silva in the lead.
To save energy, Tom’s crew, with assistance from a small army of subcontractors, installed new windows, sprayed foam insulation into the walls and attic, and, perhaps best of all, put in a new gas boiler to replace the inefficient, oil-fired beast in the basement. Richard Trethewey, This Old House plumbing and heating expert, figures that with these envelope upgrades and a 95 percent efficient condensing boiler using the latest controls, the Deldons will cut their fuel bills by more than half, without sacrificing comfort.
Homeowners began converting to fuel oil back in the 1940s, when it was marketed as a cleaner alternative to coal. By 1960, 32 percent of houses in the United States had oil heat, but its use has since declined to just 7 percent. Oil remains popular in the Northeast, however, where more than 30 percent of homes still burn it. But Nick was done with oil. “I was constantly worried about running out,” he says. “And I’d have to keep the driveway clear so that trucks could make deliveries.”
Converting to natural gas, which feeds continuously into houses via underground pipes, would eliminate those worries. And they could say goodbye to the rusty 275-gallon steel oil tank lurking in their basement.
These tanks can leak at their fittings and perfume the basement with an oily aroma. Their walls can also corrode from the inside, where sludge—a mix of rust particles, water, oil contaminants, and bacteria—sinks to the bottom.
To make their tank go away, the Deldons hired Removal Specialists, a local firm experienced in decommissioning and taking out fuel oil tanks. “This is not a do-it-yourself job,” Richard says. “There are strict regulations governing how the oil and tank must be removed and disposed of. The risk of an accidental oil spill, and the cost of cleaning it up, is just too high to do a removal any other way.”
In the Deldons’ case, the work took only a few hours and the bill came to just $325, plus $50 for a permit from the Arlington fire department. A disposal ticket at the end of the process provided the proof that everything had been handled properly.
To see what’s involved in readying a tank for removal and giving it the heave-ho, read on.
TOH Tip: “To find a firm that’s qualified to remove oil tanks, talk to your local fire department. They issue tank-removal permits and should know which companies do good work. Then, make sure whoever you hire carries pollution-liability insurance and is OSHA-trained and certified.” —Richard Trethewey, TOH Plumbing and Heating Expert
At the Arlington project house, TOH’s Richard Trethewey and Removal Specialists’ project manager Shawn Clarke watch as one of Clarke’s crew pumps fuel oil from the soon-to-be-removed tank. Everything in the tank as well as the tank itself has to be removed, recycled, or reused according to strict guidelines established by the state of Massachusetts.
Steps for Removing a Fuel Tank
Step 1: Pump out the tank
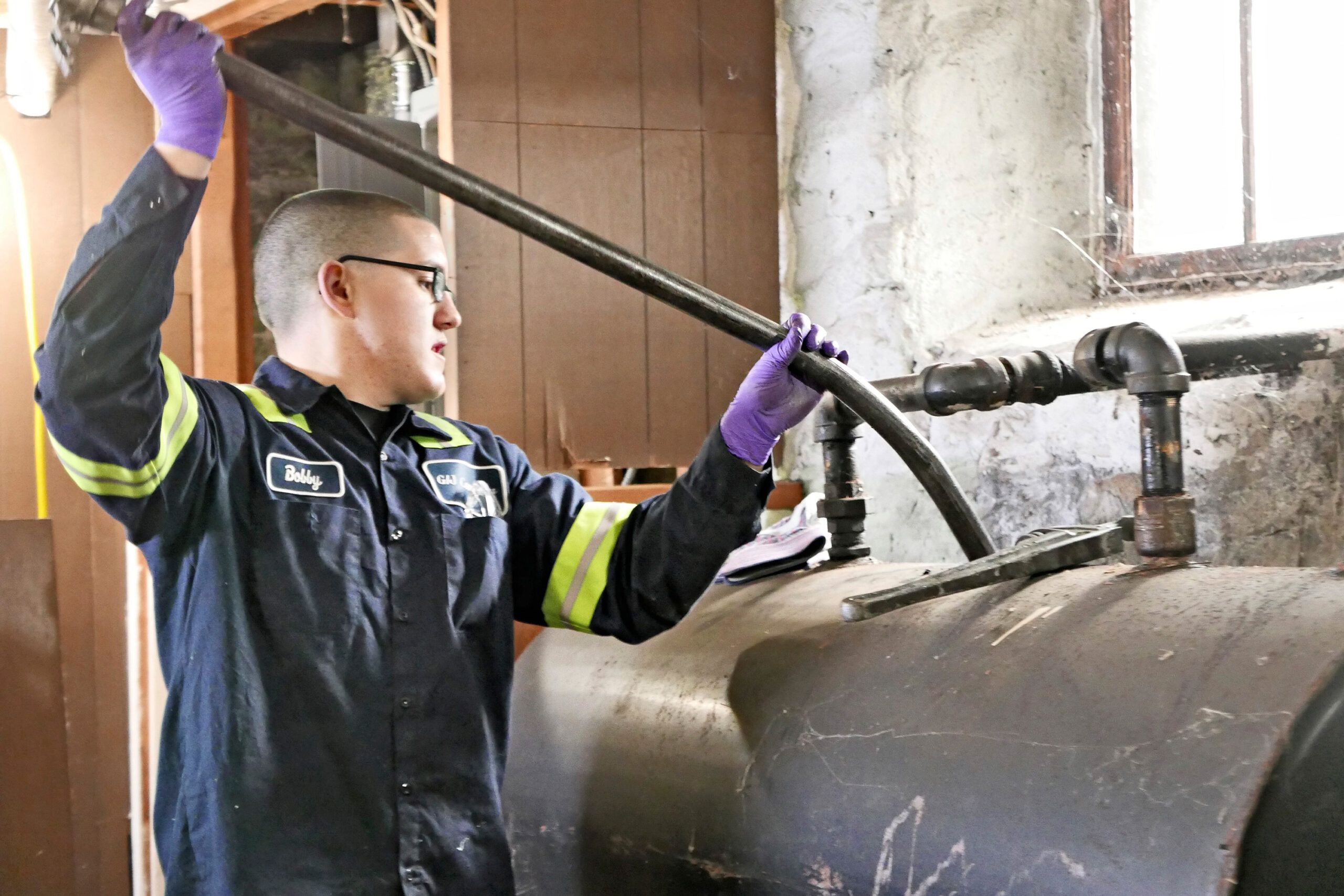
After removing the tank’s gauge, Removal Specialists Robert Crowe inserts the hose that will suck out the uncontaminated fuel oil. He connects the hose to an explosion-proof transfer pump, which feeds the oil through another hose into a drum outside. That leftover oil will then be filtered and used for heating.
Step 2: Cut the tank open
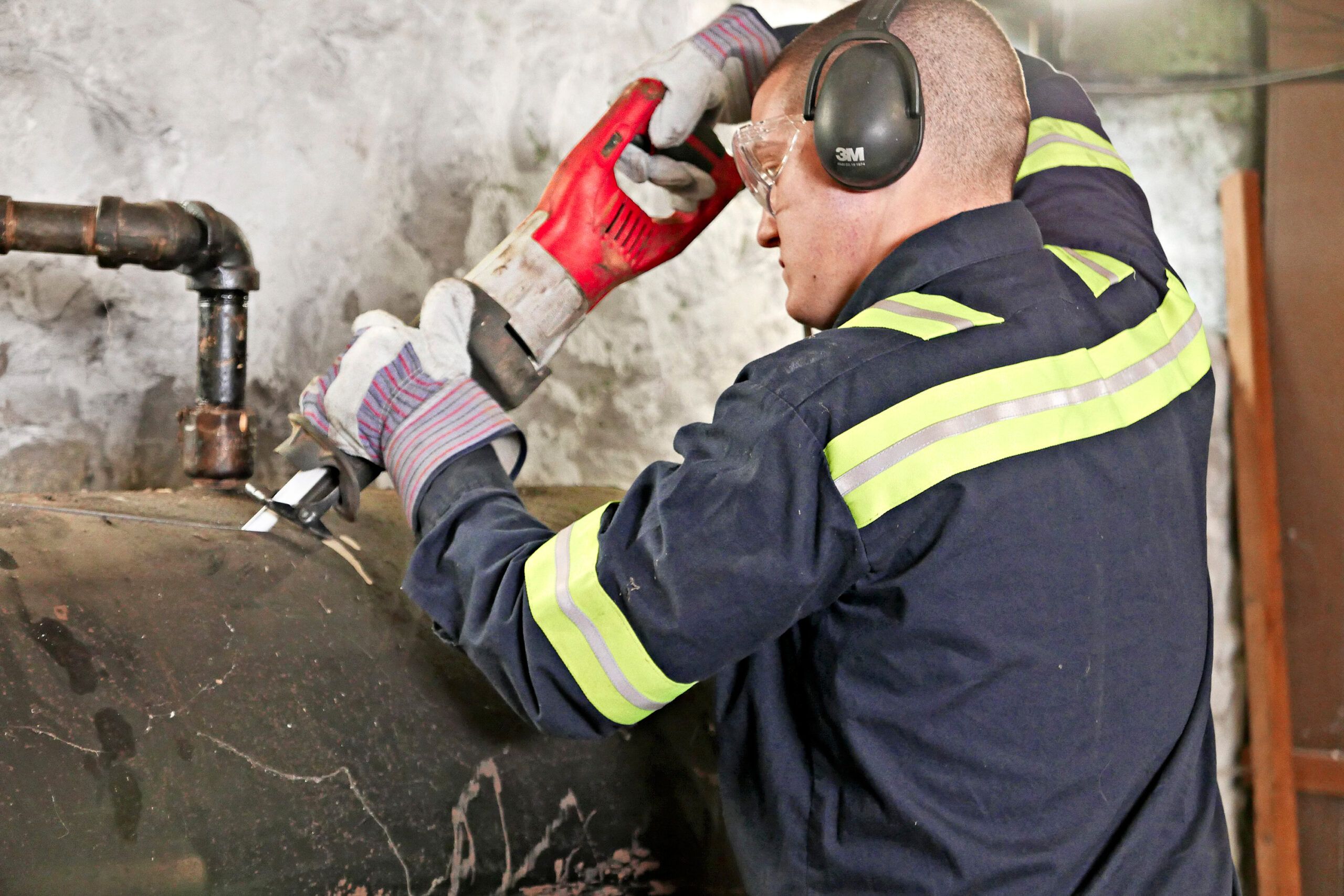
With the fuel oil removed, Crowe slices through the tank’s 12-gauge wall with a reciprocating saw fitted with a metal-cutting blade. Since fuel oil has a high flash point, there’s no concern that the hot metal sparks thrown off by the blade could ignite any fumes trapped in the tank.
Step 3: Clean the tank
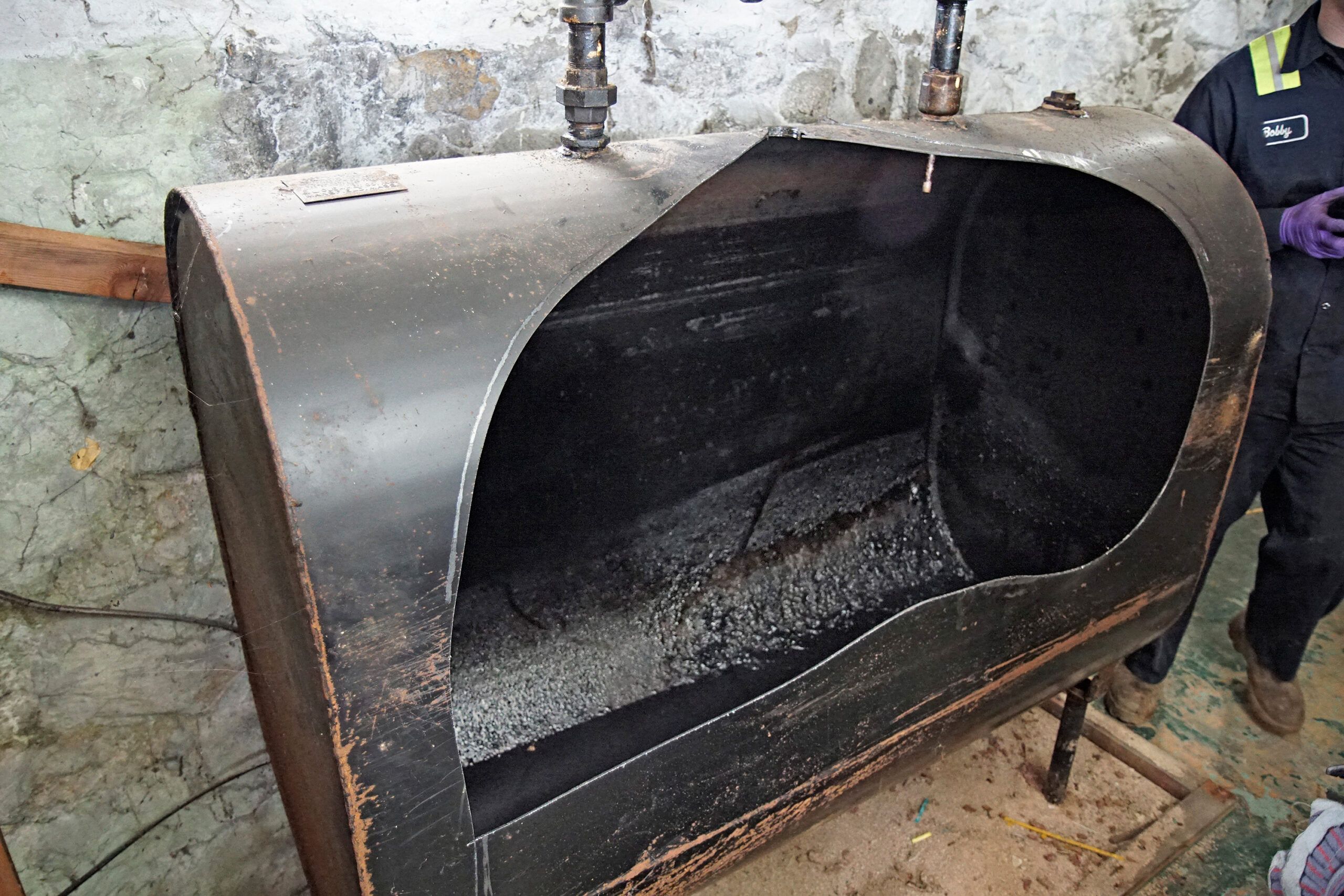
The hole that Crowe cuts into the side of the tank is wide and deep enough for him to reach in and scrape down the inside walls. When they’re clean, he scoops the sludge—a thick, black slurry that accumulates in the bottom of all oil tanks over years of use—into 5-gallon buckets.
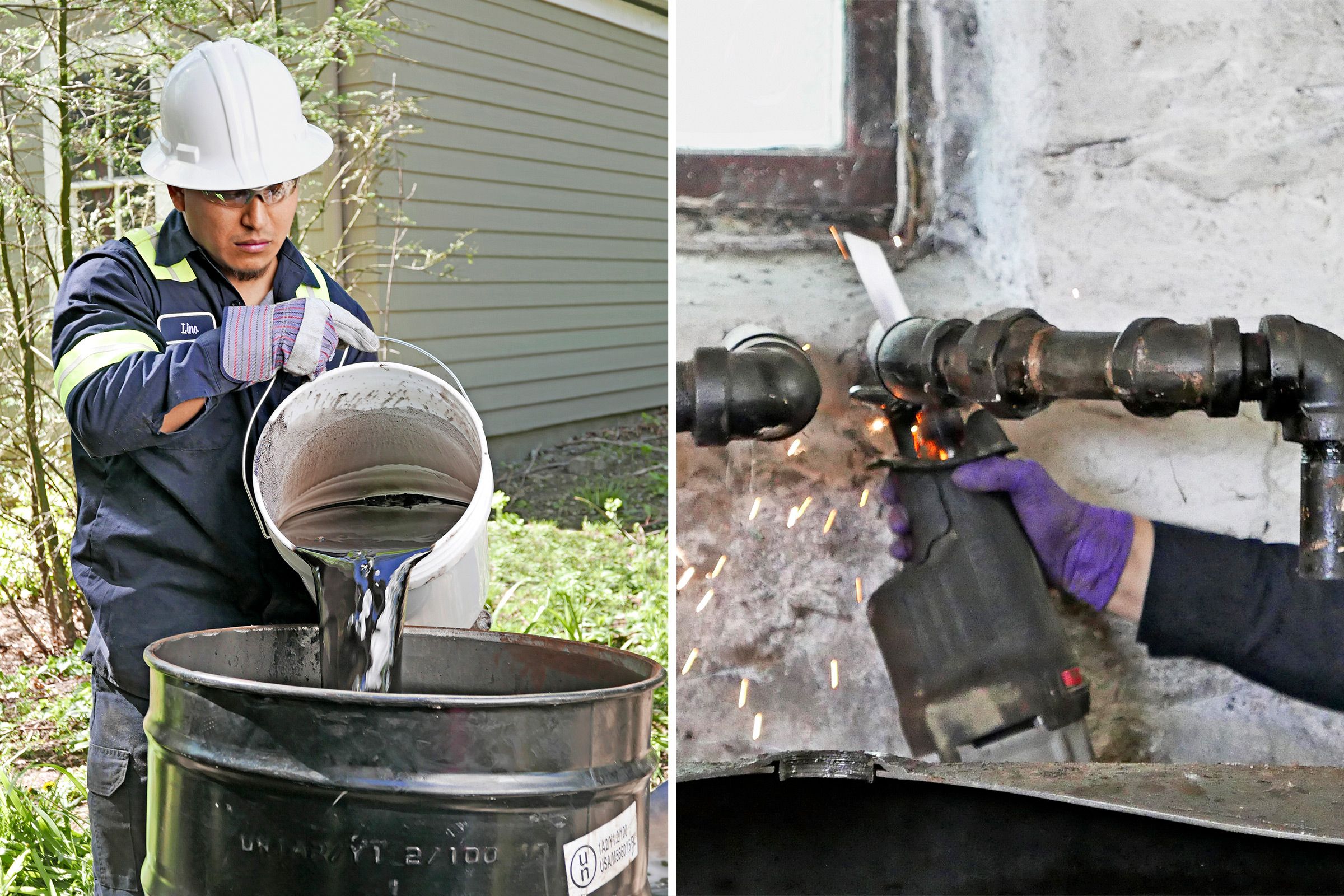
Step 4: Recycle the sludge
Lino Hernandez pours the sludge into a 55-gallon drum. When filled, the drum will be taken to a specialized waste-management facility that processes the sludge so it can be burned for industrial use.
Step 5: Cut the pipes
Because an oil delivery to a disconnected pipe could result in a disastrous spill, Crowe severs the tank’s vent and fill pipes and removes them from the foundation. He then fills the holes with a concrete-patching compound.
Step 6: Move it out
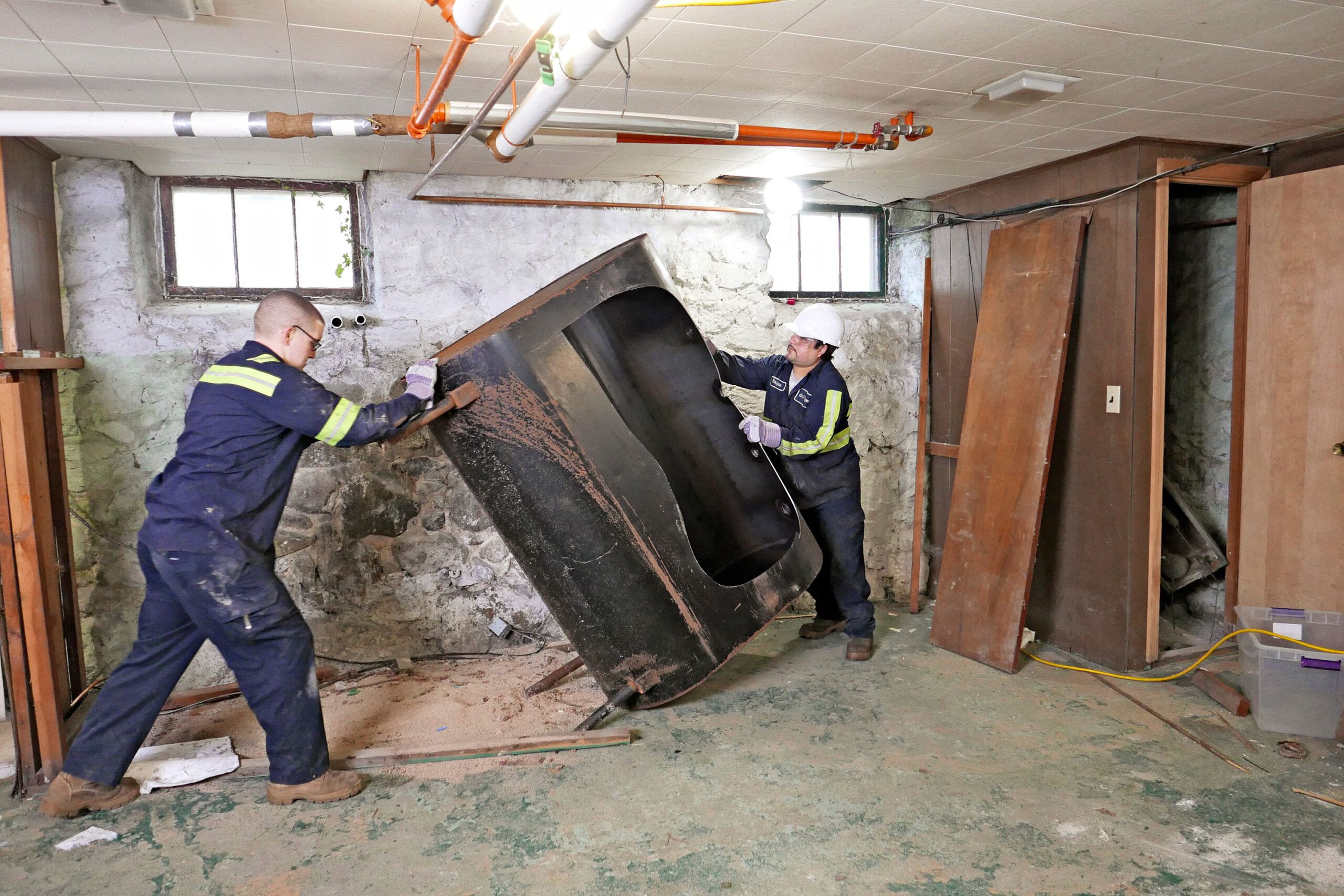
Crowe and Enrique Cobos-Cordero muscle the empty tank up and out the basement bulkhead. The tank will be taken to a state-certified yard, where it will be inspected and scrapped and then carried to a steel mill to be melted down.
MORE: