Retaining walls are more than just stacked stone, block, or timber—they are complex structures designed to hold back soil and create usable space on sloped properties. These carefully engineered systems wage an ongoing battle with gravity, restraining tons of saturated soil that would otherwise slump and slide away from foundations or damage surrounding landscapes. While they may appear simple, retaining walls require thoughtful planning and precise execution to ensure their effectiveness and longevity. This guide will help you understand the basics of engineering retaining walls, different structural techniques, and when you should enlist professional help.
What Is a Retaining Wall?
A retaining wall is a structure designed to restrain soil to a slope that it would not naturally keep to, typically a steep, near-vertical, or vertical slope. These walls are built to resist the lateral pressure of soil, water, and other materials behind them. The primary function of a retaining wall is to prevent downslope movement or erosion and provide support for vertical or near-vertical grade changes.
Common Uses for Retaining Walls
Retaining walls serve various purposes in both residential and commercial settings, including the following:
- Create level areas on sloped properties for landscaping or construction.
- Prevent soil erosion on hillsides.
- Manage water runoff and improve drainage.
- Increase usable outdoor space by terracing steep landscapes.
- Protect foundations from sliding soil pressure.
In residential areas, retaining walls can transform unusable sloped yards into functional spaces for gardens, patios, or play areas. For commercial properties, they can maximize land use and create aesthetically pleasing landscapes.
Key Factors in Retaining Wall Design
Designing an effective retaining wall requires careful consideration of the soil, water management, and climate.
Soil Composition and Pressure
The type of soil behind the retaining wall significantly impacts its design. Different soils exert varying amounts of pressure on the wall:
- Clay soils retain water and can exert substantial pressure
- Sandy soils drain well but may require additional reinforcement
- Rocky soils can be unpredictable and may need special design considerations
Engineers analyze soil composition to determine the appropriate wall design and reinforcement needed. For instance, a four-foot-high, 15-foot-long wall could be holding back as much as 20 tons of saturated soil, emphasizing the importance of proper soil assessment.
Water Management and Drainage
Poor drainage, resulting in saturated soil and frost heaving, is the main cause of wall failure. To prevent this, take the following steps:
- Install a layer of gravel behind the wall
- Use landscape fabric to prevent soil from clogging the gravel
- Include a perforated drainpipe at the base of the wall
- Ensure proper grading to direct water away from the wall
These measures help relieve hydrostatic pressure and prevent water from accumulating behind the wall, which could lead to structural damage over time.
Climate Considerations
Local climate plays a significant role in retaining wall design:
- In areas with freeze-thaw cycles, walls must be built below the frost line or on well-drained gravel to prevent frost-heaving.
- Regions with heavy rainfall require robust drainage systems.
- Hot, dry climates may need designs that account for soil shrinkage and expansion.
Engineers must factor in these climate-specific challenges to ensure the wall’s stability throughout various weather conditions.
Types of Retaining Walls
Retaining walls can be engineered in several ways depending on the needs of the landscape design and materials selected.
Gravity Walls
Gravity walls rely on their own weight and sometimes the weight of the soil in front of them to resist pressure from behind. These walls are typically used for shorter heights and can be constructed from various materials:
- Concrete blocks
- Natural stone
- Cast-in-place concrete
Gravity walls are simple in design but limited in height, usually not exceeding three or four feet without additional reinforcement.
Cantilever Walls
Cantilever walls are L-shaped reinforced concrete structures that use the weight of the backfill to improve stability. They consist of a thin stem and a base slab, both of which are reinforced with steel. Cantilever walls are more efficient than gravity walls and can be used for greater heights, typically up to 25 feet.
Anchored Walls
Anchored walls add extra support through cables or other tie-backs anchored in the soil or rock behind the wall. This type is used when very tall walls are needed or when space is limited behind the wall. Anchored walls can be built to significant heights and are often used in highway and bridge construction.
Mechanically Stabilized Earth (MSE) Walls
MSE walls are composite structures made of alternating layers of compacted backfill and reinforcement elements like geotextiles or metal strips. The facing can be precast concrete panels, modular blocks, or even vegetation. MSE walls are cost-effective for tall walls and can be built quickly.
Materials for Retaining Wall Construction
Retaining walls can be made with a variety of materials, each with distinct advantages and visual appeal. Here are four different types of retaining walls to consider for your landscape.
Concrete Retaining Walls
Concrete is a versatile and strong material for retaining walls. It can be poured in place or used in precast blocks.
Upside: Strong and durable. Well-designed and properly drained concrete walls rarely fail.
Downside: Bare concrete isn’t particularly attractive, though it can be veneered with masonry or formed with decorative designs.
Cost: Around $30–$50 per square face foot installed, according to Angi.
Remember: Follow all rules for landscape fabric, drainage, and backfill. The footing should be below frost depth or on well-drained gravel that reaches this level.
Timber Retaining Walls
Timber walls offer a natural look and are relatively easy to construct for DIY enthusiasts.
Upside: Moderately challenging to build by yourself up to four feet high.
Downside: Not as long-lived as masonry. Making square cuts can be challenging.
Cost: $15–$30 per square face foot installed, according to Angi’s cost guide.
Remember: Use eight-foot-long, 6×6-inch pressure-treated wood designated for ground contact. All timber walls require deadmen (six-foot-long, T-shaped tiebacks buried in the hillside) every four feet at midwall height or higher.
Stone and Brick Retaining Walls
Stone and brick walls offer a classic, aesthetically pleasing option for retaining walls.
Upside: Handsome rustic appeal for stone; more formal look for brick.
Downside: Stone-wall masonry is harder than it appears. Brick masonry also requires skill to achieve a professional look.
Cost: About $20–$100 per square foot for stone, and about $20–$25 per square foot for brick, via Angi.
Remember: A mortared wall needs a footing and a drainage system to defeat frost heaving. A dry, unmortared wall allows water to seep through, naturally relieving pressure behind it.
Interlocking Concrete Block Systems
Interlocking block systems, also called segmented retaining walls, offer a balance of strength and ease of installation.
Upside: Mortar-free and easy to assemble. Units are small and modular, allowing for curved or tapered walls.
Downside: You can’t mix and match manufacturer’s systems. Some systems with metal pins can be challenging to align perfectly.
Cost: About $45–$270 per square foot installed, depending on block configuration and site, according to HomeGuide.
Remember: Use the manufacturer’s calculators to determine how many blocks, pins, and tiebacks you’ll need. Cap walls with flat units or stone held down with silicone caulk.
The Engineering Process for Retaining Walls
Engineering a retaining wall involves a systematic approach to ensure the structure can withstand the forces acting upon it. This process includes thorough site analysis, precise calculations, and detailed design planning.
Site Analysis and Soil Testing for Retaining Walls
Before designing a retaining wall, engineers must conduct a comprehensive site analysis. This includes:
- Topographical surveys to understand the terrain
- Soil testing to determine composition, strength, and drainage characteristics
- Assessment of groundwater conditions
- Evaluation of potential loads, including nearby structures or traffic
Soil testing is crucial as it informs the wall’s design and helps prevent failures due to soil instability or excessive pressure. Engineers may use various methods, including bore samples and penetration tests, to gather this information.
Structural Calculations and Load Bearing Walls
Once site data is collected, engineers perform complex calculations to determine:
- The lateral earth pressure the wall must resist
- The wall’s stability against overturning, sliding, and bearing capacity failure
- Required reinforcement for concrete or masonry walls
- Appropriate dimensions and materials for the wall and foundation
These calculations take into account factors such as soil weight, water pressure, surcharge loads, and seismic forces where applicable. For walls over four feet tall or those supporting significant loads, we find it crucial to have these calculations performed by a licensed engineer.
Creating Detailed Retaining Wall Design Plans
The final step in the engineering process is creating detailed design plans. These plans typically include:
- Wall dimensions and cross-sections
- Material specifications
- Reinforcement details
- Drainage system layout
- Construction sequence and methods
- Safety features and erosion control measures
These plans serve as the blueprint for construction and are essential for obtaining necessary permits and ensuring the wall is built to specifications.
Building Techniques for Retaining Walls
Constructing a retaining wall correctly will ensure that it lasts a long time. Attention to detail during the building process can prevent many common issues that lead to wall failure.
Proper Foundation Preparation
A solid foundation is essential for any retaining wall. The process typically involves:
- Excavating to the proper depth, which should be below the frost line in colder climates
- Creating a level base with compacted gravel
- Installing a concrete footing, if required by the design
For nonmortared walls, a gravel-filled trench dug below the frost line is often sufficient. In areas without freezing concerns and well-draining soil, scraping away topsoil may be adequate for smaller walls.
Backfilling and Compaction Methods for Retaining Walls
Proper backfilling is critical for the wall’s performance:
- Replace native soil with 3/4-minus gravel (no stones under 3/4 inch in diameter) or “bank-run” gravel (washed stones 1/4 inch to 6 inches in diameter).
- Shovel at least a 4-inch layer of gravel onto the landscape fabric.
- Grade this layer so it slopes 1 inch for every 4 feet, allowing water to drain away.
- Lay in a 4-inch perforated PVC drainpipe at the base of the wall and cover it with gravel.
Shovel in backfill as you build the wall, one tier at a time. Don’t add all the backfill at the end—it won’t compact thoroughly. Tamp down the gravel as you go with a heavy hand tamper. Behind the top tier of the wall, add 6 inches of topsoil and lightly compact it.
Battering and Deadmen-Tieback Systems
All retaining walls should lean into the hill 1 inch for every 12 inches of height. Timber walls 4 feet or higher should be tied to the hillside with “deadmen” anchors (6-foot-long, T-shaped tiebacks buried in the hillside) attached to the wall every 8 feet, extending 6 feet back to a 2-foot-wide T-bar.
Some interlocking block systems do not include deadmen if the design allows backfill to secure the blocks individually in place. Still, others require geo-grid, weblike tiebacks that get buried in the backfill. Check the manufacturer’s literature to find out what you need.
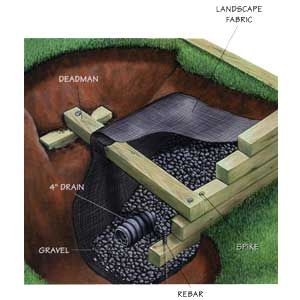
Installing Drainage Systems for a Retaining Wall
Effective drainage is crucial to prevent water pressure buildup behind the wall:
- Lay landscape fabric in a C-shape, with the open end facing downhill.
- Add a layer of gravel sloped one inch for every four feet to direct water away.
- Install a four-inch perforated PVC drainpipe at the base of the wall.
- Cover the pipe with gravel and wrap the fabric over it.
This system helps channel water away from the wall, reducing the risk of soil saturation and pressure buildup.
Maintenance and Longevity of Retaining Walls
Regular retaining wall maintenance can prevent minor issues from becoming major problems and extend the wall’s lifespan significantly.
Regular Inspection Procedures
Implement a routine inspection schedule to catch potential issues early:
- Check for any signs of bulging or leaning in the wall
- Look for cracks or deterioration in the materials
- Ensure drainage systems are clear and functioning properly
- Examine the soil at the top and bottom of the wall for erosion
- Inspect any visible reinforcement elements for signs of corrosion
Conduct these inspections at least once a year, and more frequently after severe weather events or earthquakes.
Common Retaining Wall Issues and Repairs
Address common problems promptly to prevent further damage:
- Cracks: Small cracks can often be filled with masonry caulk. Larger cracks may require professional assessment.
- Bulging: This can indicate soil pressure issues. Consult an engineer if you notice significant bulging.
- Drainage problems: Clear clogged drains and ensure proper grading around the wall.
- Erosion: Add soil to eroded areas and consider additional landscaping to prevent future erosion.
- Leaning: Minor leaning might be corrected by adjusting backfill. Severe leaning requires professional evaluation.
Extending the Lifespan of Your Retaining Wall
To maximize the longevity of your retaining wall:
- Maintain proper drainage around the wall
- Avoid planting large trees or shrubs near the wall that could disrupt the soil
- Keep heavy loads away from the top of the wall
- Apply sealants to concrete or masonry walls as recommended
- Replace deteriorated materials promptly
With proper care, a well-constructed retaining wall can last for decades, providing both functional and aesthetic value to your property.
When To Hire a Professional Engineer for Your Retaining Wall
While some retaining wall projects can be DIY endeavors, there are situations where professional engineering expertise is not just beneficial, but necessary.
Complex Site Conditions
An engineer should be consulted when dealing with any of the following scenarios:
- Steep slopes (greater than 3:1 ratio)
- Poor soil conditions or unstable ground
- Areas with high water tables or drainage issues
- Sites with existing structures nearby that could be affected
Wall Height and Load Considerations
Professional engineering is typically required for:
- Walls over four feet in height
- Walls supporting significant loads (e. g. , driveways, buildings)
- Tiered wall systems
An engineer can design a retaining wall that safely manages the increased pressure and load-bearing requirements in these situations.
Retaining Wall Legal and Safety Requirements
Many jurisdictions have specific regulations regarding retaining walls:
- Local building codes often require engineered plans for walls over a certain height
- Walls near property lines or public spaces may need additional approvals
- Certain materials or construction methods may require professional certification
Consulting an engineer ensures your project complies with all relevant laws and safety standards, potentially saving you from costly legal issues or reconstruction in the future.
Our Conclusion
Retaining walls are invaluable for managing landscapes, controlling erosion, and creating functional outdoor spaces. Whether achieved through DIY efforts or professional intervention, understanding the basics and intricacies of retaining wall construction is crucial for a successful project. Evaluate your needs, consider site-specific challenges, and choose appropriate materials and designs to build a retaining wall that will stand the test of time.