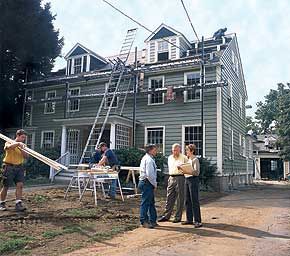
Since May, This Old House general contractor Tom Silva and his crew of carpenters have been working on the TV project house in Winchester, Massachusetts, building a new kitchen addition and sunroom, reconfiguring the master bedroom suite and basement media room, and beefing up weakened or undersized parts of the original structure. As autumn gives way to winter and the rough carpentry is finished, Tom has put down his tool belt (for awhile, at least) so that he can orchestrate the next phase of the remodeling process. “When the framing is all done, “says Tom, “the subcontractors arrive.” Plumbers, electricians, plasterers, and roofers have descended on the house, and the property is swarming with subs.
The job is far from over, and there are still plenty of decisions to be made — Tom and other members of the TOH team confer almost daily with homeowners Kim Whittemore and Bruce Leasure. Says Tom of the hubbub at the house: “Everybody here is real good at their job. The hardest thing is keeping them out of each others’ way.”
Metal and Asphalt Roofing
Most of the roof is being covered in architectural asphalt shingles, a durable and inexpensive roofing material. But asphalt is not recommended for a roof with a pitch shallower than 4 in 12 (meaning for every horizontal foot the roof covers, it rises 4 inches) because wind and rain can force their way underneath. So on the kitchen addition, Tom Silva called for a metal roof. The roofers soldered together sheets of lead-coated copper over the plywood sheathing to form an impermeable barrier against the elements, then added integral lead-coated copper gutters with decorative copper hangers. “The asphalt has a 40-year warranty,” says Tom. “The metal will probably last into the next century.”
Insulation Inspection
Buttoning up the house against cold New England winters (and the occasional scorching summer day) requires a tight and thorough insulation barrier. It’s also a requirement of the Massachusetts building code, which is why an inspector showed up to meet with Tom and verify the completion of the installation, peering into walls and crawl spaces to examine the goods. Tom used two types of insulation: blown-in mineral wool for the walls and sprayed-on Icynene foam on the underside of the roofs. “Mineral wool has excellent insulating abilities, but if you use it on the underside of a roof, it has to be vented, just like fiberglass batts,”he explains. “We could have put in roof ridge and soffits vents, but by using the Icynene, which doesn’t need venting, we saved some money in the long run.”
Planting Trees
TOH landscape contractor Roger Cook to the rescue: To screen out the new neighbors after they cut down all the trees on their side of the backyard property line, Roger and crew planted three blue spruces, six giant western red cedars, and seven pyramidal white pines — chosen for their shape and dense foliage. The effect on viewing the neighbor’s house, as Roger puts it: “Now you see it, now you don’t.”
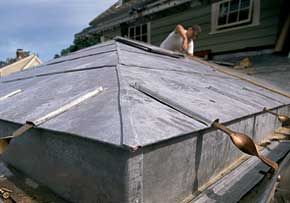
Skim-Coat Plastering
Only the renovated master bedroom and kitchen needed new walls, so Kim and Bruce decided to go with plaster, to match the rest of the house. (The media room gets drywall, which doesn’t echo as much.) So master plasterer Steve Norton and his crew troweled on a 1/8-inch coat of veneer plaster over blueboard. “It’s a much harder wall than regular drywall,” says Norton. “And with a full coat covering everything, it’s unlikely you’ll ever see a seam or a popped nail like you sometimes do with drywall.”
Sunroom Trim
To replicate the decorative exterior panels under the new sunporc’s double-hung windows — rectangular “spider webs” of applied 1×2 redwood pieces — Silva Brothers carpenter Tim Oglesby built a jig to make the job go faster. “It took about an hour to lay out and build the jig with perfectly square corners, stops for the 16 pieces, and the nearly three dozen saw cuts that make up each panel,” says Oglesby. “But then, all I had to do was cut a series of identical pieces and drop them in place, kind of like a big jigsaw puzzle.” When a panel was complete, Oglesby simply nailed the pieces in place. The finished design will be primed and painted the same cream color as the rest of the exterior trim.
Wiring the House
The confusing ganglion of roughed-in wires and cables in the Winchester basement utility room will eventually send signals and currents throughout the house. Along with standard electrical wiring, electrician Allen Gallant and his crew strung Category 5 cable for Internet and phone lines to every room. Gallant’s favorite device is a $300 whole-house surge protector. “Most everybody uses a plug-in surge protector for their computer,” Gallant says. What they don’t realize is that most new appliances also have electronic circuitry, and without whole-house protection, one lightning strike or return from a power outage could take out your refrigerator, oven, and home theater system.”
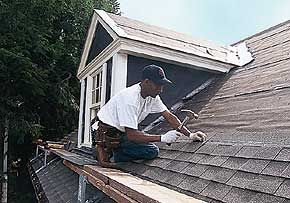
Assessing the Floors
“You never know what you’ll find when you rip up an old carpet,” said Tom Silva, eyeing the filthy beige wall-to-wall that covered the living room and dining room floors. His hope was that there would be gold underneath: strip oak floors, which were popular in 1920s Colonial Revivals like the Winchester house. So he lifted a corner in the front hall, and with a wipe of paint thinner dissolved years of grime and old wax to find glowing oak underneath. “I know we’ll have to replace some boards, and put in some patches,” he said. “But after a light sanding and a couple of coats of finish, this will be beautiful.”
Radiant Heat Prep
Before master plumber Ronald Coldwell could retrofit radiant heating under the first story’s floors, he had to get one thing out of the way. Well, actually, hundreds of things: sharp-edged cut nails, used to install the original flooring, that were poking through the bottom of the floorboards right where the heating’s plastic PEX tubing was to run. It took Coldwell a full day to cut the 400 nails with an angle grinder. As he put it, “Some days my job is lots of fun. Others, it’s a real grind.”
Sizing a TV Screen
Planning the media room in the refurbished basement of the Winchester house is more than just wiring the room for sound. Kim had to consider the size of the TV screen, because that dictates how far away the seating should be for optimum viewing. (A good rule of thumb: Viewer distance from the TV should be equal to twice the diagonal measurement of the screen.) So Kim marked the wall with the outlines of five different sizes of flat-screen plasma televisions and then measured recommended seating distances. In the end, she and Bruce settled on the smallest, a 42-inch screen, which gave them cozy seating that makes good use of the tight space. “The cost was also a plus,” she says. “The bigger the screen, the higher the price tag. There may be optimum seating distance, but we were also thinking optimum checkbook balance.”
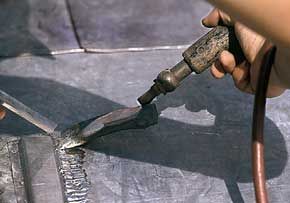
Where to Find It
Plaster contractor:
Stephen Norton
Stephen’s Plastering
Winchester, MA
718-721-7315
Electrician:
Allen Gallant
Gallant Electric
Lexington, MA
781-862-4636
Landscape Contractor:
Roger Cook
K & R Tree and Landscape
Burlington, MA
781-272-6104
Master Plumber:
Ronald Coldwell
Trethewey Brothers Inc.
Roslindale, MA
617-325-3283
Architectural sheet metal:
Yankee Steeplejack Company
Canton, MA
781-821-1003
Plasma screen TV:
Plasma WEGA
Sony Style USA,
Sony Electronics e-Solutions Company LLC
877-865-7669
Our thanks to:
Kostas Reissis
Audio Visions
Woburn, MA
877-283-4681