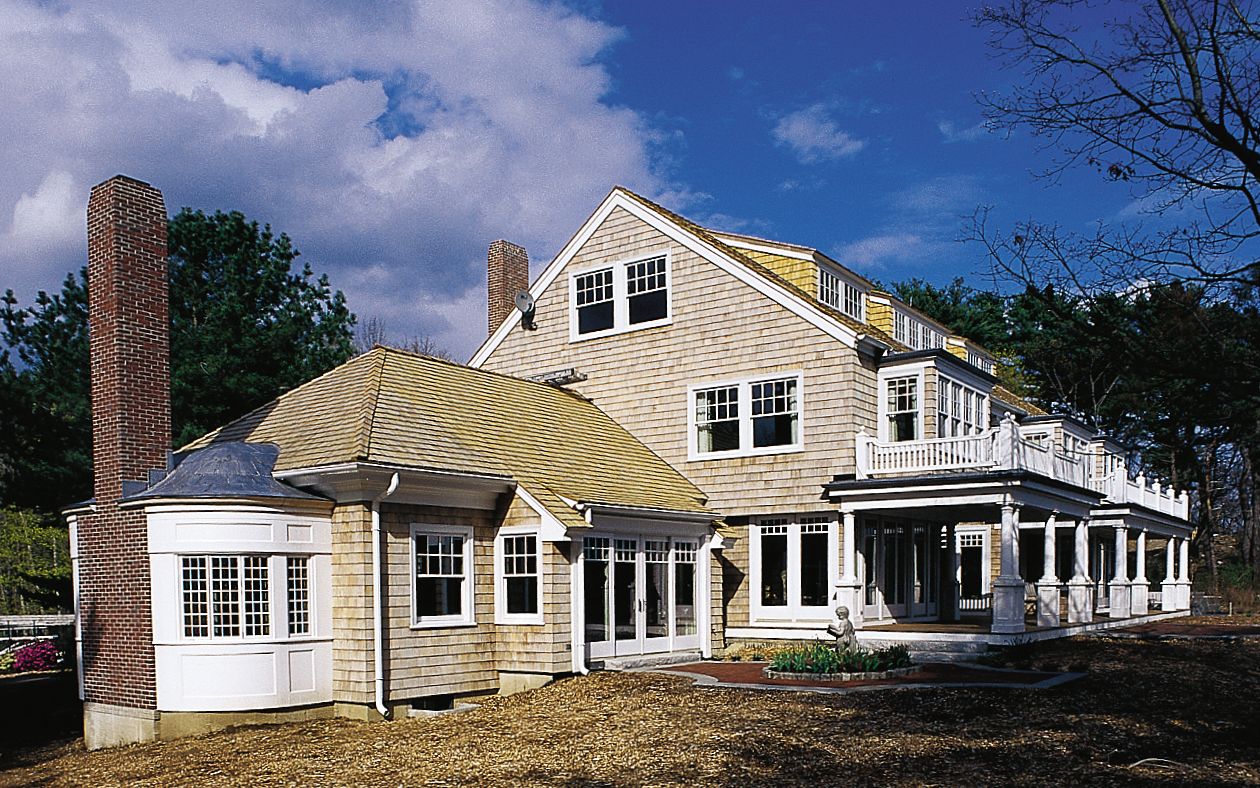
One of the challenges of winter construction, at least here in brutal
New England, is temporary heat.
How do you give the workers some relief from the cold while parts of the building have no windows? How do you heat the building without choking the workers with oil or gas fumes?
Historically, the choice has been a “torpedo heater.” These portable
heaters are on wheels and look like their name suggests, ½, a
torpedo. They fire with either kerosene, propane or natural gas and can be moved to the location needed for spot-relief from the cold.
The problems have been the noise, smell and fumes the units produce. A kerosene unit will choke practically anyone in its path and leave a residue that is bad for plaster or painted surfaces.
The gas units put high levels of moisture in the building and the fumes are not so great either. With these unvented units, the high levels of carbon monoxide in their exhaust can cause headaches, nausea and, over extended periods, even death.
What we did at the Manchester, Massachusetts, project was to create temporary heat by using new high-efficiency, oil-fired heating boiler, and throughout the building we placed air handlers.
These file-cabinet-sized units have a hot-water heating coil and a blower fan inside them. When air is blown across the hot-water coil (much like in an automobile radiator), air is heated.
The main challenge for any temporary heat has always been portability and ease of installation. What made this method possible was a super-tough flexible plastic tubing called cross-linked polyethylene (PEX).
After the boiler was installed, a circulator pump was installed at the boiler. Large-sized PEX piping was run upstairs to a centrally located supply and return manifold. This station, much like a station for air tools running on compressed air, supplied heat to the air handlers.
Smaller PEX were run from the manifold to the air handlers. On the manifold were quick-connect fittings used in the hydraulic industry.
These fittings allowed for disconnecting the lines without draining the piping every time. Want some heat in the living room? Just snap on a pair of smaller PEX lines, run them through the job site like extension cords, and plug in the air handler.
As parts of the house’s radiant heating system were installed and came on line, we simply added that piping off of our already fired boiler and stopped using temporary heat in that area, allowing us to phase in the
heating of the building.
One caution we must take is to protect the quality of the air that is burned in our heating boiler during construction. It is important not to clog the boiler or burner with foreign matter. The other air-quality issue is to provide filters at the air handlers so that the heating coils don’t get clogged with construction sawdust or sanding from sheet rock or plaster.
I saw this temporary heat solution done on a recent high-end remodel in Brookline, Massachusetts, and I was impressed with the working
conditions it led to. The general contractor didn’t have to scream to be
heard over the heater noise, there were no fights about whether the heat was on or off. You could actually hear all seven radios tuned to different stations.
This method for temporary heat also made sense for us in Manchester
because we were using water as the heating medium. We were not using a series of forced-hot-air furnaces throughout the building and separate
water heaters. The integrated approach on this building was to have one boiler and burner that would be load-managed to do all functions in the building. The boiler will make hot water for faucets through an indirect water heater. This water heater ½ a super-insulated thermos bottle
with no burner in it ½ has a coil that boiler water can pass through to heat up for washing and cooking.
The heating plan for this building also calls for radiant floor heating
throughout the first floor and bathrooms. Flat panel radiators with
their own thermostatic valves will heat the bedrooms. The top floor will
have hydro-air using a mini-duct hydro-air system. The concept of
hydro-air means that heated water is sent through a coil to heat the air. That means in turn that the same ductwork used for cooling will also work for heating. And the last thing we will do with the system is to use a heat exchanger to run the snow-melting system at the front
steps, thus keeping the antifreeze separate from the boiler water.
And how much did all this cost? Well, the boiler had to be installed anyway. The PEX and the time to install it were relatively cheap. I found some scratched and dented air handlers at a friendly heating wholesaler and got them for $250 apiece. They can be used again and again.
And the value of not having to breathe kerosene fumes? Priceless.
Richard Trethewey is the plumbing and heating consultant for This Old House.