Norm’s Ready to Help You Step Up Your DIY Game
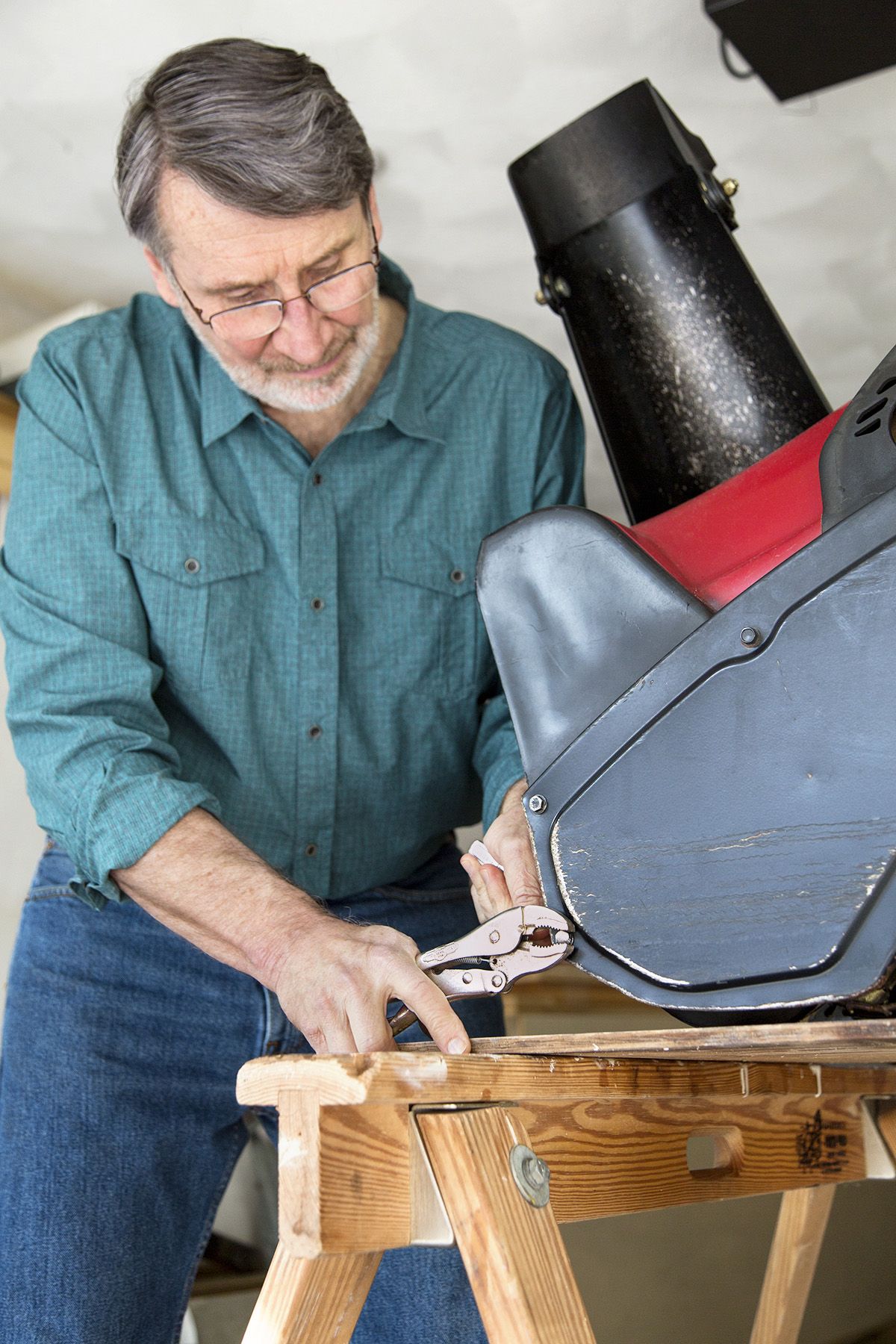
Like any master carpenter, Norm Abram has learned by doing. And doing and doing and doing. He began practicing his craft by his father’s side, remodeling and building custom homes, and he’s continued to learn new skills throughout his life.
Clearly, Norm has developed some sure-fire ways to make things work, and he’s always happy to share his knowledge. Here’s the latest collection of the TOH series, Norm’s Tricks of the Trade. In it, Norm offers advice on such DIY jobs as filling a crack in a cabinet door, drilling into steel, and keeping nuts tight on a deck so they won’t loosen up. It’s almost like having Norm as your handy next-door neighbor—except that you can’t borrow his tools.
Straighten a Bowed Stud: Step 1
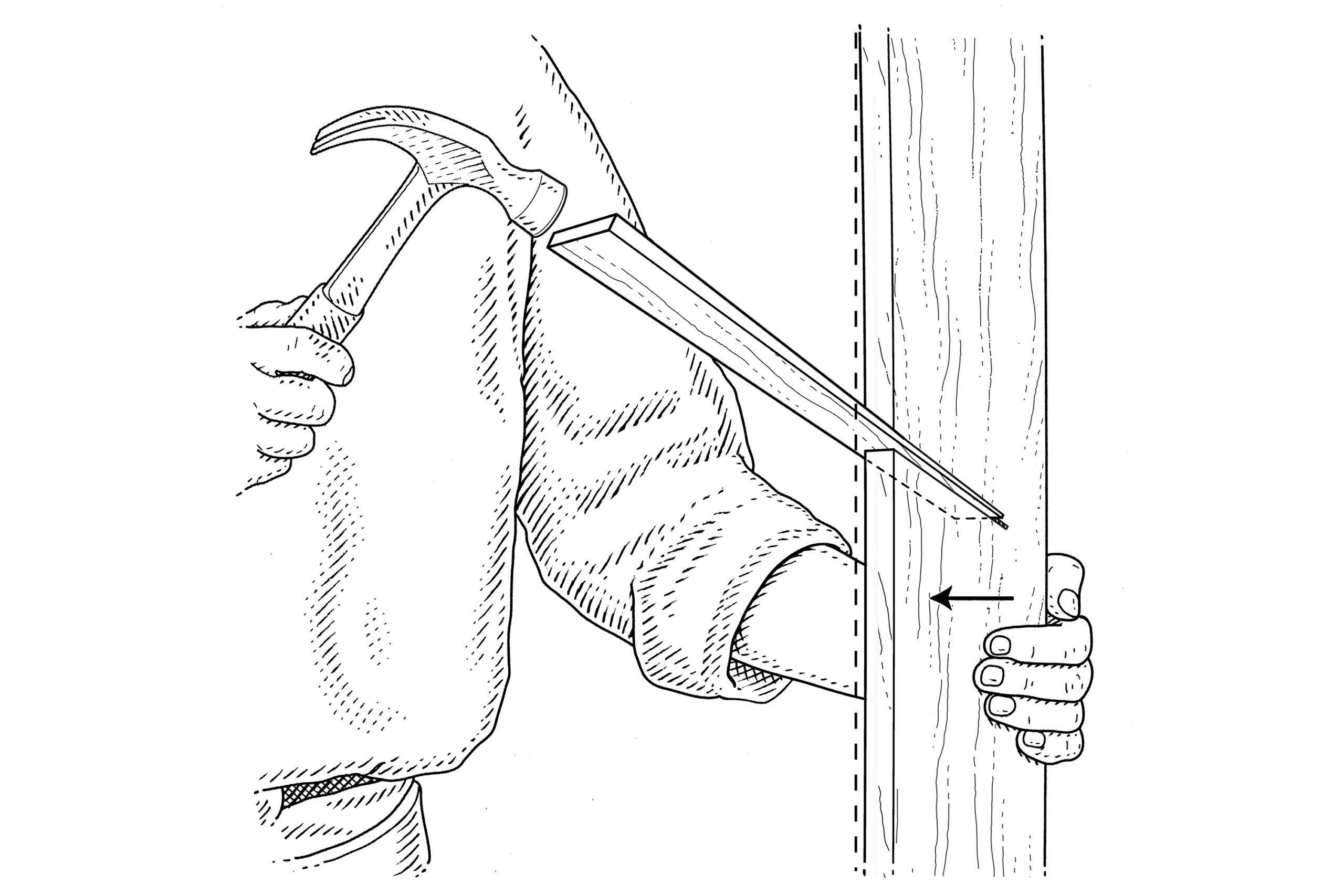
Q: Now that I’m finally getting around to building a partition wall, some of the studs I bought have bowed. Can I still use them or do I have to go buy more?
—Dellmar Yellock, Philadelphia
A: If the studs don’t have any other defects, go ahead and build the wall with the ones you’ve got. But before hanging the drywall, you should straighten any stud that bows in or out of the wall’s plane by more than 1/8 inch. Otherwise, that bow will leave an obvious hump or dip when the wall is finished. (Note: This fix works only with non-load-bearing walls. If the wall were load-bearing, you’d need to replace the bowed studs with straight ones.)
Cut into the edge. Halfway up from the floor, on the inside of the curve, make a 45° cut about three-quarters of the way through. Pull the stud until it’s straight, then tap a shingle into the open kerf, as shown. Use a utility knife to trim the shingle flush on the sides.
Straighten a Bowed Stud: Step 2
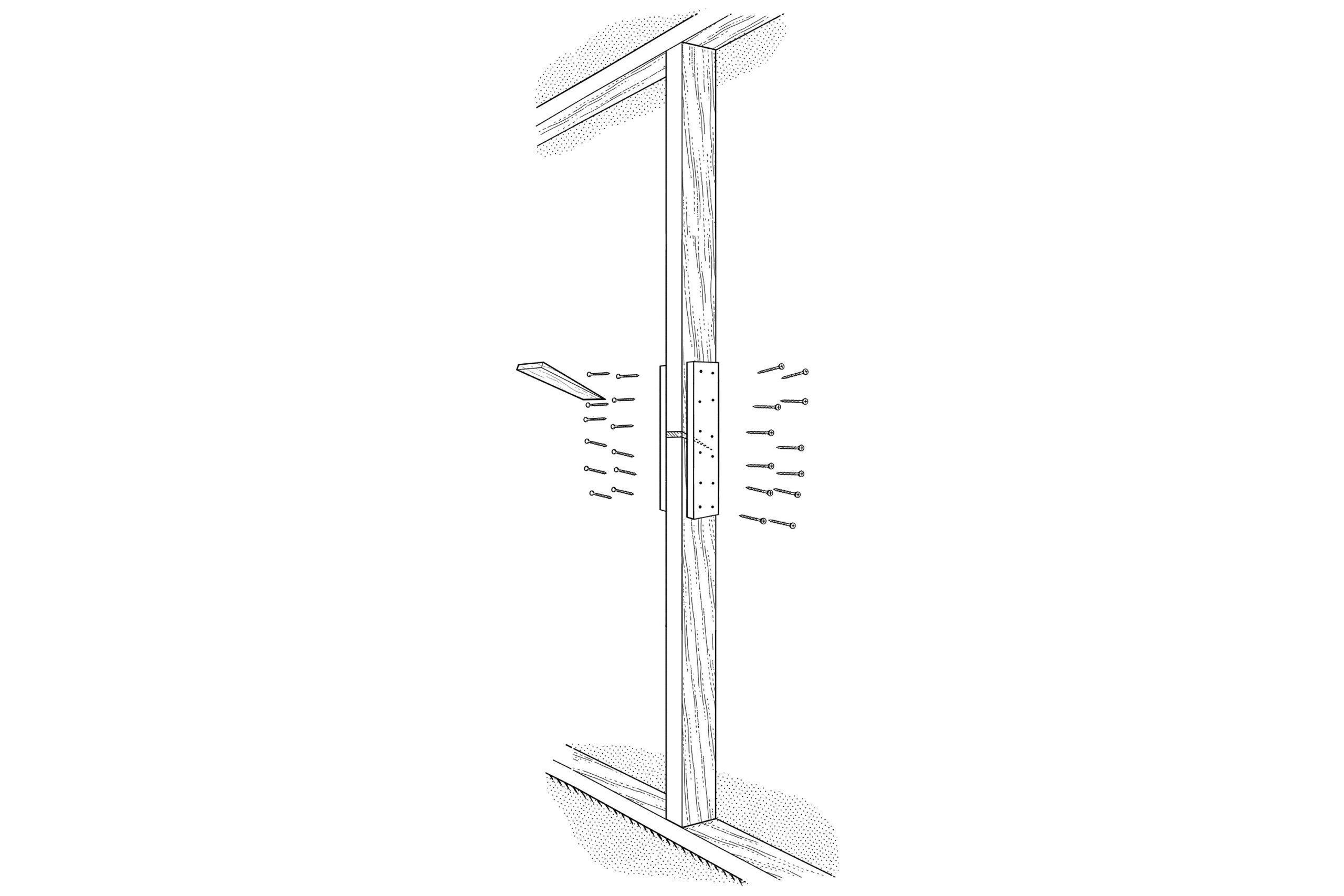
Reinforce the stud. Cut two 1⁄2-inch-plywood gussets about 24 inches long and 1⁄4 inch narrower than the stud’s width, so they won’t interfere with hanging the drywall. Apply construction adhesive to the gussets, and center each one—side to side and top to bottom—on a stud face, covering the cut. Then fasten each gusset with twelve 1 1⁄4-inch deck screws. Finally, score the shingle with a utility knife and snap it off flush with the stud’s edge.
Filling a Crack in a Wood Cabinet Door
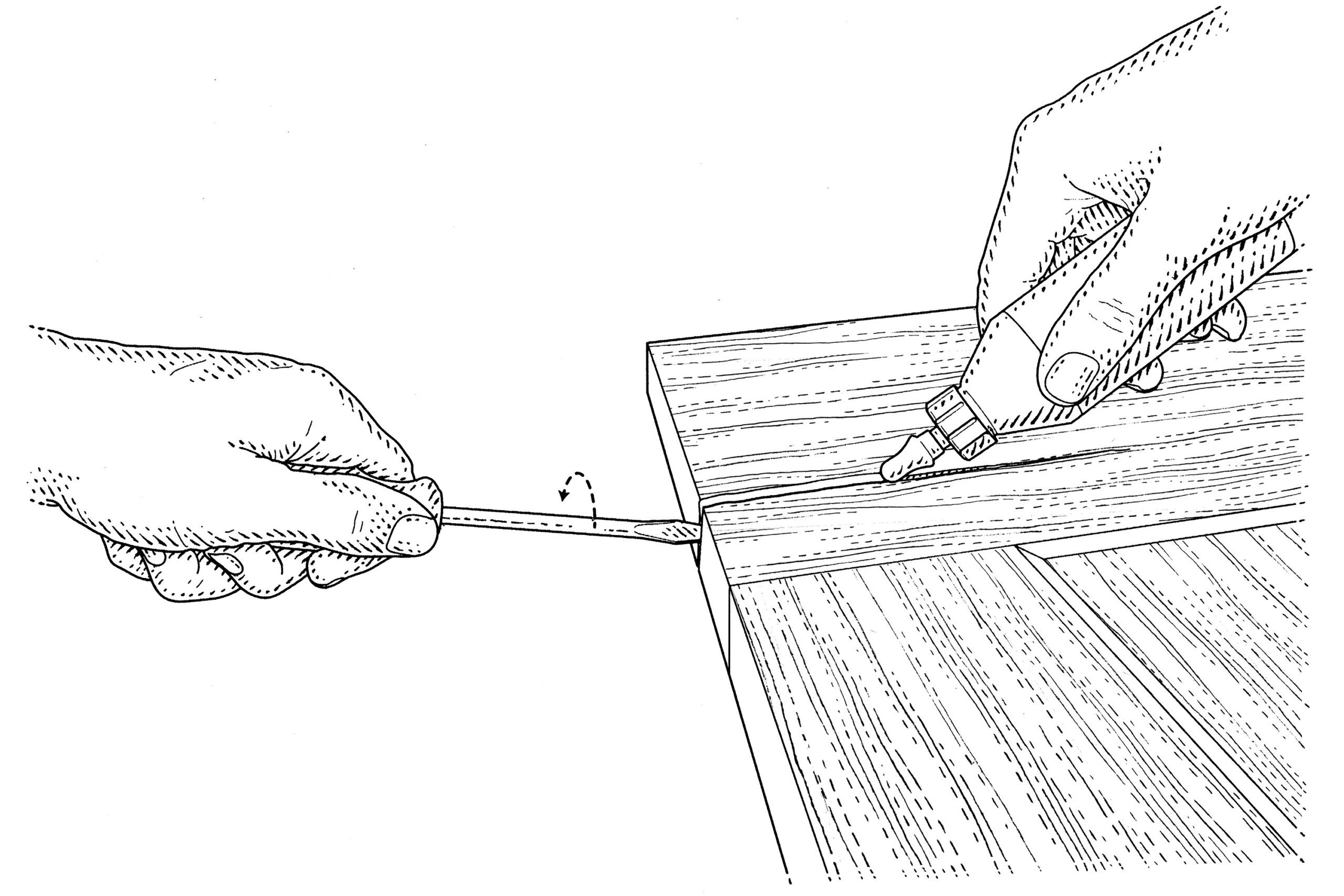
Q: The frame surrounding the panel on my wood cabinet door has developed a slight crack. What’s the best way to fix it?
—Robert Sawyer, Studio City, Calif.
A: A little glue should be able to fix that problem quite nicely. The problem is getting the glue far enough inside the crack so that it does some good. Here’s how to go about it.
First, remove the door and lay it on a flat surface protected against drips. Wedge a flathead screwdriver into one end of the crack and twist it slightly; that will widen the crack enough so you can squeeze in some wood glue. Be careful about how much you turn the screwdriver-—crank it too hard and you could make the crack much longer.
Apply the glue to both sides of the crack. If it doesn’t flow into the crack’s narrow end, use a toothpick to push it in.
When the gluing is done, pull out the screwdriver and close the crack with a clamp or two. Use a damp rag to wipe up any glue that squeezes out, before it dries. You can remove the clamps in about an hour, but wait 24 hours before rehanging the door.
Tighter Nuts
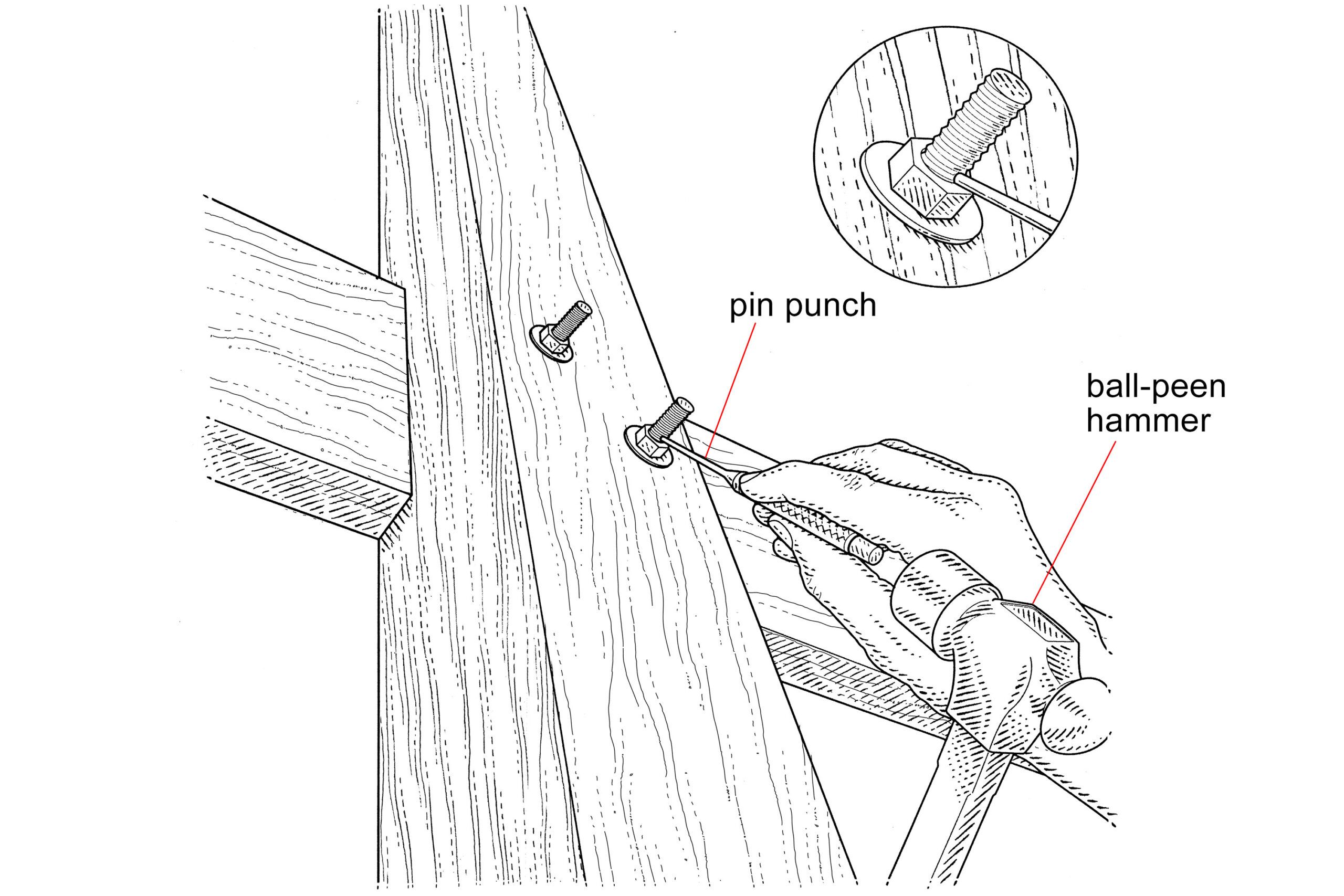
Q: How can I make sure that the nuts holding my deck framing together won’t work loose over time?
—Eric Barrow, Cos Cob, Conn.
A: There are at least four ways to keep exterior nuts tight. You can apply a thread-locking adhesive, tighten a second nut against the first one, or replace each nut with one that has a nylon insert, commonly called a nyloc nut. Or you can use the method my father taught me, which doesn’t cost a thing: Once the nut is tight, rest the tip of a pin punch on the bolt where it meets the nut, then give the punch a sharp tap. That deforms the threads enough to keep the nut from loosening, but doesn’t prevent it from being removed later.
Pitching Pipe for a Drywell
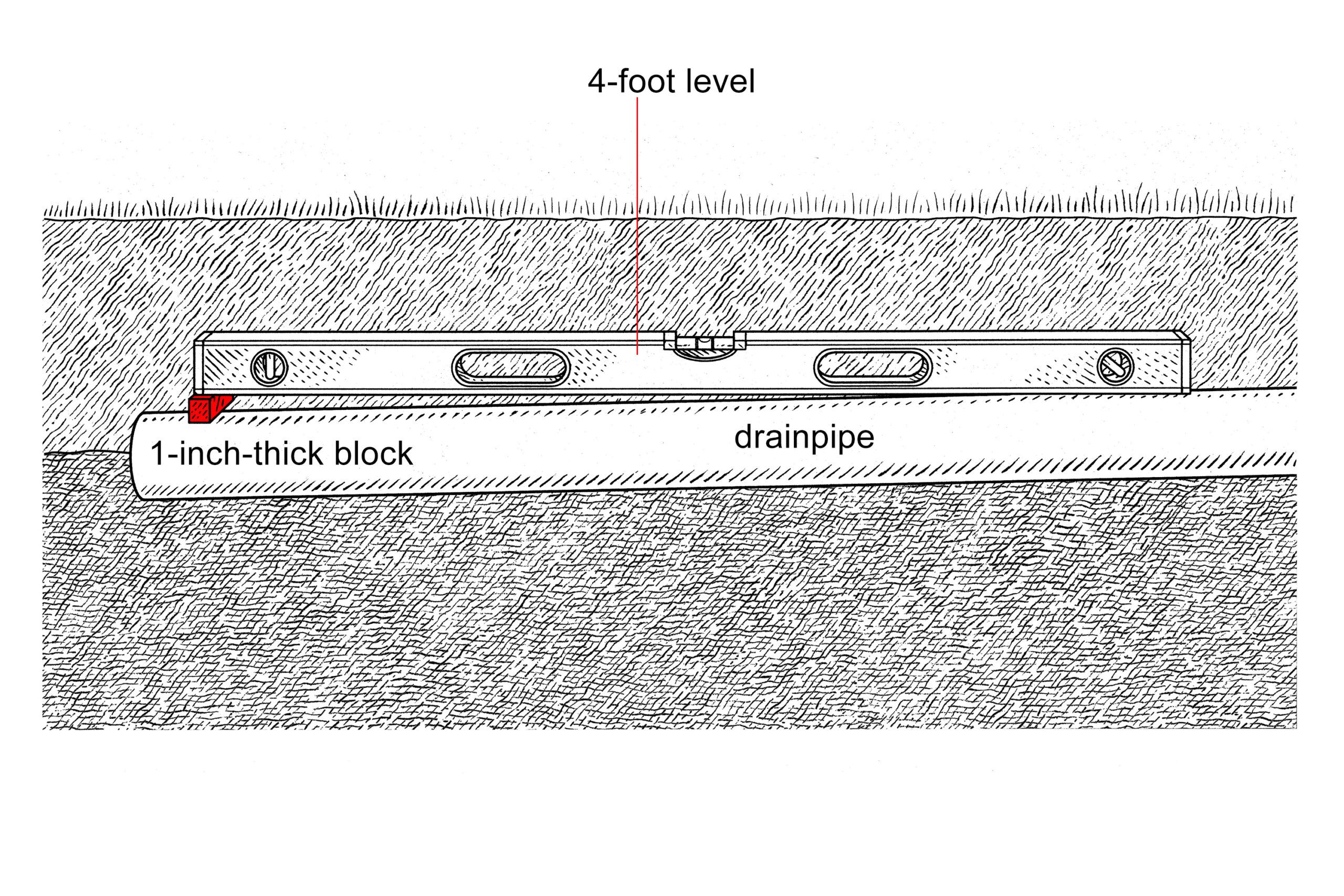
Q: I have to connect my downspout to a dry well. How much should I pitch the pipe that leads to the dry well?
—Archibald Smart, Washington, D.C.
A: The standard pitch for most things that depend on gravity to shed water—drainpipes, patios, porch decks, and gutters, to name a few—is 1⁄4 inch per foot. And here’s a trick that makes it easy to determine whether something has that pitch. Hot-glue a narrow 1-inch block to one end of a 4-foot level. Then simply place the block on the lower end of the slope and adjust things until the bubble reads level. The surface that the level is resting on will be at the proper pitch.
Drilling into Steel: Step 1
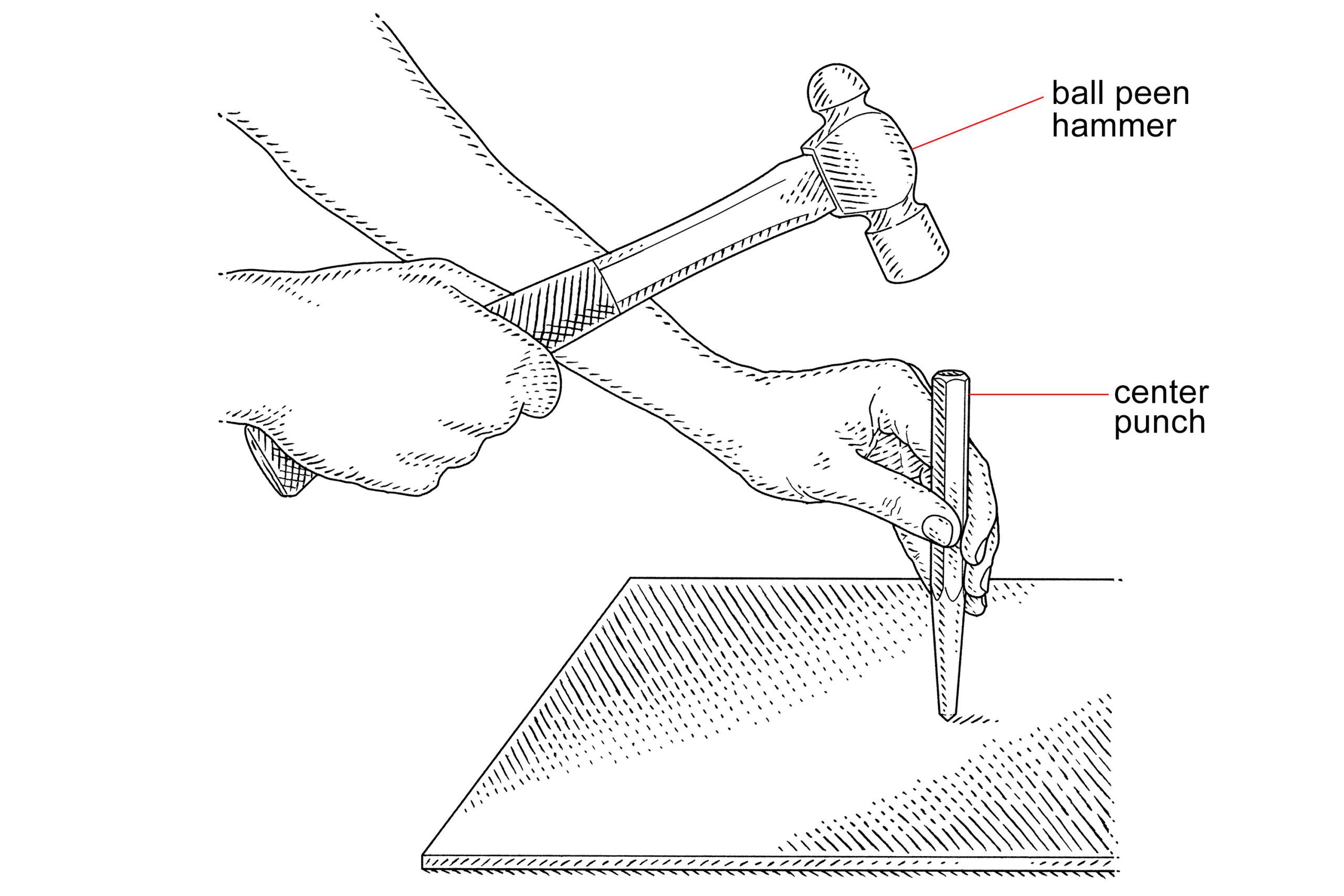
Q: Whenever I try drilling into steel, the bit skates around on the surface before it bites in. What can I do to keep that from happening?
—Bill Fuller, Larchmont, NY
A: Steel certainly is not as obliging as wood, but with the right technique, you can drill through it fairly easily using ordinary high-speed-steel bits. Here are the basics, which will work no matter what kind of metal you’re drilling into.
Dimple. First put on safety glasses, then give a center punch a sharp tap with an engineer’s or ball peen hammer (shown). The punch creates a small dimple in the surface of the metal that will keep the tip of the bit from wandering so it can chew into the metal. By the way, there’s a good reason to use those specialized hammers. Center punches are made of hardened steel, which can shatter regular nailing hammers.
Drilling into Steel: Step 2
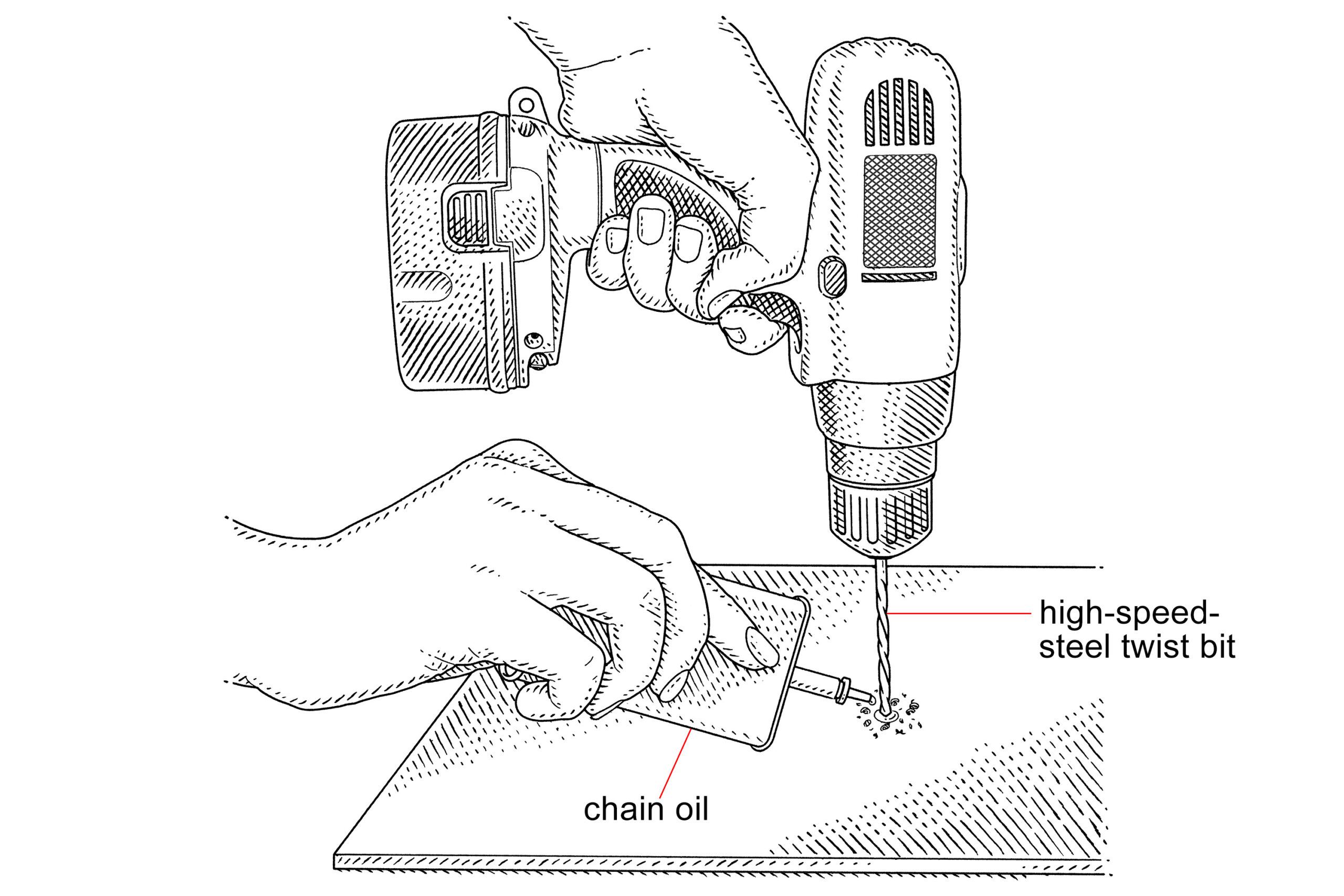
Drill. Before you start, put on safety glasses— bits can break or fling razor-sharp filings. As you drill, use a slow speed and apply light to moderate pressure. Too much muscle or too high a speed will cause the bit to overheat, lose its temper, and stop cutting. Adding a drop or two of chain oil will help keep the bit cool, too. If progress is too slow, drill a smaller hole first, then step up to the size you want.
Accurate No-Gap Miters: Step 1
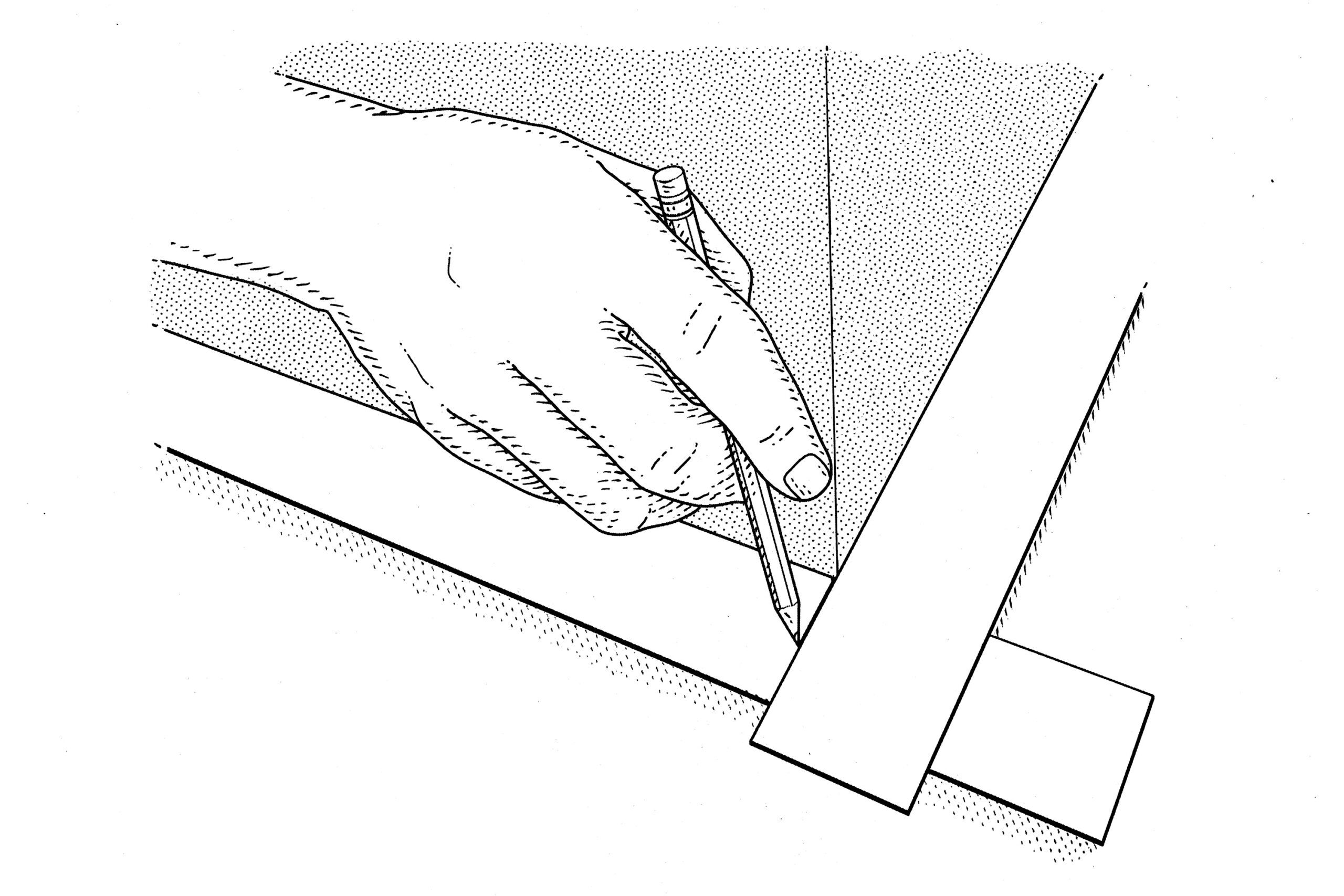
Q: The corners in my house aren’t square. How can I make accurate outside-corner miter cuts in quarter-round baseboard trim?
—Julia Hrubiak, Amherst, NY
A: To cut a no-gap miter, you need to bisect the angle formed by an outside corner. Here’s a simple way to do that using strips of posterboard and a sliding T-bevel. This technique also comes in handy with other kinds of trim, including crown molding. In that case, hold the strips in place on the ceiling with double-sided mounting tape.
Overlap the strips. Cut two 24-inch-long pieces of posterboard into strips exactly the same width, about 2 inches across. Place one against each side of the wall, with their ends overlapping at the corner. Mark two parallel lines on either side of the bottom strip, as shown, using the edges of the top strip as a guide.
Accurate No-Gap Miters: Step 2
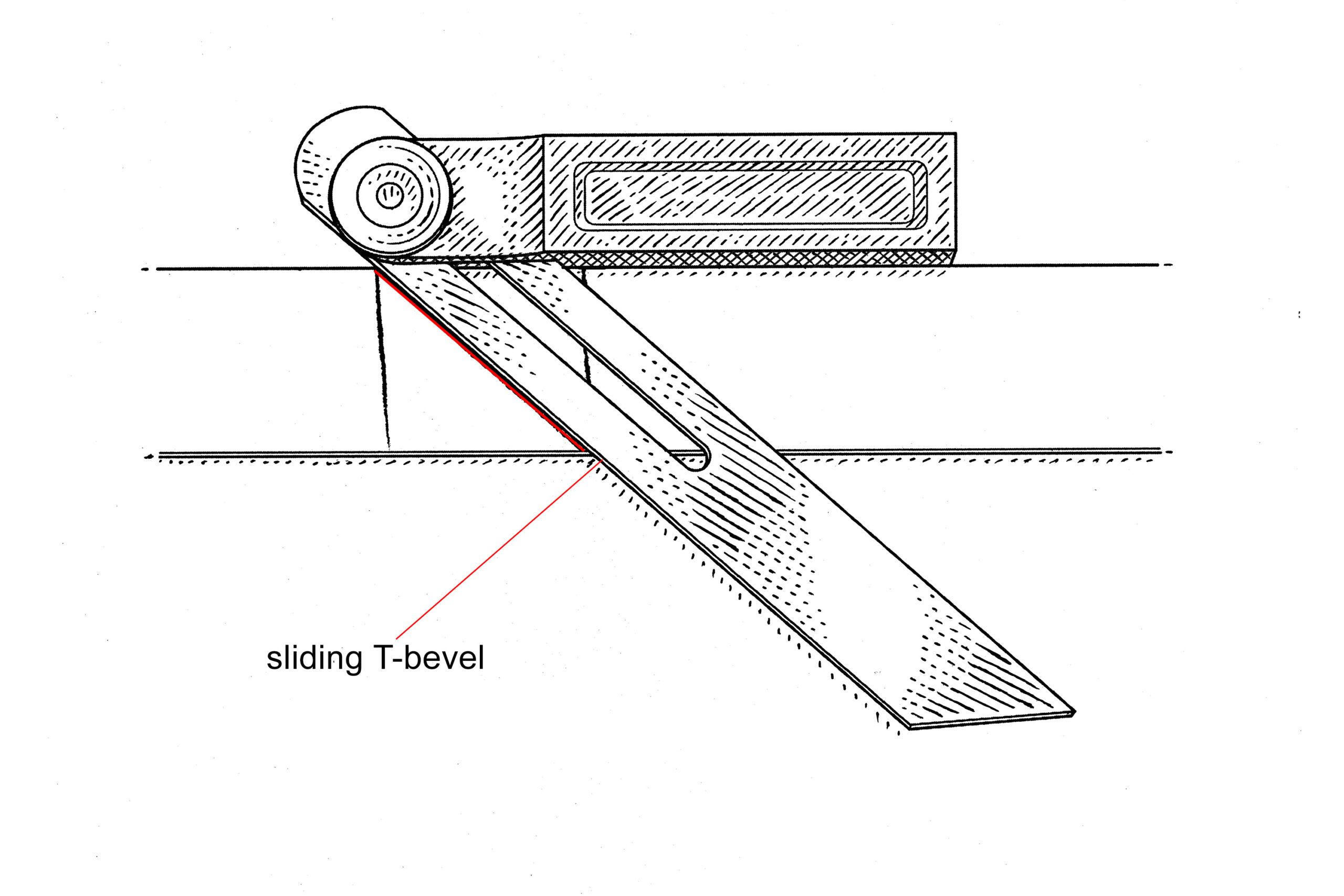
Find the cut angle. Take the bottom strip and draw a line from the point on the edge that touched the wall to the point diagonally across from it on the strip’s opposite edge. That diagonal line shows the angle of the cut. Rest the handle of a sliding T-bevel against one edge of the strip and line up its blade with the diagonal, as shown.
Accurate No-Gap Miters: Step 3
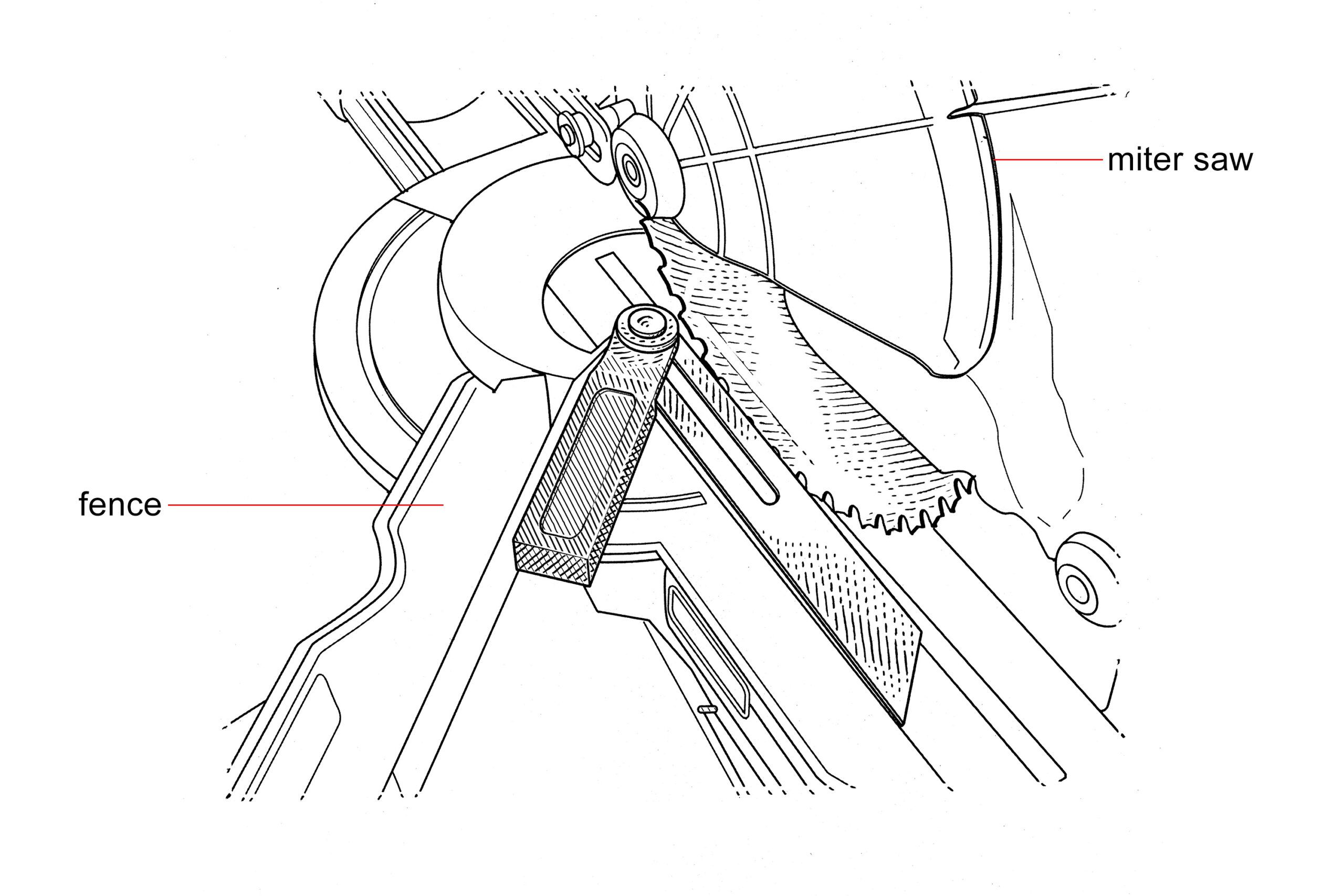
Set the saw blade. Place the handle of the T-bevel against the miter saw’s fence and pivot the blade until its teeth touch the T-bevel, as shown. Note the angle on the miter scale so that you can set the blade at the same angle for right- and left-hand cuts. When the mitered pieces come together, they’ll make a perfect, gap-free joint.