Net-Zero
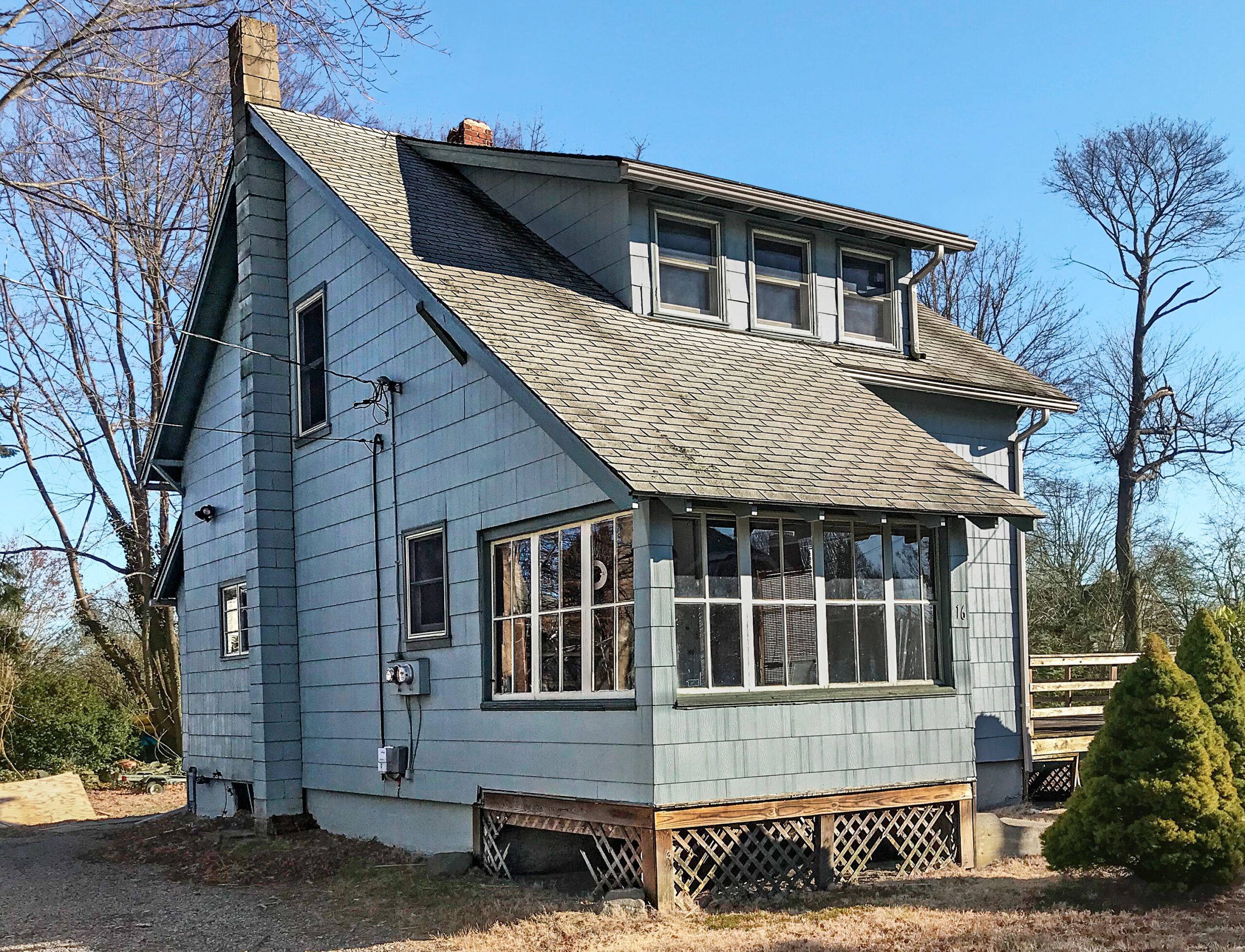
One summer Sunday, as they reluctantly prepared to corral their two boys and hit the road at the end of another weekend at the Jamestown, Rhode Island, beach house they shared with their extended family, Don and Dana Powers confronted the question: “Why don’t we live how we really want to live?”
Shown: All-new systems will enable the renovated house to use only as much energy as it produces.
Cutting Lumber
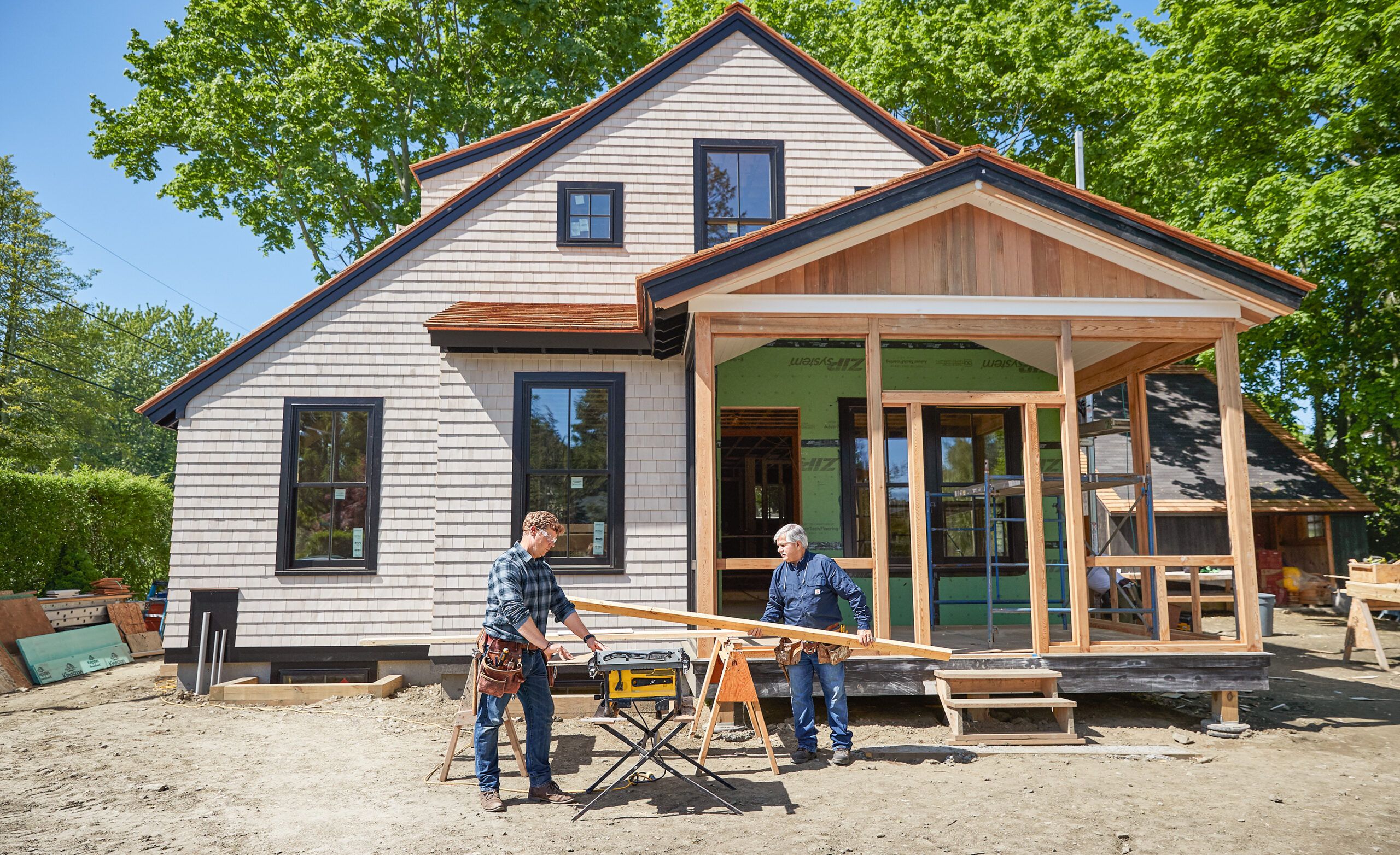
And with that they decided they would leave their house in Providence, where Don’s architectural office is located, and find a new home in the small island community across a toll bridge from Newport.
Shown: TOH general contractor Tom Silva and host Kevin O’Connor cut lumber for a screened porch that allows outdoor access from an addition that will double the size of the existing 1,000-square-foot cottage.
Homeowners
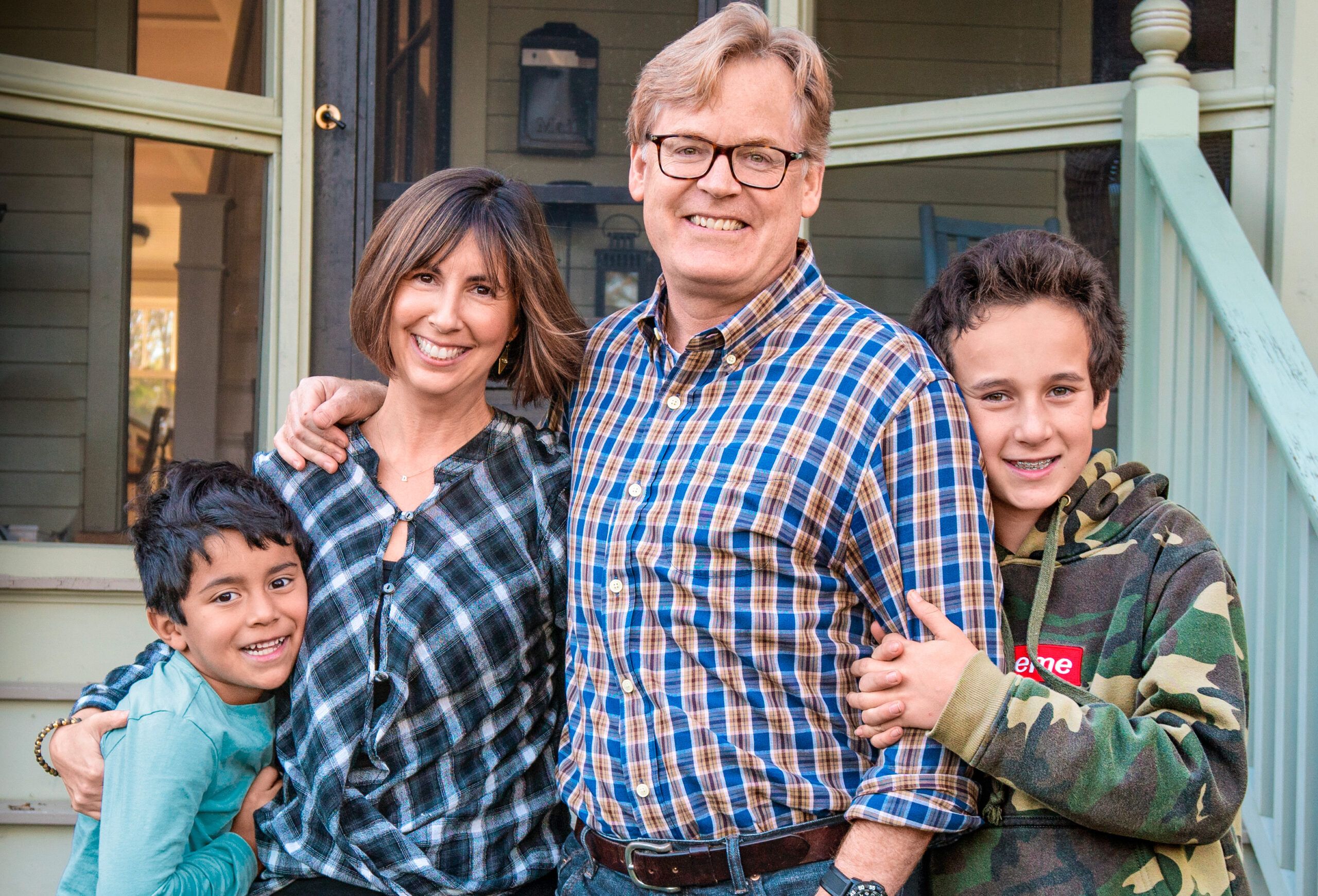
Thus began a two-and-a-half-year hunt that ended with an accepted offer on a 1,000-square-foot cottage, built in the 1920s, in need of extensive renovation—now being documented for the 40th season of This Old House TV.
Shown: Homeowners Dana and Donald Powers with their sons Theo, age 7, and Nate, 13.
Foundation Panels
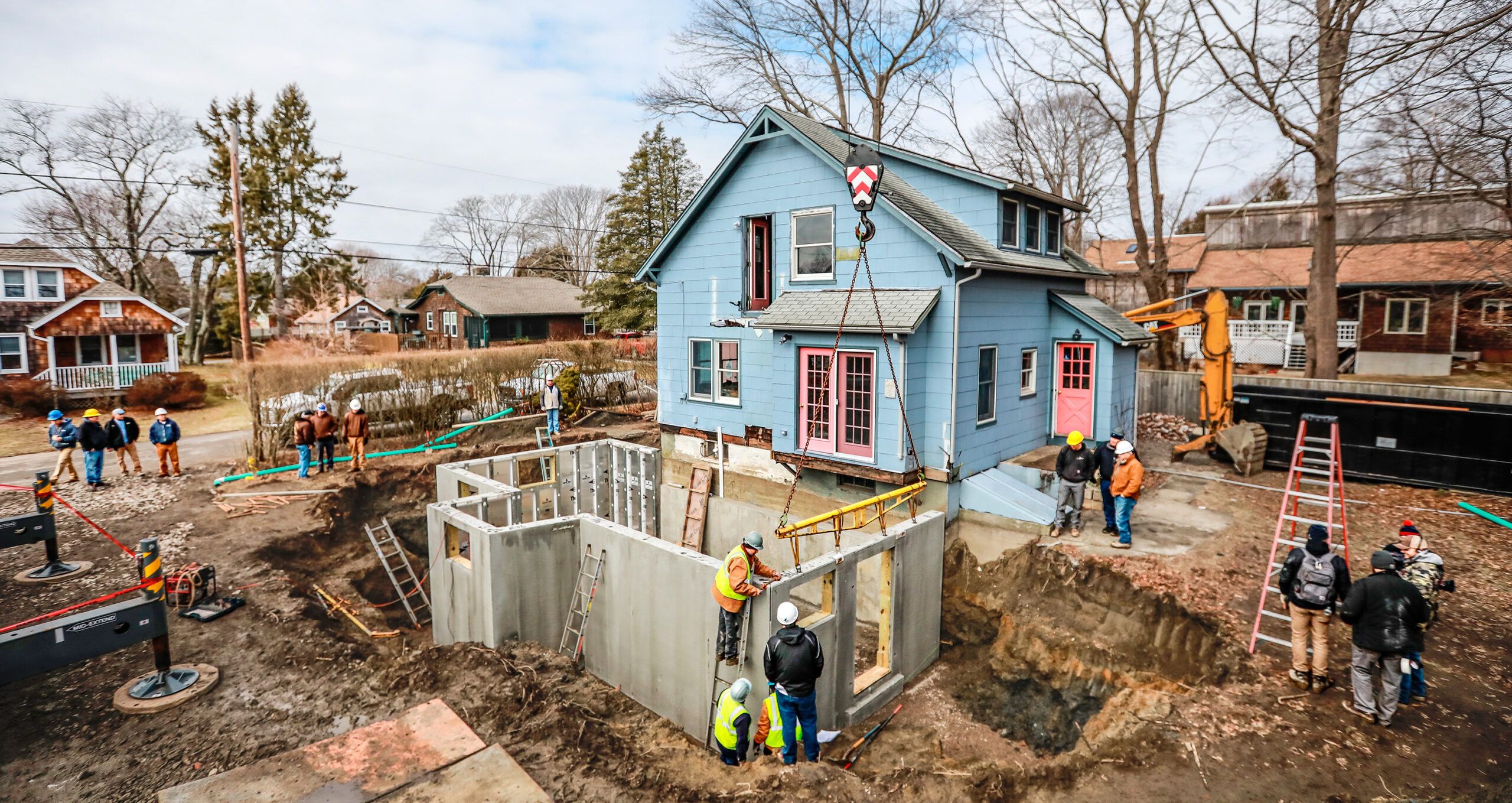
Don’s design goals for the house were multifaceted. First, he wanted to rework the floor plan and enlarge the house to accommodate their family of four. At the same time, he would keep the house recognizable as a Jamestown shingled cottage. “I didn’t want the house to be the sore thumb of the neighborhood, with a big bulky addition. And I wanted to add some architectural flair.”
Shown: The addition’s factory-made concrete foundation panels are insulated with foam and backed with steel studs.
Unloaded Panel
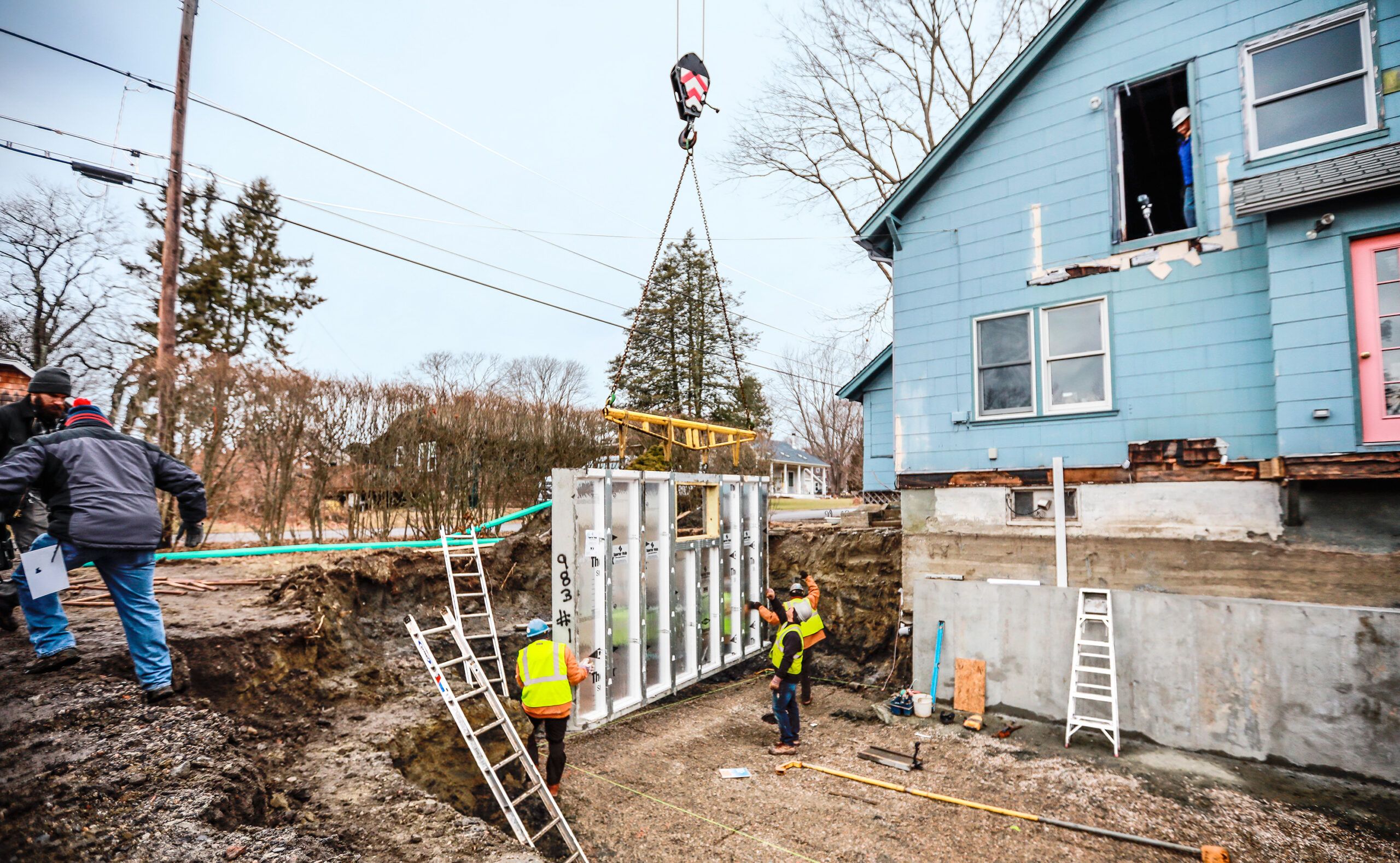
Just as important was energy efficiency, something Don knows a lot about from his work designing sustainable-community projects. The couple decided to build a net-zero home—a building standard that dictates that a house use only as much energy as it can produce. In the Powers house, photovoltaic solar panels and a heat-recovery HVAC system will supply the needed energy, while layers of insulation, Energy Star appliances, triple-glazed argon-filled windows, and LED lighting will keep energy use low.
Shown: A crane unloads the panels, then lifts them into place on compacted gravel subfootings where they are bolted together.
Foundation walls and installation: Superior Walls
Foundation Height
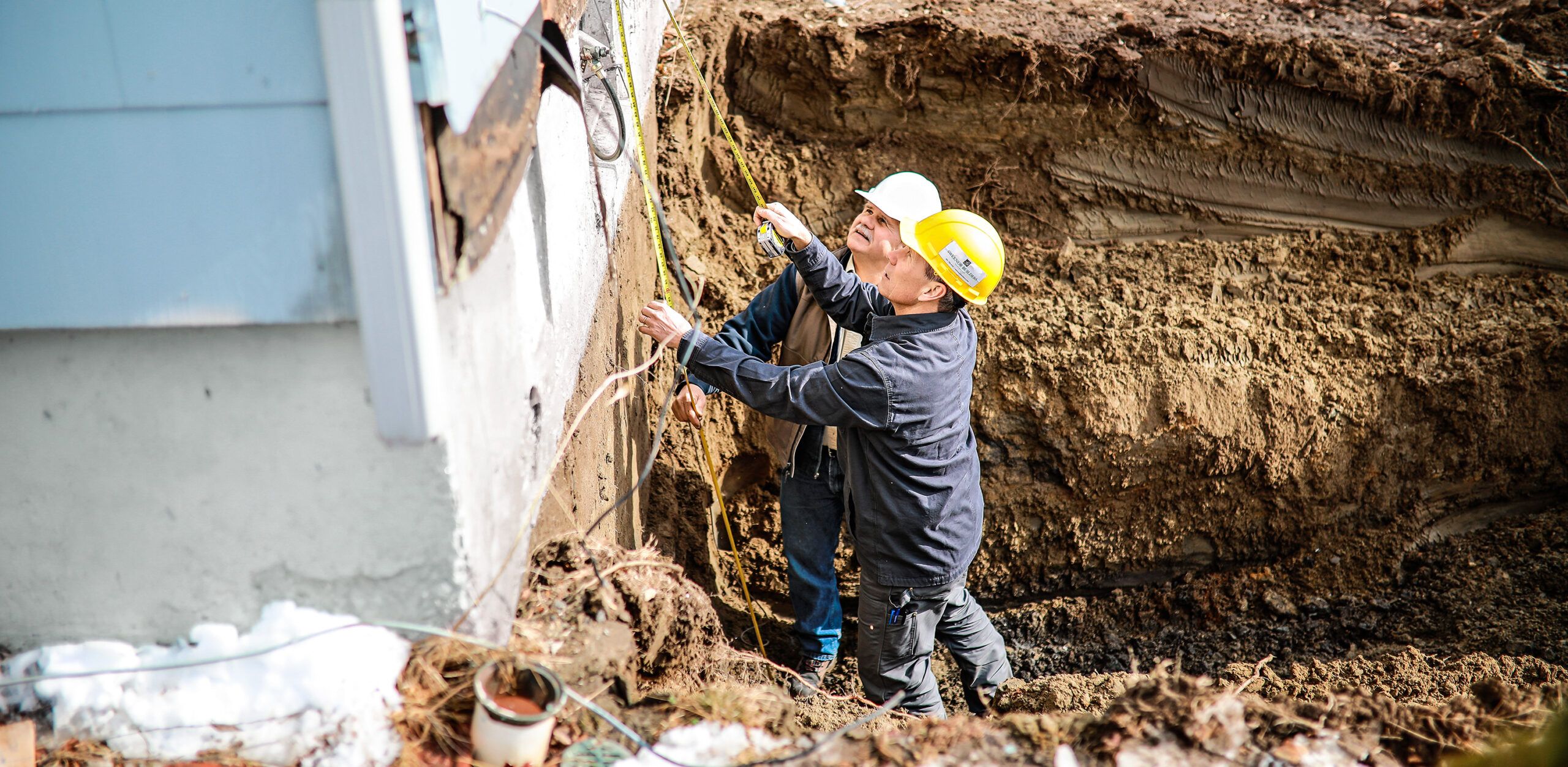
The couple have a realistic outlook about living in the finished house. “Many folks in the net-zero world feel that any energy use more than absolutely necessary is almost morally wrong,” Don says. “We’ll be responsible energy users, but we’re not going to live like monks.”
Shown: Tom Silva and Jeff Sweenor, the builder on the Jamestown project, check the measurement for the step-down addition’s foundation height.
General contractor: Jeff Sweenor, Sweenor Builders
Cutting Rafter Tails
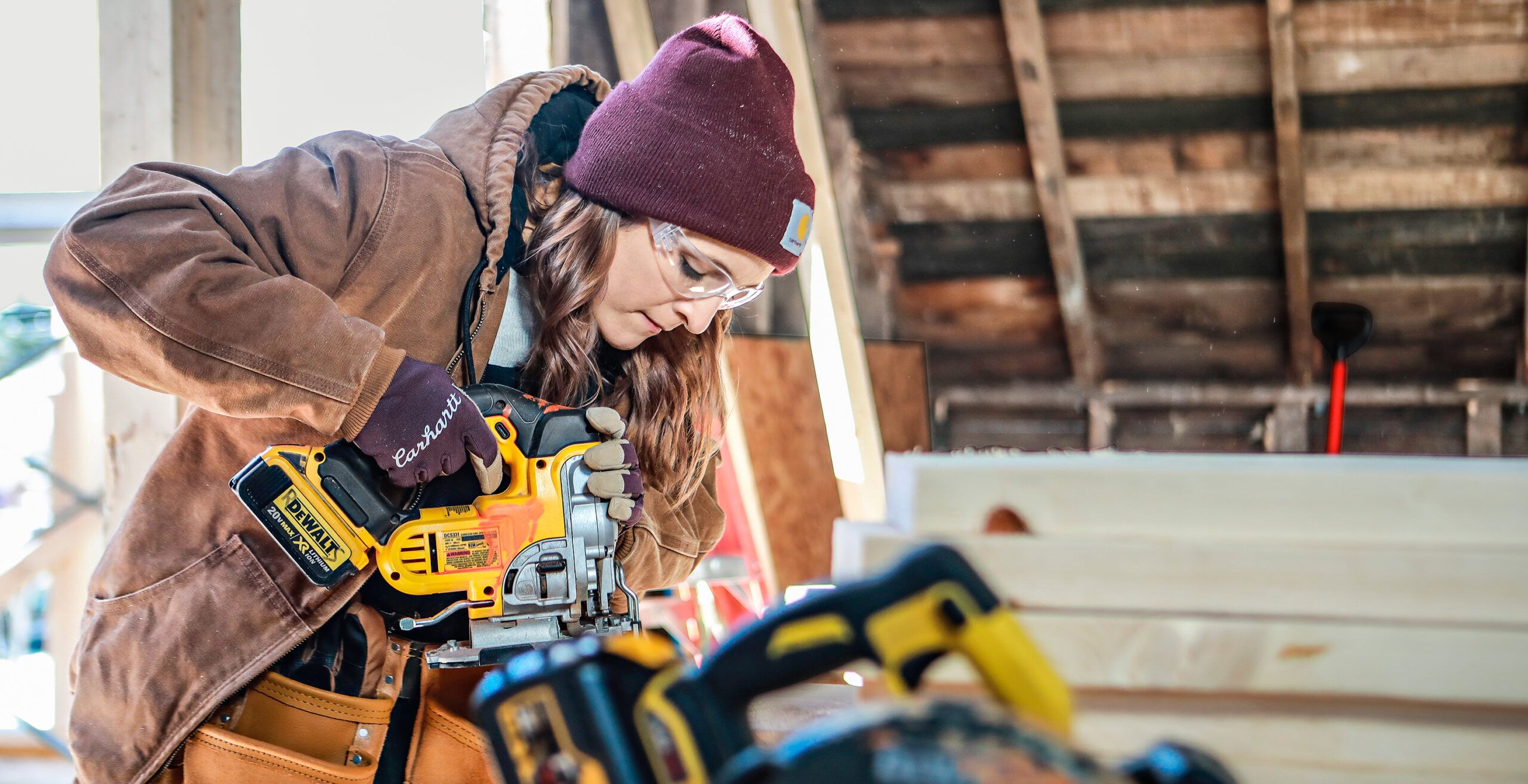
The renovated house will grow in length, but not in height or depth, with a two-story addition continuing the eave line of the original house to keep the low, cottage scale of the neighborhood. The original roof carries unbroken onto the new construction, where the size and placement of existing front and rear shed dormers are duplicated. But the addition is not a mirror image of the original house. It’s more of an artful extension.
Shown: Sweenor Builders’ apprentices at work. Mary McGuire Smith cuts rafter tails with a jigsaw
Jigsaw: DeWalt
Framing a Dormer
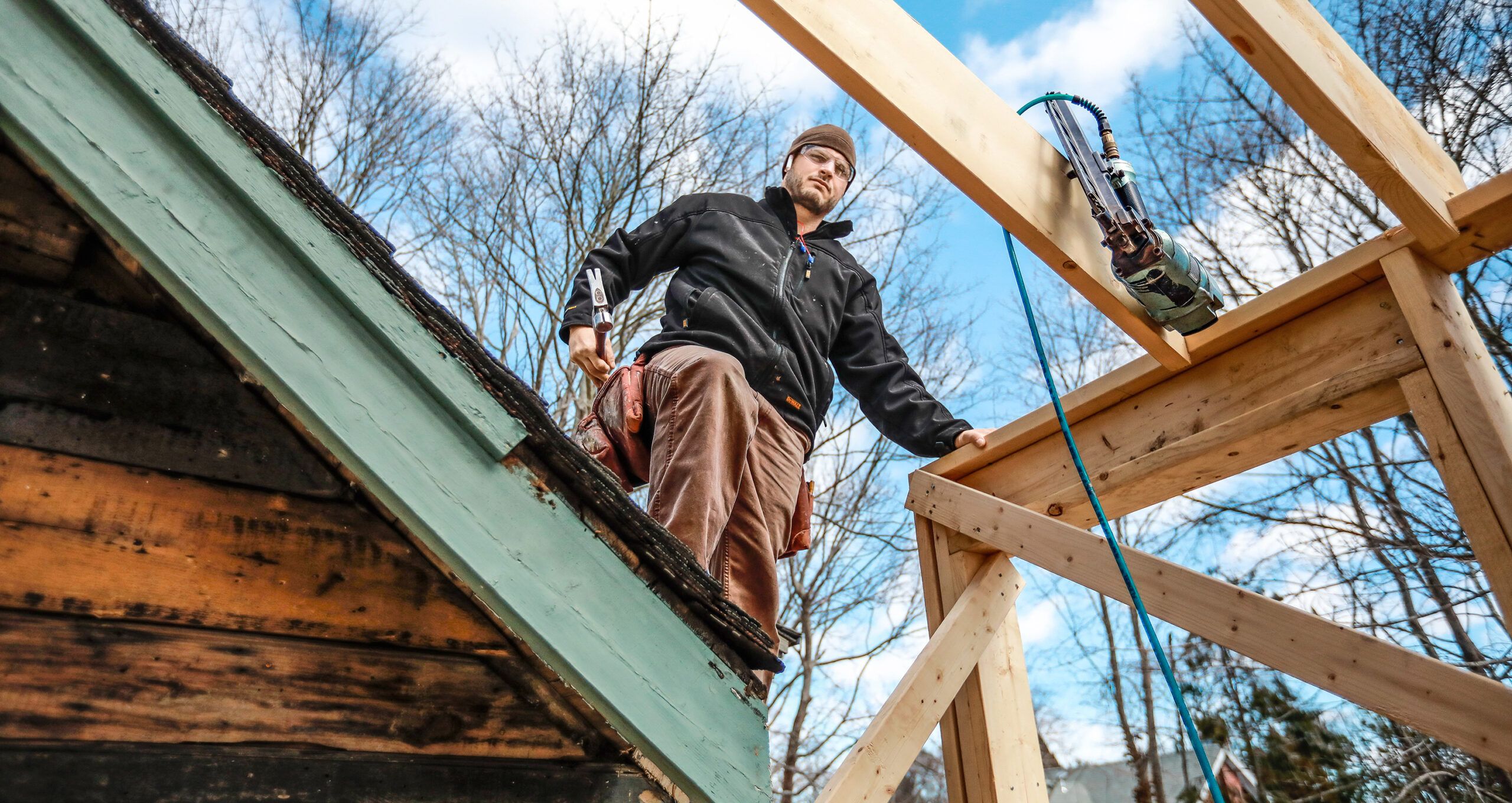
Inside, an 8-foot-wide opening will connect the kitchen and dining area to the adjacent living room. “We wanted most of the floor to be a big social space but with the intimacy of individual rooms,” Don says. In the living room, there’s a three-sided “music nook” for their son Nate’s baby grand piano. A den is tucked into a front corner of the house with a door separating it from the common areas. Upstairs, there will be bedrooms for each of their sons, a shared bath, and, down a short bookshelf-lined hall, a master suite.
Shown: Some more Sweenor Builders’ at work: Kevin Barker helps frame a dormer.
Wall Wrap
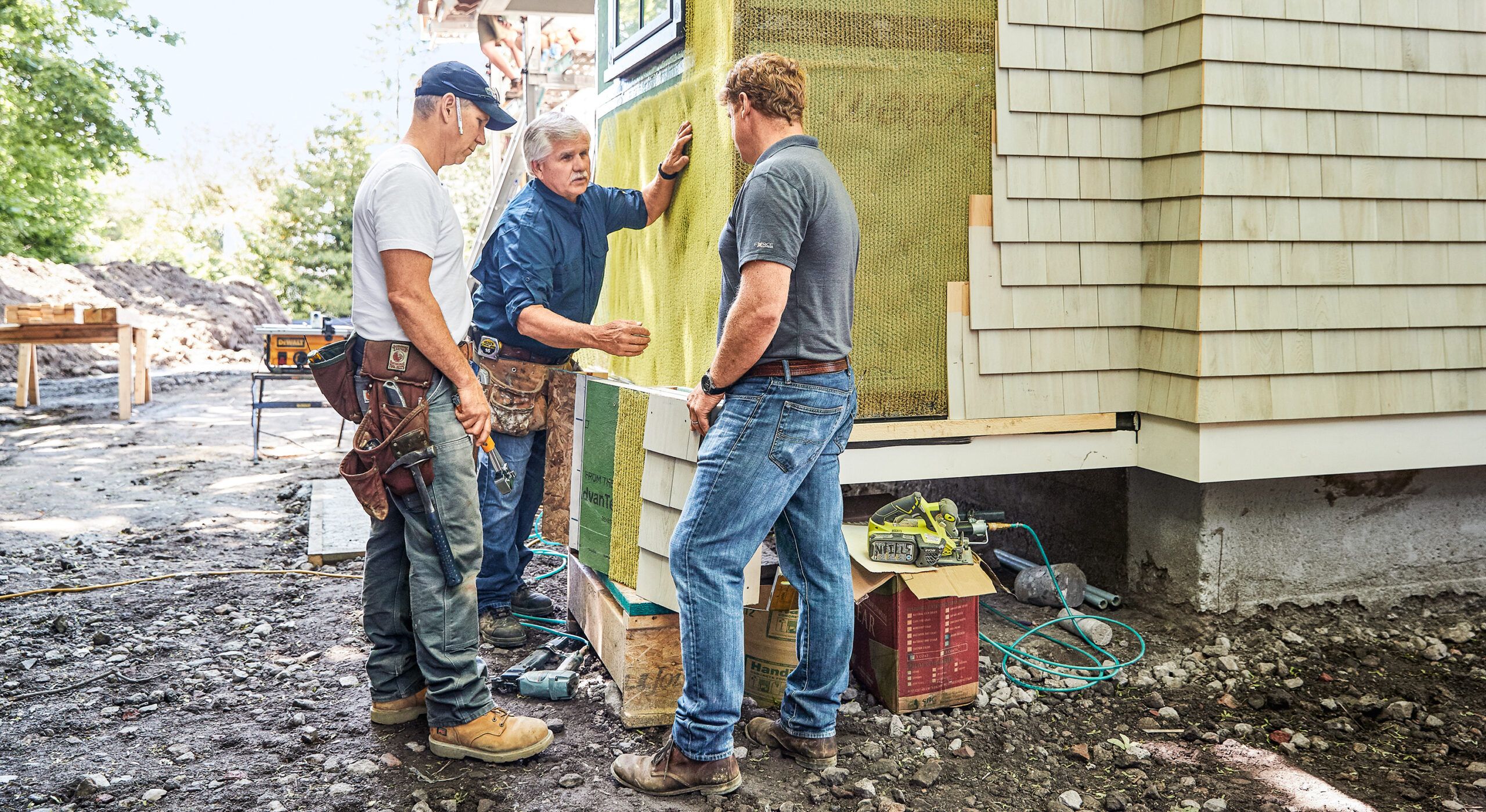
The addition’s screened porch steps down to the yard. “Being outside is a big part of how we live here,” Don says. “It’s a Jamestown thing to hang around the fire pit at night,” Dana adds.
Behind the house is a post-and-beam barn. Purchased as a kit and assembled on-site, the multiuse building has one garage bay and a small shop downstairs. “I’ll finally have a place to use my father’s woodworking tools,” says Don. Upstairs is open space for an office/art room and a guest suite.
Shown: Tom Silva and Kevin O’Connor discuss a vinyl-mesh wall wrap with builder Jeff Sweenor. The mesh helps the white cedar shingles dry from the back side, increasing their life span and keeping moisture out of the house.
Wall wrap: Home Slicker
Architectural Rendering
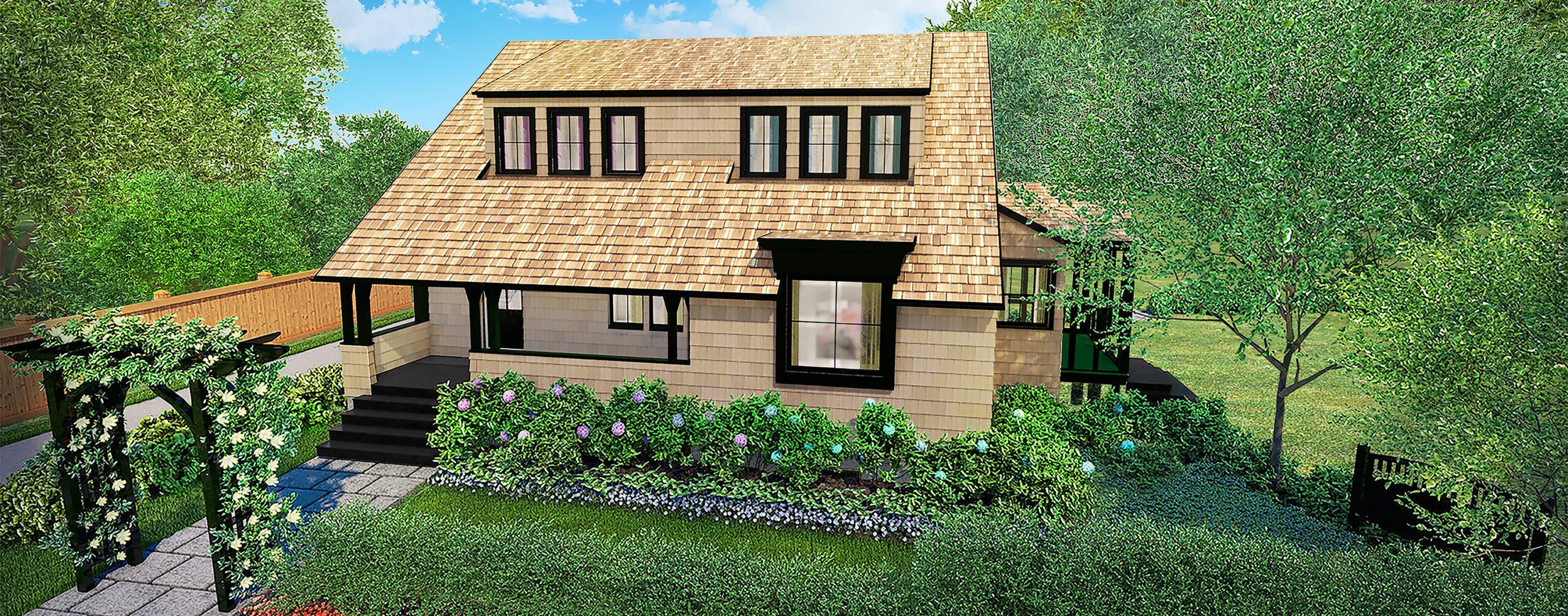
One step in achieving net zero is to ensure the building will use as little energy as possible, so the first challenge was to tighten up the existing structure as well as insulate the new addition. The house’s existing foundation and slab were lined with a combination of rigid mineral-wood panels and rigid foam panels. Instead of a typical poured-concrete foundation, the addition’s basement walls were factory-built insulated, reinforced concrete panels installed on-site. Above the basement, the stud walls are filled with spray foam, with rigid foam applied to the exterior on top of a vapor barrier.
Shown: A computer rendering shows how the finished house, with double the living space of the original cottage, will retain its neighborly scale.
Architect: Don Powers, Union Studio Architecture & Community Design
Coastal Hallmarks
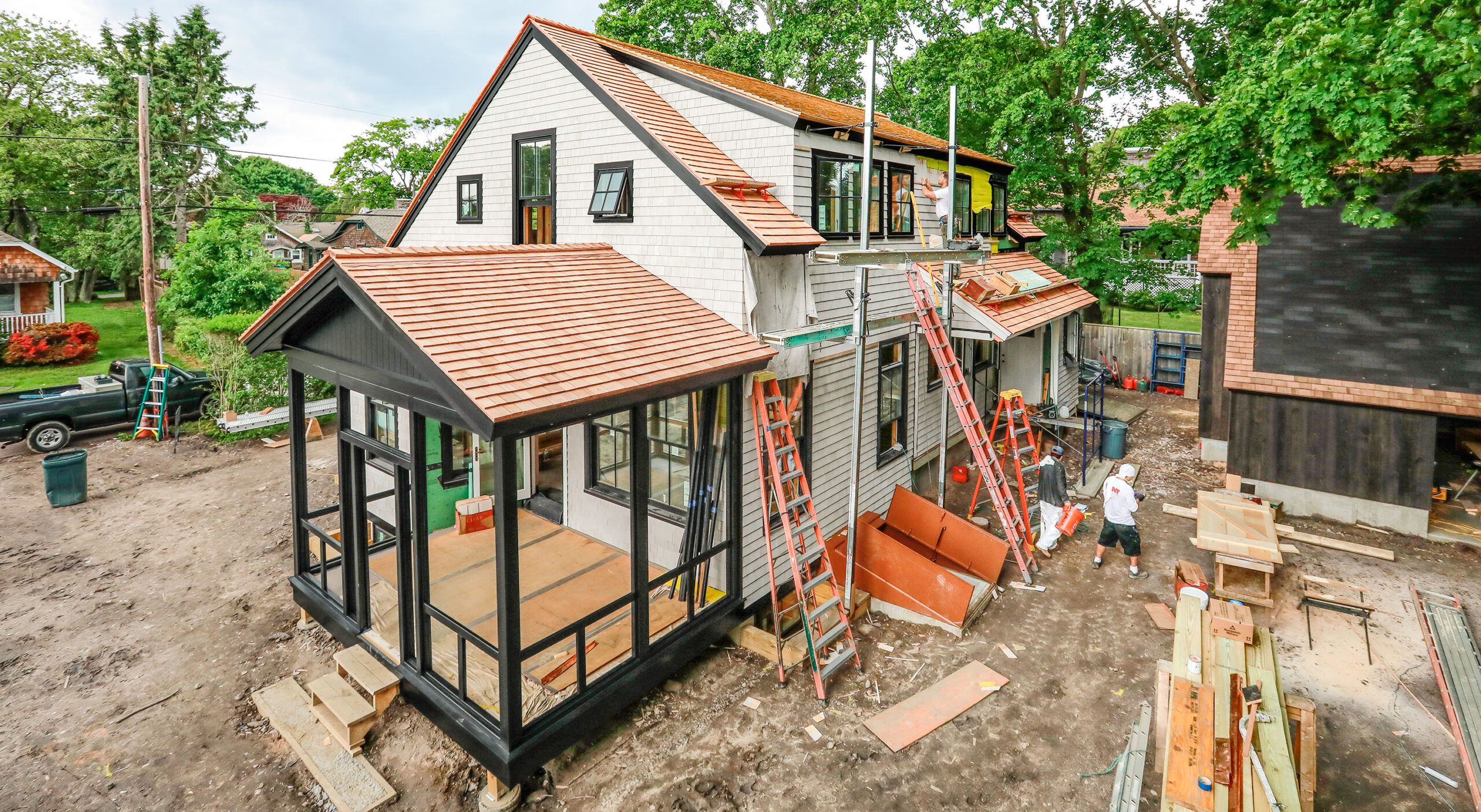
The underside of the existing roof was also insulated with closed-cell spray foam; then a matrix of 2x6s and OSB sheathing filled with one 2-inch layer and one 3-inch layer of staggered rigid mineral-wool board was installed on top of the new and old rafter systems. “Basically, they built structural insulated panels [SIPs] on-site,” says This Old House general contractor Tom Silva. “This saved time and money.”
Shown: Red cedar roof shingles and white cedar sidewall shingles with woven corners (meaning no corner boards) are hallmarks of coastal New England cottages. Unadorned, flat exterior trim on rake boards, windows, and doors completes the look.
White cedar shingle siding: SBC
Red cedar roof: Liberty Cedar
Roof Underlayment: Cedar Breather
Windows: Marvin
Solar panels: Vivint Solar
HVAC system: LG Air Conditioning Technologies
Ventilation system: RenewAire and Panasonic
HVAC installation: Restivo’s
Barn Construction
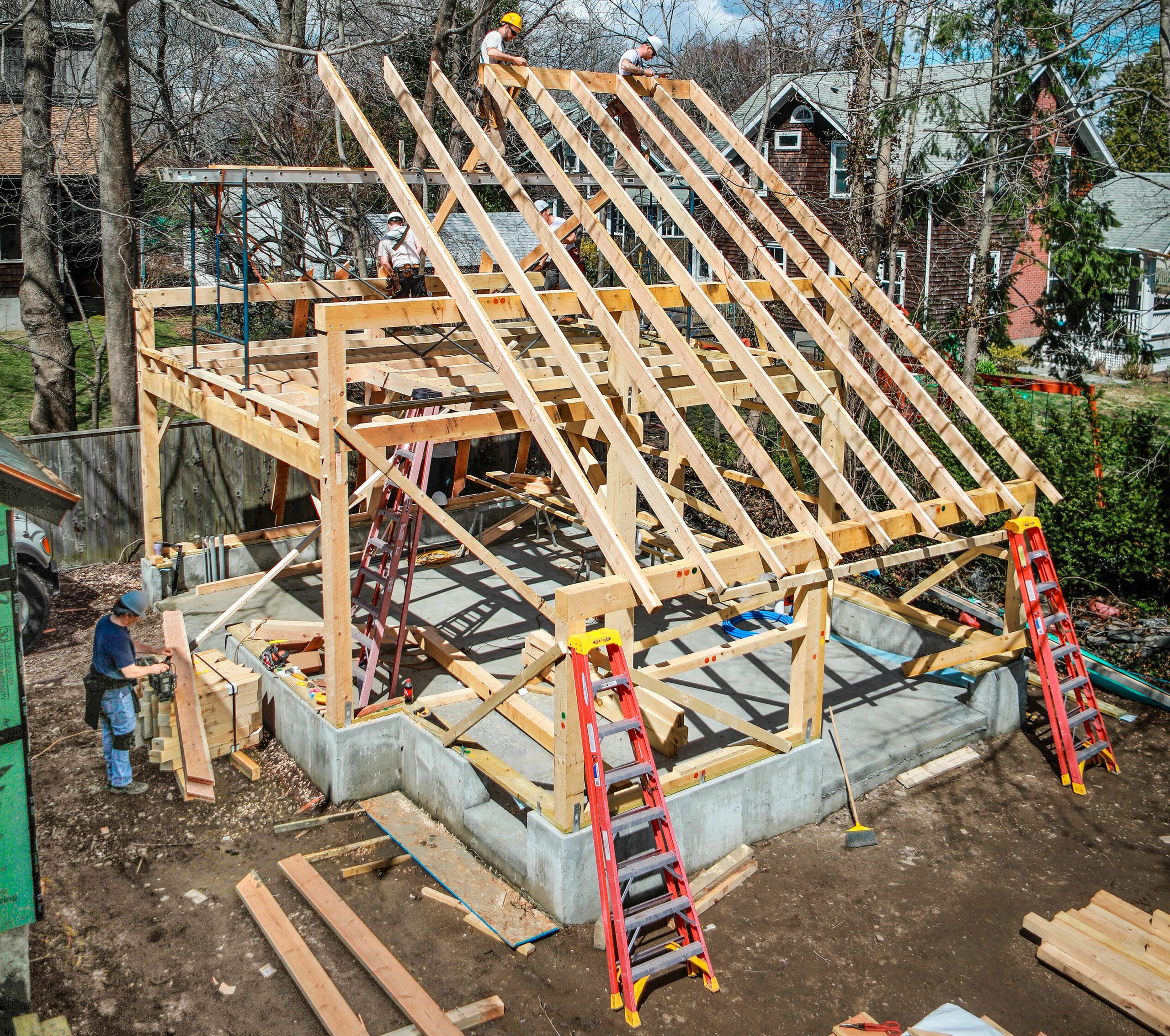
Though Sweenor Builders, the crew on the project, goes out of its way to build a tight house, all houses have air leaks. A blower door test on the Powers home showed 4 air changes per hour (ACH), considered to be tight. But a new air-sealing technology, first developed for HVAC ducts, reduced the house’s ACH to less than 1, all in about 60 minutes.
Here’s how it works: Lengths of tubing with spray-nozzle tips are set up inside the house on small tripods—several on each floor. Then, while a blower door pressurizes the house, a compressor pushes an acrylic-glue-like substance through the tubing and out the nozzles. The atomized gluey mist travels toward any air leaks, where it begins to collect around the holes. Glue particles stick to other glue particles, eventually clogging the opening. “This technology is a game changer,” says TOH plumbing and heating expert Richard Trethewey. “It’s a faster and better way to air seal any building, old or new.”
Shown: The post-and-beam barn arrived on-site in kit form. Cutting the barn frame at a factory, rather than on-site, saved time and money. After assembling the frame, the crew cut, then installed, the 2×12 rafters.
Barn: Country Carpenters
Outdated Decks
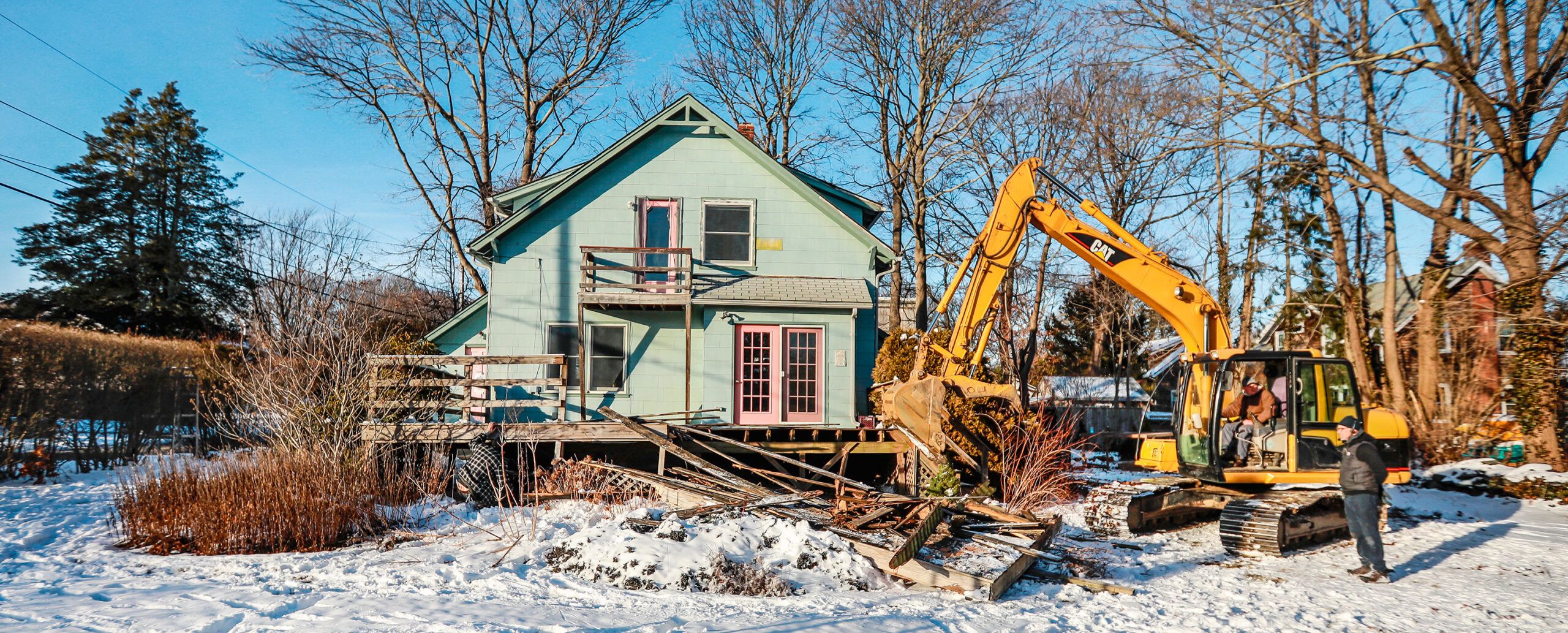
Photovoltaic panels on the southern slope of the barn’s cedar roof will generate all the electricity used by the Powers family. An innovative heat-recovery system that monitors five zones in the buildings, and can actually move heat from one area to another, will provide ultra-efficient HVAC. It will also heat water for the faucets. An energy-recovery ventilation system will provide fresh air for the house but will harvest heat from the air before exhausting it outdoors.
Shown: The classic lines of a New England cottage hid behind a series of outdated decks, leaky doors and windows, and asbestos-laden siding.
Entry Porch
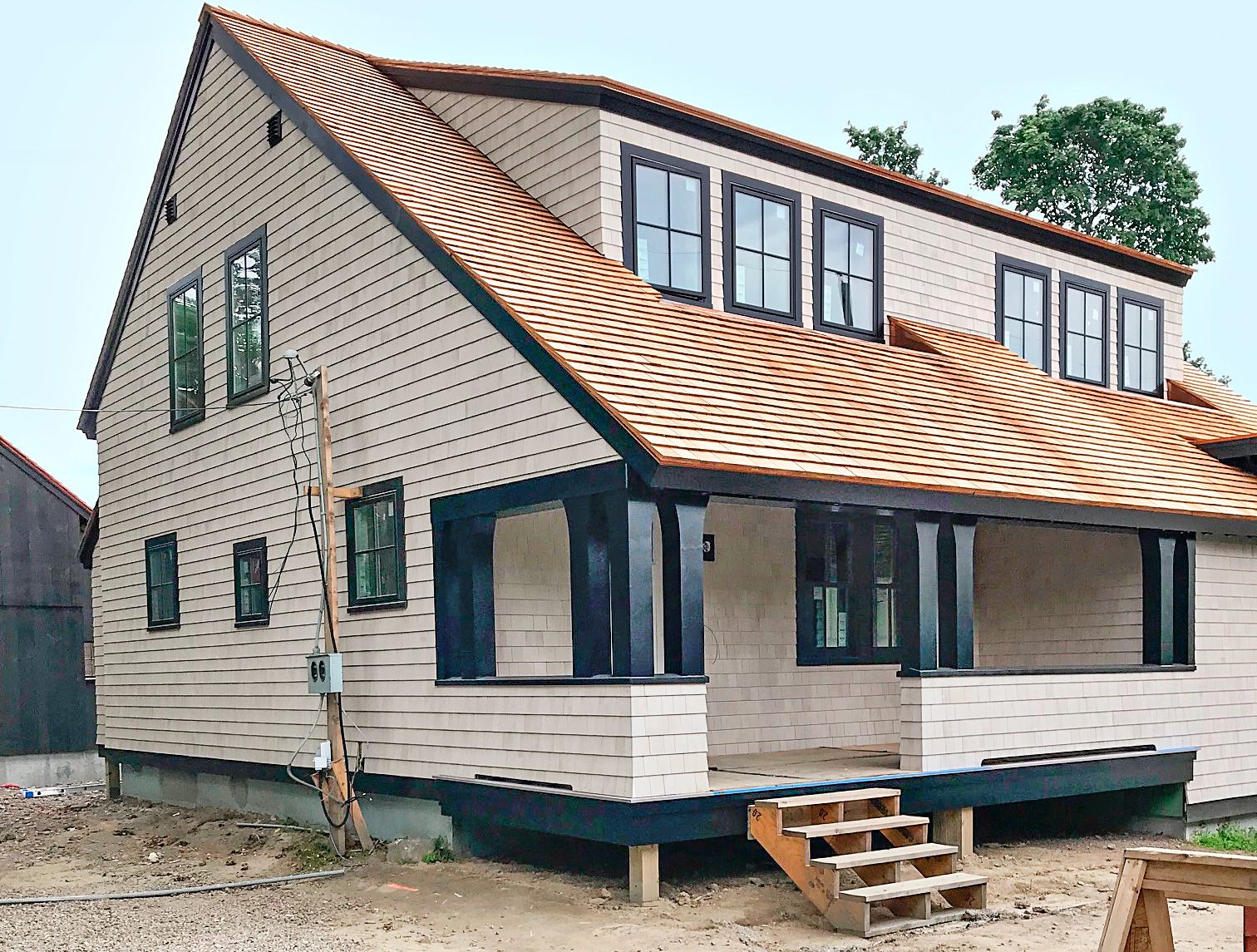
Moving to Jamestown will mean lots of lifestyle changes for the Powers family. They will be living outside the city in a small, close-knit community near the ocean. The house is two-thirds the size of their previous home. Net zero means increased attention to electricity use and heating and cooling demands. “But the way we look at it, a net-zero house will enhance our life, not dictate it,” says Don. Adds Dana, “It’s all part of living the way we want to live.”
Shown: The original roof plane caps the now opened-up entry porch, and the lines of the original dormer continue onto the addition.